Abschnitt 4.3 - 4.3 Dimensionierung
Absauganlagen erfüllen als "Anlagen" nur dann die ihnen zugedachten Aufgaben und genügen den betrieblichen Erfordernissen, wenn sie insgesamt auf die jeweiligen Randbedingungen abgestimmt und dafür ausgelegt sind. Um das zu gewährleisten, bedarf es schon in der Planungsphase der intensiven Zusammenarbeit zwischen der Firma, die die Anlagen errichtet und dem späteren Betreiber.
Dem Betreiber kommt dabei die Aufgabe zu, den Hersteller über Art, Umfang und Lage der Emissionsquellen innerhalb der Betriebsgebäude zu informieren und ihm den später vorgesehenen Betrieb der Anlage sowie die örtlichen Möglichkeiten zur Aufstellung der Anlagen-Komponenten offen zu legen. Der Hersteller ist für die Auslegung, technische Umsetzung, Montage vor Ort und Übergabe der Anlage an den Betreiber verantwortlich.
Der bedarfsgerechten Dimensionierung der Anlage kommt dabei für den wirkungsvollen, sicheren, störungsarmen und energieeffizienten Betrieb eine entscheidende Rolle zu.
Folgende Anlagen-Komponenten müssen bei Absauganlagen dimensioniert werden:
Erfassungselemente (sofern nicht Bestandteil abzusaugender Bearbeitungsmaschinen, etc.)
Rohrleitungsnetz
Abscheider
Ventilatoren
Leitungen/Kanäle zur Abluftführung
Elemente zur Steuerung/Regelung des Anlagenbetriebs
Bauteile zur Überwachung des Anlagenbetriebs und zur Gewährleistung der Anlagensicherheit
Nachfolgend werden die Vorgehensweise bei der Dimensionierung sowie die wesentlichen Zusammenhänge und gegenseitigen Abhängigkeiten beschrieben.
4.3.1
Grundsätzliche Vorgehensweise
Zentrale Aufgabe einer Absauganlage ist die Erfassung der im Arbeitsbereich oder in einer Bearbeitungsmaschine anfallenden Schadstoffe, deren Entfernung vom Arbeitsplatz oder aus der Maschine, die Separierung des Schadstoffs vom Transportmedium "Luft" sowie bei Bedarf dessen zeitweilige, gefahrlose Zwischenlagerung für eine spätere Weiterbehandlung. Im Fokus der Dimensionierung stehen daher vor allem die dafür benötigten Erfassungs- und "Transport"-Luftmengen sowie Art und Leistung des benötigten Abscheiders und die erforderliche Behandlung der Abluft.
Anschließend werden anhand eines Betriebs-Layouts die Standorte der Absaugstellen mit dem zugeordneten Volumenstrom- und Druckbedarf, die Standorte der Abscheider sowie der Einrichtungen zur Zwischenlagerung (eventuell auch Weiterbehandlung) der Schadstoffe festgelegt.
Erst danach erfolgen die Überlegungen zur Wahl der im konkreten Fall technisch und wirtschaftlich sinnvollsten Anlagenbauart und zur Gestaltung der Transportwege, also des Rohrleitungsnetzes. Aufgrund der gegenseitigen Abhängigkeiten der für den späteren Betrieb wesentlichen Anlagen-Parameter, wie Luftgeschwindigkeiten, Druckverluste, Abscheider-Belastungen, erforderliche Ventilator-Leistungen und Einrichtungen zur Überwachung und Steuerung sowie der erforderlichen Einrichtungen zur Gewährleistung der Anlagen-Sicherheit etc. erfolgt dieser Dimensionierungsschritt im Regelfall iterativ. Dabei werden die verschiedenen Varianten planerisch und rechnerisch "durchgespielt" und die Ergebnisse für die Anlagenleistung, die erforderlichen Investitionen und die zu erwartenden Betriebskosten bewertet. Diese Vorgehensweise ermöglicht die Herausarbeitung spezifischer Vorzüge und Nachteile der unterschiedlichen Varianten und führt im Ergebnis so zu der für den konkreten Fall optimierten Lösung.
Abschließend wird die gewählte Lösung darauf geprüft, wie die Anlage sich voraussichtlich in allen für den späteren Betrieb wesentlichen Anlagen-Zuständen und bei Störungen verhält und welche Leistungsreserven für eventuelle spätere Anlagenerweiterungen vorhanden sind; die Flexibilität und die Kosten- und Energieeffizienz werden bewertet.
Im Diagramm in Abbildung 4.3.1 ist die grundsätzliche Vorgehensweise bei der Anlagen-Dimensionierung mit dem Ziel einer optimalen Lösung für den konkreten Fall dargestellt.
4.3.2
Bestimmung der Absaugleistung
Die Absaugleistung ist die zentrale Planungsgröße bei der Dimensionierung einer Absauganlage. Sie umfasst alle für die Anlage wesentlichen Parameter, nämlich:
den erforderlichen Mindest-Volumenstrom zur Erfassung und zum störungsfreien Abtransport der abzusaugenden Schadstoffe an oder von den Emissionsorten,
die erforderlichen Druckdifferenzen zur Aufnahme der Schadstoffe und zur Überwindung von Strömungswiderständen innerhalb der Anlage,
die technologisch erforderlichen (sog. Beiluft-Volumenströme, hydraulischer Abgleich, Schadstoffzustand oder -verhalten) oder aus betrieblichen Gründen gewünschten Reserven (Volumenstrom und Druckdifferenz) für den späteren Anlagenbetrieb.
Planerinnen und Planer müssen bei der Festlegung der Absaugleistung vom späteren Betreiber unterstützt werden. In der Gefährdungsbeurteilung muss ermittelt werden, wo, unter welchen Umständen und in welcher Form Schadstoffe im Betrieb auftreten (können), die über die Absaugung erfasst und aus dem Arbeitsbereich beseitigt werden müssen. Dabei müssen alle betrieblichen Prozesse (Fertigung, Lagerung, Bearbeitung, etc.) in Bezug auf das mögliche Auftreten des abzusaugenden Schadstoffs analysiert und bewertet werden.
4.3.2.1
Stoffeigenschaften und -mengen
Folgende Stoffeigenschaften bestimmen wesentlich die Anforderungen an die zu planende Absauganlage:
Aggregatzustand
Gewicht/Dichte
Partikelgröße
Eigendynamik
Brennbarkeit
Explosionsfähigkeit im Gemisch mit Luft
Gesundheitsschädliche Eigenschaften (KMR-Stoffe, Arbeitsplatzgrenzwerte, Emissionsgrenzen)
Nähere Informationen zu den Stoffeigenschaften finden Sie in Abschnitt 3.1.
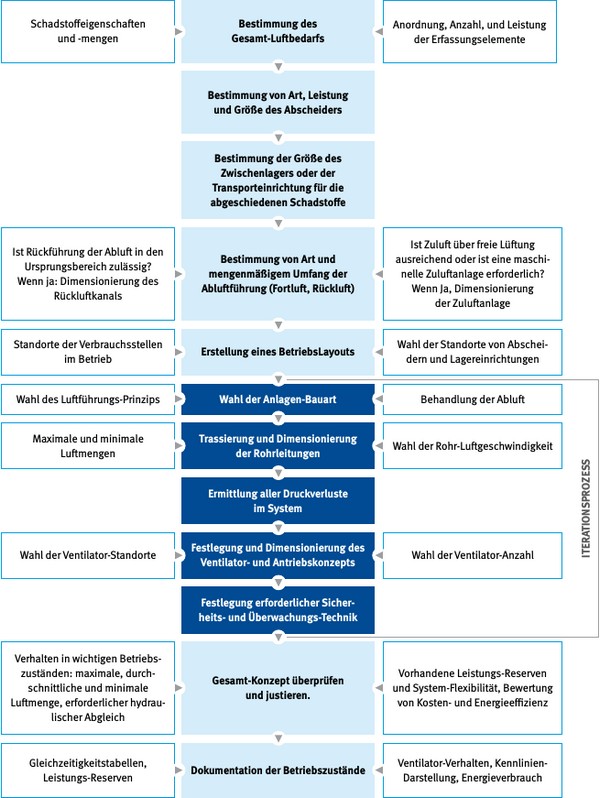
Abb. 4.3.1
Vorgehensweise bei der Dimensionierung von Absauganlagen
Die zu erwartende Stoffmenge muss für die weitere Dimensionierung abgeschätzt werden. Für diese Abschätzung stehen verschiedene Verfahren zur Verfügung:
Erfahrungswerte aus existierenden, vergleichbaren Anlagen
Überschlagsrechnungen, z. B. zu Zerspanungsleistungen
Bilanzrechnungen aus eingesetzten Betriebsstoffen
Hochrechnungen aus Emissionsraten oder Prozessparametern
4.3.2.2
Anordnung, Anzahl und Leistung der Erfassungselemente
Sind für die abzusaugenden Schadstoffe Art, Menge und Ort des Auftretens im Betrieb ermittelt, können die Erfassungen festgelegt und zugeordnet werden. Die Dimensionierung der Erfassungen umfasst dabei folgende Gesichtspunkte:
Anordnung und Geometrie der Erfassungselemente
notwendige Erfassungsluftgeschwindigkeit/Volumenstrom (unter Berücksichtigung des Gesundheits- und des Arbeitsschutzes)
dabei erforderlicher Unterdruck an der Schnittstelle zur anschließenden Rohrleitung.
Erfassungseinrichtungen können als geschlossene, halboffene oder offene Systeme konstruiert sein. Näheres dazu ist in Abschnitt 3.2. beschrieben.
4.3.2.3
Ermittlung des Gesamt-Volumenstrombedarfs
Nach Festlegung der zu treffenden Einzel-Maßnahmen zur Erfassung der Schadstoffe ist der Gesamtbedarf an Volumenstrom für die zu dimensionierende Anlage zu ermitteln. Dieser Gesamt-Volumenstrombedarf stellt das entscheidende Kriterium für die spätere Größe der Anlage, die Auslegung von Abscheidern, Zwischenlagern, Abluftleitungen und Ventilatoren dar. Er ist damit maßgebend für Kosten für Investitionen und Betrieb der späteren Anlage.
Zur Ermittlung des erforderlichen Bedarfs an einzelnen Emissionsstellen müssen folgende Parameter festgelegt werden:
- 1.
Volumenstrom V̇ in m3/h
- 2.
Luftgeschwindigkeit w an der Schnittstelle zwischen Erfassungselement und Rohrleitung in m/s
- 3.
Querschnittsfläche A in m2 bzw. Durchmesser D am Anschlussstutzen des Erfassungselements in m
- 4.
erforderliche Druckdifferenz Δpstat gegen Umgebung (Unterdruck) in Pa zur Erzielung der gewünschten Luftgeschwindigkeit
Der Gesamt-Volumenstrombedarf ist nicht allein die Summe der Bedarfe an allen Erfassungsstellen. Auch der Anlagenbetrieb muss berücksichtigt werden. Das betrifft vor allem den gleichzeitig erforderlichen Betrieb der Anlage an mehreren Erfassungsstellen. Darüber hinaus muss es Leistungsreserven geben für den nachträglichen Anschluss weiterer Erfassungsstellen, sowie anlagentechnologisch vorzuhaltende Leistungsreserven (z. B. Beiluft-Mengen zur Vermeidung von Ablagerungen oder Luftleistungen für den sogenannten hydraulischen Abgleich).
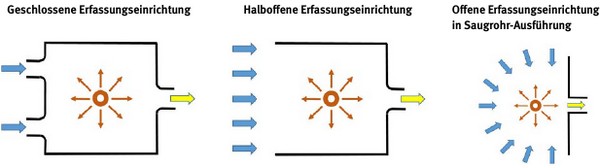
Abb. 4.3.2
Erfassungssysteme für Schadstoffe
Es müssen auch Leistungsreserven vorhanden sein, die rechnerische Unsicherheiten (z. B. bei der Ermittlung des Anlagen-Verhaltens) kompensieren. Man kann zum Beispiel wegen Montageungenauigkeiten nicht davon ausgehen, dass die rechnerische Annahme einer "Stoffdichtigkeit" der Anlage vollständig gegeben ist.
In der Regel wird der Volumenstrombedarf aus gleichzeitigem Betrieb mehrerer Verbraucher den wesentlichen Eckpunkt für die Größe der zu projektierenden Anlage geben. Für den späteren Betrieb sind aber nicht nur der maximale Bedarf aus gleichzeitigem Betrieb, sondern auch weitere Betriebszustände von Interesse. Solche "Eck-Betriebspunkte" für die Anlage stellen dar:
Maximaler Volumenstrombedarf: Er bestimmt die erforderlichen Größen und Leistungen der Abscheider, Lagerbereiche, Abluftkanäle, und Ventilatoren. Auch die Auslegung des Rohrleitungsnetzes wird wesentlich von diesem Bedarf mitbestimmt. Außerdem sind auf diesen Betriebszustand alle wesentlichen Sicherheitsbauteile, Steuerungseinrichtungen sowie die Energieversorgung auszulegen.
Minimaler Volumenstrombedarf: Er gibt Anhaltspunkte für das geforderte Absaugspektrum und damit für die vorteilhafte Anlagen-Bauart. Daneben ist er eine wesentliche Größe für die Auslegung des Rohrleitungsnetzes, die Abstufung der Ventilatoren und Antriebsleistungen, die Ausrüstung mit Beiluftklappen oder Schiebersteuerung und die durch die Anlagensteuerung einzuleitenden Maßnahmen.
Durchschnittlicher Volumenstrombedarf: Er beeinflusst wesentlich den späteren Energieverbrauch, die voraussichtliche Standzeit des ausgewählten Filtermaterials, die Auslegung der Abreinigung des Filters und die Auslegung einer vorhandenen Ventilator-Abstufung. Auf diesen durchschnittlichen Bedarf (inkl. einer vorgewählten Streuung) wird die Anlage im Regelfall optimiert.
Der gleichzeitige Volumenstrombedarf Vges bestimmt sich aus der Summe der jeweils erforderlichen Volumenströme Vi an den einzelnen Anschlussstellen.

Hinweise für die mögliche Gleichzeitigkeit können gegeben sein durch:
die Zahl der maximal gleichzeitig anwesenden Beschäftigten (mehr von Hand bediente Maschinen können nicht gleichzeitig betrieben werden),
die Produktpalette und die Fertigungsschwerpunkte des Betreibers,
das Vorhandensein mehrerer baugleicher Maschinen/Emissionsquellen,
die Auswertung über evtl. vorhandene Betriebsstundenzähler.
Erfahrungen zeigen, dass in der Praxis die Anlagengrößen eher überdimensioniert (Viel hilft viel!) und die im Betrieb benötigten Gleichzeitigkeiten tendenziell überschätzt werden.
Bei der Planung sollten 10 % Leistungsreserven berücksichtigt werden, um zum Beispiel Undichtigkeiten, Ungenauigkeiten in der Auslegung und Montage auszugleichen.
Die Notwendigkeit von weiteren Leistungsreserven ergibt sich aus für spätere Zeitpunkte vorgesehenen Erweiterungen der Anlage. Der daraus resultierende Zusatzluftbedarf sollte nur für die Dimensionierung der Abscheider und Abluftkanäle berücksichtigt werden. Im Bereich des Leitungssystems und der Ventilatoren würden sich für den aktuellen Zustand bei Berücksichtigung dieses Zusatzbedarfes unter Umständen Funktionsstörungen (z. B. Ablagerungen) ergeben. Leitungssystem und Ventilatoren müssen dann im Rahmen der Erweiterung der Anlage überarbeitet werden
Hinweis: |
---|
Mithilfe von Anhang 8.5. kann eine Zusammenstellung des Gesamt-Volumenstrombedarfs einer Absauganlage erfolgen, aus der auch die Bedarfe in unterschiedlichen Anlagen-Betriebszuständen hervorgehen. |
4.3.3
Bestimmung von Art, Leistung und Größe des Abscheiders
Liegen die benötigten Volumenströme und Schadstoffmengen fest, muss zunächst das richtige Abscheidekonzept gefunden und festgelegt werden. Dazu muss bestimmt werden, welche Bauart von Abscheidern für die Art, den Zustand und die Menge des abzuscheidenden Schadstoffs geeignet ist. Anschließend erfolgt die Dimensionierung des Abscheiders, die Wahl des Abscheidemediums und die Festlegung der Größe. Berücksichtigt werden müssen hierbei auch die vorgesehene Abscheider-Regeneration (soweit erforderlich) sowie die Art der Abführung und Entsorgung der abgeschiedenen Schadstoffe.
4.3.3.1
Bestimmung des Abscheideprinzips
Für die Wahl des Abscheide-Prinzips sind der Aggregatszustand des Schadstoffs, dessen Lösung in der Transportluft und die physikalischen und chemischen Eigenschaften von Bedeutung.
Der Schadstoff kann auftreten:
in Form von gröberen oder feineren Partikel von Feststoffen
in Form eines Aerosols als heterogenes Gemisch aus Luft und feinen Fest-Partikeln oder flüssigen Tröpfchen
in Form von Dämpfen
in rein gasförmigem Zustand
Daneben spielen folgende Eigenschaften für die Wahl des Abscheiders eine wesentliche Rolle:
die Rohluft-Temperatur,
die elektrostatischen Eigenschaften des Schadstoffs,
die Verklebung von Partikeln untereinander (Agglomeration),
die Rohluft- Schadstoff-Feuchtigkeit,
die Brennbarkeit oder Explosionsfähigkeit des Schadstoff-Luft-Gemischs,
die Rohluft-Beladung (Menge der Schadstoffe im Luftstrom) sowie
die jeweils zulässige Reinluft-Konzentration.
Bei partikelförmigen Stoffen richtet sich die Abscheidetechnik im Wesentlichen nach der Partikelgröße (siehe Abbildung 4.3.3). Ist die Rohgasbeladung hier sehr hoch (> 100 g/m3) oder enthält sie für die Abscheidung unerwünschte Produkte (z. B. Metallteile, größere Werkstoffteile, Funken), empfiehlt sich die Anwendung mehrstufiger Abscheidekonzepte.
Geeignete Vorabscheider können sein:
Schwerkraftabscheider (z. B. Absetzkammern) zur Vorabscheidung größerer Partikel oder Fasern,
Prallabscheider zur Abscheidung z. B. auch von möglichen Funken im Rohluftstrom,
Magnetabscheider zur Ausschleusung von Metallteilen,
Zyklone (Zentrifugalabscheider/Fliehkraftabscheider) zur Vor-Sedimentierung größerer Staubmengen für Volumenströme bis 100.000 m3/h.
Die Abscheideleistung der genannten Abscheider ist aber besonders im Bereich feinerer Partikel nicht ausreichend, sodass im Regelfall ein alleiniger Einsatz nicht genügt. Sie können den Hauptabscheider aber entscheidend entlasten und dessen Standzeit deutlich verlängern.
Nachteilig beim Einsatz von Vorabscheidern ist allerdings ihr Strömungswiderstand, der zusätzliche Druckverluste verursacht und damit einen höheren Energieaufwand beim Betrieb der Anlage nach sich zieht.
Nähere Einzelheiten sind dem Abschnitt 3.5 zu entnehmen.
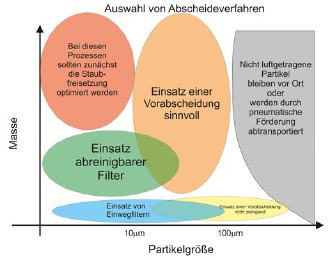
Abb. 4.3.3
Abscheideverfahren für Partikel
4.3.3.2
Dimensionierung des Abscheiders (Größe)
Liegen Art und Funktionsweise des Abscheiders fest, kann der Abscheider dimensioniert werden.
Bemessungsgrößen sind bei den weit verbreiteten filternden Abscheidern vor allem der (maximale) Rohluft-Volumenstrom V̇ (m3/h) und bei partikelförmigen Schadstoffen die für einen störungsfreien Betrieb jeweils maximal zugrunde zu legende Filtrationsgeschwindigkeit vf (m/h) oder Filterflächenbelastung f (m3/(m2 · h)).
Die notwendige Filterfläche AF (m2) ergibt sich dabei aus der Beziehung:

Die Wahl der Filtrationsgeschwindigkeit hängt wesentlich von der vorgesehenen Regenerations-Technik, der Bauart des Abscheiders (Schlauch-, Taschen- oder Patronenfilter), dem Filtermaterial sowie der Struktur und Korngrößenverteilung des Schadstoffs in der Luft ab. Sie beträgt zwischen 30 und 300 m/h. Auch die Wirksamkeit der Vorabscheidung sowie die geometrischen Verhältnisse im Abscheidebereich (Länge/Durchmesser-Verhältnis oder Lichtweiten zwischen den Filterschläuchen) spielen für die Wahl der Filtrationsgeschwindigkeit eine Rolle.
Abschnitt 3.5. gibt Hinweise für übliche Filtrationsgeschwindigkeiten bei verschiedenen Anwendungsbereichen.
Generell sollte die Filtrationsgeschwindigkeit eher geringer gewählt werden. Das führt zwar im Ergebnis zu größeren Abscheider-Abmessungen (und damit höheren Investitionskosten), bringt aber dem Betreiber für den späteren Betrieb deutliche Vorteile:
geringere Druckverluste im Abscheider und damit geringere Energiekosten,
längere Filterstandzeiten und damit geringere Wartungskosten,
längere Regenerations-Zyklen und dadurch wiederum geringere Energie-Aufwendungen.
Außerdem ist der Abscheider meistens das Bauteil innerhalb der Anlage, das die Leistungsreserven für später vorgesehene Anlagenerweiterungen definiert und damit wesentlich über die Flexibilität der Gesamt-Lösung entscheidet.
Aufgrund der Komplexität der Thematik können an dieser Stelle nur die weit verbreiteten filternden Abscheider angesprochen werden. Ausführungen zur oder Hinweise für die Dimensionierung anderer Abscheider sind der einschlägigen Fachliteratur [30] zu entnehmen.
4.3.3.3
Wahl der Regenerations-Technik und -Intervalle
Die möglichen Regenerations-Techniken sowie die für die Regeneration erforderlichen Intervalle hängen unmittelbar mit dem gewählten Abscheidesystem zusammen. Bei manchen Systemen ist eine Regeneration im eigentlichen Sinne gar nicht möglich, sodass in diesen Fällen die "Regeneration" aus einem Austausch des Filtermediums besteht. Zu nennen wären in diesem Zusammenhang:
Speicherfilter bei filternden Abscheidern
Anlagerung von Stoffen an der Oberfläche von z. B. Aktivkohle als Adsorbens
Lösen von Stoffen in Waschflüssigkeiten als Absorbenzien
Waschflüssigkeiten bei Nassabscheidern
Zyklone und alle Schwerkraftabscheider benötigen gar keine Regenerations-Technik. Hier müssen allenfalls die Sammelbehälter in Abständen mechanisch oder von Hand geleert werden, sofern das Material nicht in zentrale Fördersysteme aufgegeben wird.
Bei filternden Abscheidern stehen prinzipiell 3 Verfahren zur Wahl:
Mechanische Rüttelung
Spülluftverfahren
Druckimpuls-Verfahren
Mechanische Rüttelung eignet sich nur für geringe Filterbelastungen bei flexiblem, unbeschichtetem Filtermaterial. Die Rüttelung kann nur in Betriebspausen erfolgen. Im Gegensatz dazu sind bei der Spülluft-Abreinigung keine Betriebsunterbrechungen erforderlich, weil sie nur auf aktuell nicht mit Rohgas beaufschlagte Segmente angewendet wird. Allerdings sind bei dieser Lösung größere Filterflächen (ein Segment befindet sich immer im Abreinigungsmodus) sowie relativ große Luftmengen erforderlich. Druckimpuls-Verfahren sind auch bei hoch belasteten und beschichteten Filtermaterialien wirkungsvoll bei gleichzeitig relativ geringem Luftbedarf. Nachteilig ist die Notwendigkeit der Druckluftversorgung über einen betrieblichen Kompressor.
4.3.3.4
Festlegung des Entsorgungskonzepts
Für das Entsorgungskonzept spielt - neben der aus der Abscheidung anfallenden Schadstoffmenge - vor allem der Aggregatzustand der abgeschiedenen (Rest-)Stoffe die wesentliche Rolle.
Partikel fester Stoffe können über mechanische Austragsysteme (Schnecken, Zellenradschleusen, etc.) aus dem Filter ausgetragen werden und einer (Zwischen-)Lagerung in Behältern zugeführt werden.
Flüssigkeiten können aus dem Abscheider abfließen und mit Pumpen in Lagertanks oder direkt zur (Abwasser-) Aufbereitung gefördert werden. Bei der Abwasseraufbereitung kommen in vielen Fällen Oxidantien zur Ausfällung der Schadstoffe aus dem Abwasser und Säuren oder Laugen zur Einstellung eines zulässigen pH-Werts zum Einsatz, bevor das Abwasser in das öffentliche Kanalnetz oder einen natürlichen Vorfluter geleitet werden kann. Der anlagentechnische und rohstofftechnische Aufwand darf dabei nicht vernachlässigt werden und beeinflusst die späteren Betriebskosten erheblich. Darüber hinaus ist auch der Genehmigungs- und Überwachungsaufwand bei der praktischen Umsetzung zu berücksichtigen.
4.3.4
Erstellung eines Betriebs-Layouts
In einem Betriebs-Layout werden alle für die zu planende oder zu dimensionierende Anlage wesentlichen Details in einem Lageplan skizziert. Das Layout sollte nach Möglichkeit maßstabsgetreu erstellt werden, sodass auch die wesentlichen Entfernungen und Größenverhältnisse sichtbar gemacht werden können. Das Layout wird in der Regel als Grundriss-Darstellung erstellt. Die wesentlichen Anlagenkomponenten (z. B. Abscheider, Ventilatoren) sollten aber auch als Aufriss oder Schnittzeichnung dargestellt werden. Das gilt besonders für die Fälle, bei denen aufgrund der betrieblichen Verhältnisse die Höhe begrenzt ist.
Im Betriebs-Layout sollten besonders folgende Randbedingungen dargestellt werden:
Standorte der abzusaugenden Emissionsstellen mit den zuzuordnenden Luftmengen
Standorte der Abscheider und Ventilatoren mit (kritischen) Abständen zu Gebäude-Außenhüllen, Nachbargrundstücken, Lagerbereichen mit brennbaren Materialien, etc.
Standorte und wesentliche Bauteile von vorhandenen oder noch zu errichtenden Entsorgungs- und (Zwischen-)Lagereinrichtungen
Verlauf von für den Betrieb der Anlage wesentlichen Versorgungseinrichtungen (Druckluftversorgung, Standorte von Schaltschränken, etc.)
Ein aussagefähiges Betriebs-Layout kann auch wesentliche Grundlage für die in Abschnitt 4.4 näher beschriebene Angebotsbearbeitung sein.
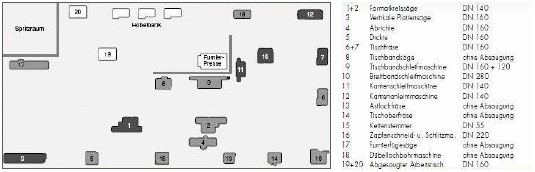
Abb. 4.3.4
Beispiel für Betriebslayout eines holzbearbeitenden Betriebs
4.3.5
Wahl der Anlagenbauart in einem iterativen Prozess
Für den Aufbau einer Absauganlage stehen verschiedene Varianten zur Verfügung (siehe Tabelle 4.1.1 in Abschnitt 4.1). Welche dieser Varianten unter den konkret herrschenden Randbedingungen optimale Ergebnisse liefert, kann nur ermittelt werden, indem eine konkrete Rechnung "durchgespielt" wird. Nach der Auswahl einer Variante des Luftführungsprinzips (siehe Abschnitt 4.3.5.1) werden dabei nacheinander folgende Schritte vorgenommen:
Trassierung und Dimensionierung der Rohrleitungen (Durchmesser, Längen)
Ermittlung der Druckverluste im System (Verbraucher, Rohrleitungen, Abscheider, Abluftkanäle)
Festlegung der Ventilator- und Antriebskonzepte (Anzahl und Anordnung im System, Dimensionierung, Übersetzungskonzepte, Steuerung/Regelung)
Festlegung erforderlicher Sicherheits- und Überwachungstechnik (Brand- und Explosionsschutz, Lärmschutz, Störungsüberwachung, Leistungsüberwachung)
Als Ergebnis der Berechnung ergeben sich Aussagen zum Betriebsverhalten (Arbeitspunkt: siehe Abbildung 4.3.5) sowie zu den jeweils erforderlichen Luftleistungen und den zu erwartenden Investitionskosten für die jeweils untersuchte Variante.
In einem iterativen Prozess wird anschließend die für die konkreten Randbedingungen günstigste Variante ermittelt.
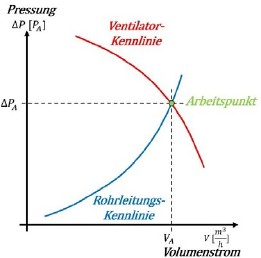
Abb. 4.3.5
Betriebsverhalten einer Absauganlage
4.3.5.1
Wahl des Luftführungs-Prinzips
Bei der Wahl des Luftführungsprinzips können schon einige weniger brauchbare Varianten von der Betrachtung und Berechnung ausgeschlossen werden, wenn man auf folgende Fragen unter den vorliegenden Randbedingungen eindeutige Antworten hat:
Können Verbrauchsstellen im Hinblick auf die jeweils erforderlichen Luftmengen, ihrer örtlichen Lage im Betrieb (siehe Betriebs-Layout) und den gleichzeitigen (oder nicht gleichzeitigen) Betrieb dieser Verbraucher sinnvoll zu Gruppen zusammengefasst werden?
Darf und soll die Abluft aus dem Abscheider als Rückluft in den Betrieb zurückgegeben werden oder soll sie als Fortluft in die Atmosphäre geblasen werden?
4.3.5.2
Trassierung und Dimensionierung der Rohrleitungen
Unter Trassierung versteht man die Wahl der Linienführung einzelner Rohrleitungsabschnitte oder der gesamten Rohrleitung. Um Druckverluste zu minimieren (siehe Abschnitt 4.3.5.3), sollten Rohrleitungen möglichst kurz sein und auf direktem Wege zum Kern der Anlage, nämlich dem Abscheider und den Ventilatoren führen. Scharfe Richtungsänderungen (Linienwinkel > 60°) sowie stumpfe Rohrzusammenführungen sollten vermieden werden. Bei den Zusammenfassungen einzelner Verbraucher im Rohrnetz können durch eine optimale Trassierung Verluste verringert werden, wenn Leitungsabschnitte mit höheren Gesamtdruckverlusten (Verbraucher + anschließende Rohrleitung) gegenüber solchen mit geringeren Verlusten kurzgehalten werden.
Das Durchstoßen von Brandwänden oder aus anderen Gründen "sensiblen" baulichen Anlagen im Rohrleitungsverlauf sollte nach Möglichkeit vermieden werden, um den notwendigen "Sicherungsaufwand" durch aufwändige Leitungskonstruktionen oder teure Sicherheitsbauteile (z. B. Brandschutzklappen) gering zu halten (siehe hierzu auch Abschnitt 3.9).
Rohrleitungen sollten so dimensioniert werden, dass ausreichende Volumenströme mit möglichst geringen Luftgeschwindigkeiten erreicht werden. Dabei muss darauf geachtet werden, dass die Material-Transportgeschwindigkeiten hinreichend groß sind, um einen ablagerungsfreien Transport zu gewährleisten. Diese kritische Geschwindigkeit ist stark vom Verhalten des abzusaugenden Stoff-Luft-Gemischs abhängig und für Feststoff-Luft-Gemische im Allgemeinen höher als für Flüssigkeitsnebel oder Gas-Luft-Gemische. Anhaltspunkte für kritische Geschwindigkeiten sind dem Abschnitt 3.3 oder den im Abschnitt 8. dargestellten stoff- und verfahrensspezifischen Kriterien zu entnehmen.
Der Querschnitt der abführenden Rohrleitungen hinter dem Zusammenfluss mehrerer Volumenströme (i) sollte so gewählt werden, dass die Luftgeschwindigkeit nach dem Zusammenfluss möglichst gleichbleibend ist. Das ist gegeben, wenn der Gesamt-Querschnitt (folgender Beziehung folgt:

4.3.5.3
Ermittlung aller Druckverluste im System
Bei jeder Strömung im geschlossenen System "Absauganlage" entstehen - neben den in Strömungsrichtung wirkenden dynamischen Drücken, die für die Herstellung des Volumenstroms erforderlich sind - statische Druckkomponenten, die senkrecht zur Strömungsrichtung wirken (siehe Abbildung 4.3.6). Diese Druckkomponenten behindern die Durchströmung, weil sie "Reibung" und damit Verluste erzeugen. Sie müssen vor Auswahl der Strömungsmaschine "Ventilator" zumindest nach ihrer Größenordnung bekannt sein, weil der Ventilator - neben der Druckkomponente in Strömungsrichtung - auch die zur Überwindung dieser Verluste notwendige Leistung liefern muss.
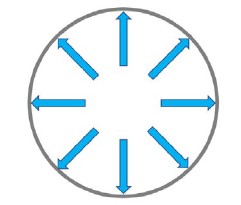
Abb. 4.3.6
Verlauf der senkrechten (statischen) Druckkomponente im Rohr
(Statische) Druckverluste ergeben sich in sämtlichen Bauteilen, die im Anlagenverlauf durchströmt werden. Im Besonderen sind das:
alle abzusaugenden Erfassungseinrichtungen und Verbrauchsstellen (Maschinen, Absaugwände, Absaugtische, Düsen, etc.),
alle Rohrleitungen und deren Leitungsbauteile (z. B. Krümmer, Abzweige, Aufweitungen, Verengungen, etc.),
alle Abscheider im Verlauf der Absauganlage,
alle Abluftkanäle, Ausblaseinrichtungen, Wärmetauscher, etc.
Steuerungs- und Sicherheitsbauteile, die innerhalb des durchströmten Bereiches verbaut sind (z. B. Klappen, Ventile, etc.)
Die Größe der statischen Druckverluste ergibt sich physikalisch nach der folgenden Beziehung:

mit
ζi = dimensionsloser, bauteilspezifischer Strömungswiderstandsbeiwert
pdyn = dynamischer Druck [Pa]
ϱ = Dichte von Luft i. A. 1,2 [kg/m3]
w = Luftgeschwindigkeit bei der Durchströmung [m/s]
Hinweise zu den zu erwartenden bauteilspezifischen Strömungswiderstandsbeiwerten sind den Abschnitten
Erfassungseinrichtungen (Abschnitt 3.2),
Rohrleitungen und ihre Leitungsbauteile (Abschnitt 3.3),
Abscheider (Abschnitt 3.5)
zu entnehmen. Bestehen Zweifel über den anzunehmenden Strömungswiderstandsbeiwert, helfen auch messtechnische Ermittlungen an identischen oder baugleichen Bauteilen in der Praxis weiter. Das gilt besonders für die Strömungswiderstandsbeiwerte von Erfassungseinrichtungen, die im Allgemeinen wesentliche Beiträge liefern und gleichzeitig eine hohe Streubreite haben. Bei den Vergleichswerten von Leitungsbauteilen liefern die veröffentlichten tabellarischen Werte ausreichende Genauigkeit.
Eine Besonderheit ergibt sich für die Druckverluste entlang (langgestreckter) Rohrleitungen. Hier kann der bauteilspezifische Strömungswiderstandsbeiwert nicht als konstant angenommen werden, da er von der Leitungslänge und dem Leitungsdurchmesser wie folgt abhängt:

mit:
λ = dimensionslose Rohrreibungszahl [-]
L = Länge des Rohrabschnitts [m]
D = Durchmesser der Leitung [m]
In Bezug auf die Druckverluste in Abscheidern gibt es eine weitere Besonderheit. Abscheider sind Anlagebestandteile, bei denen ein Bauteil mit einem relativ geringen Querschnitt (Absaugrohr) in ein Bauteil mit großem Querschnitt übergeht und bei denen die strömende Luft den großen Querschnitt wieder über einen kleineren Querschnitt (Rohr oder Abluftkanal) verlässt. Das führt zu veränderten Zusammensetzungen der Gesamtdrücke (siehe Abbildung 4.3.7).
Beispiel:
Beim Einströmen in den Abscheider wird die Luft durch die Verwirbelung und den Filterwiderstand von zum Beispiel 20 m/s (pdyn= 240 Pa) auf zum Beispiel 2 m/s (pdyn= 2,4 Pa) abgebremst. Dieser Verlust an dynamischem Druck (pdyn) bewirkt einen zusätzlichen Druckverlust, das heißt eine Zunahme des statischen Drucks (pstat,2). Beim Ausblasen aus dem Abscheider in einen kleineren Querschnitt wird der dynamische Druck (teilweise) zurückgewonnen.
Um diesen Verhältnissen Rechnung zu tragen, muss für die Filtereintragung (ζE) und die Filteraustragung (ζA) jeweils ein bauteilspezifischer Strömungswiderstandsbeiwert berücksichtigt werden. Auf der Einströmseite kann dieser Widerstandsbeiwert näherungsweise als
ζE = 1
angenommen werden. Der Widerstandswert auf der Ausgangsseite hängt von der Querschnittsgröße der abgehenden Leitung ab. Wenn dieser Querschnitt etwa doppelt so groß ist wie der Querschnitt der eingangsseitigen Rohrleitung, kann der Widerstandsbeiwert mit
ζA = 0,5
betrachtet werden.
Der wesentliche Druckverlust entsteht allerdings am Abscheidemedium aufgrund der unterschiedlichen Drücke auf der Roh- (pstat,2) und Reingasseite (pstat,3). Die Entwicklung und maximale Höhe dieses Druckverlusts

ist bei verschiedenen Abscheider-Typen unterschiedlich ausgeprägt und hängt im Regelfall stark mit der Beaufschlagung des Abscheiders (Luftmenge und Stoffkonzentration) sowie seiner Durchlässigkeit (Art und Zustand des Abscheidemediums) zusammen. Nähere Einzelheiten siehe Abschnitt 3.5.
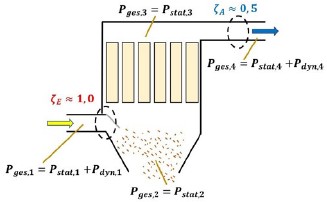
Abb. 4.3.7
Druckverhältnisse im Bereich eines Abscheiders
Abschließend werden die Druckverluste aller Bauteile innerhalb der Anlage aufsummiert. Ändern sich die Querschnitte (und damit die Luftgeschwindigkeit) im gesamten System nicht, können statt der Druckverluste auch die Strömungswiderstandsbeiwerte aufsummiert werden. Mithilfe dieses Gesamt-Widerstandsbeiwerts der Anlage kann anschließend der Gesamt-Druckverlust nach Gleichung 4.3 - 7 bestimmt werden.
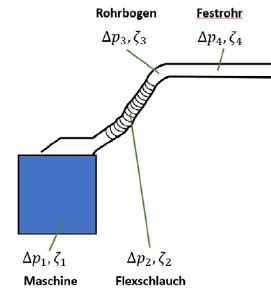
Abb. 4.3.8
Summierung der Widerstandsbeiwerte innerhalb eines Absaugbereichs.
Für den in Abbildung 4.3.8. dargestellten Anschluss einer Maschine an eine Haupt-Absaugleitung gilt:

Bei unverändertem Querschnitt im Leitungsverlauf:

Bei der oben betrachteten Reihenschaltung sind die Verhältnisse also relativ überschaubar.
Anders sieht es bei der Parallelschaltung mehrerer Erfassungsstellen aus, weil sich hier Verzweigungspunkte im System ergeben.
An Verzweigungspunkten ist zu beachten, dass dort nur ein Druck herrschen kann. Hier muss bei der Planung entschieden werden, welcher der aus den Anschlüssen resultierenden Drücke den "kritischen" Weg für die Anlage markiert. Das wird in der Regel der Anschluss sein, der - bei gegebenem Mindestvolumenstrom oder gegebener Mindestluftgeschwindigkeit - den höheren Druckverlust bewirkt. Dieser höhere notwendige Druck führt aber in den Verzweigungsleitungen mit ursprünglich niedrigerem Druck zu einer höheren Luftgeschwindigkeit und damit zu einem höheren Volumenstrom in diesen Leitungen.
Die daraus resultierende neue Luftgeschwindigkeit (wi) für den Leitungsabschnitt mit geringeren Druckverlusten ergibt sich auf der Basis des max. Druckverlusts am Knoten (Δpstat,max) nach der Beziehung:

Diese neue und in der Regel höhere Luftgeschwindigkeit führt nach der bekannten Beziehung (4.3 - 1) zu einem geändertem (höheren) Volumenstrom aus dem betreffenden Leitungsabschnitt und damit zu einem höheren Gesamt-Volumenstrom im Verzweigungspunkt. Dieser neue Volumenstrom ist dann bei der Berechnung der Druckverluste aller nachfolgenden Anlagenbereiche zu berücksichtigen.
In der der nachfolgenden Abbildung 4.3.9 ist der Druckverlauf an einer einfachen Absauganlage qualitativ dargestellt.
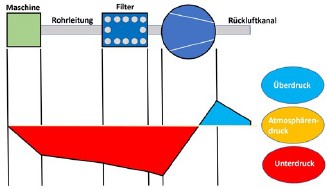
Abb. 4.3.9
Prinzip-Darstellung des Druckverlaufs an einer einfachen Absauganlage
4.3.5.4
Ventilator- und Antriebskonzept festlegen
Nachdem die konkreten Absauganforderungen in Form des benötigten Mindest-Volumenstroms und der erforderlichen Gesamt-Druckdifferenz ermittelt worden sind, müssen das passende Ventilator-Konzept und die für den konkreten Fall günstigste Antriebsvariante festgelegt werden. Wichtige Gesichtspunkte sind dabei:
Anordnung der Ventilatoren innerhalb des Systems (rohgas- oder reingasseitig)
Anzahl der Ventilatoren
Dimensionierung jedes einzelnen Ventilators für die konkreten Anforderungen (Kennlinien-Verhalten)
Wahl der Antriebstechnik (Direktantrieb, Antrieb über Kupplung, Riemenantrieb, Antrieb über Umrichter)
Maßnahmen zur Anpassung der Luftleistung auf den Bedarf im konkreten Betrieb (Regelung oder Steuerung des Leistungsverhaltens des/der Ventilator(s/en))
Im Regelfall sollten Ventilatoren reingasseitig angeordnet sein (siehe Abschnitt 4.1.2).
Eine Ausnahme von der Regel könnten Ventilatoren in Gruppenabsaugungen in Betrieben mit industrieller Fertigung unter folgenden Bedingungen darstellen:
Die Ventilatoren werden permanent während der Arbeitszeit betrieben,
sämtliche Gruppen sind (weitgehend immer) gleichzeitig im Einsatz,
der zu erwartende Verschleiß durch Abrieb ist gering oder nicht vorhanden,
der notwendige Unterdruck für die Absauggruppe ist sehr hoch,
die notwendigen Unterdrücke der Absauggruppen sind sehr unterschiedlich.
Bei rohgasseitiger Anordnung der Ventilatoren bestimmt sich deren Anzahl nach der Zahl der vorhandenen Gruppen, wenn innerhalb des Leitungssystems keine zusätzlichen "Stützventilatoren" zur Kompensierung besonderer, örtlich beschränkter Druckanforderungen vorgesehen werden müssen.
Reingasseitig kann die Zahl der Ventilatoren weitgehend frei gewählt werden, da der produzierte Volumenstrom sich in Abhängigkeit von den jeweiligen Druckanforderungen auf das Gesamtsystem verteilt. Mit mehreren Ventilatoren kann über deren Parallelschaltung (in Verbindung mit einer entsprechenden Ansteuerung) eine gute Anpassung an die betrieblichen Verhältnisse auch bei wechselnden Absauganforderungen realisiert werden. Voraussetzung ist, dass die Leistung der Ventilatoren in Bezug auf das über die Pressung realisierte Druckniveau (weitgehend) identisch ist, sodass sich die von den einzelnen Ventilatoren erzeugten Volumenströme im jeweiligen Betriebspunkt der Anlage addieren (siehe Abbildung 4.3.10).
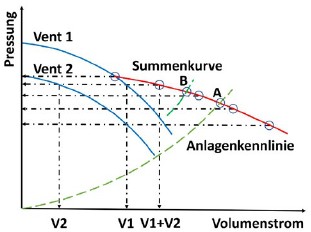
Abb. 4.3.10
Ventilator-Kennlinie bei Parallelschaltung zweier Ventilatoren
Bei der Dimensionierung des/r Ventilators/en muss darauf geachtet werden, dass sämtliche relevanten Betriebszustände in den möglichen Arbeitsbereich des Ventilators fallen, das heißt, dass die sich aus diesen Betriebszuständen ergebenden Anlagen-Kennlinien die Ventilator-Kennlinie innerhalb des für einen störungsfreien Betrieb zur Verfügung stehenden Kennlinien-Bereichs des Ventilators schneiden. Außerdem muss geprüft werden, ob der jeweilige Schnittpunkt (auch als Arbeitspunkt AP bezeichnet) mindestens den geforderten Volumenstrom liefert (siehe Abbildung 4.3.11).
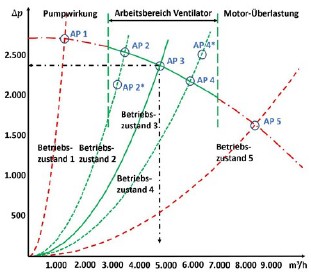
Abb. 4.3.11
Verhalten eines Ventilators bei unterschiedlichen Betriebszuständen
Die grafische Darstellung in Abbildung 4.3.11. ist folgendermaßen zu interpretieren:
- a.
Der Betriebspunkt AP 1 liegt links vom Arbeitsbereich des Ventilators: mögliche Pumpwirkung, d. h. instabiler Absaugbetrieb.
- b.
Der Betriebspunkt AP 5 liegt rechts vom Arbeitsbereich des Ventilators: Kommt dieser Betriebszustand häufiger oder über längere Zeit vor, könnte der Motor des Ventilators überlastet werden.
- c.
Der errechnete Betriebspunkt AP 2* liegt unterhalb der Ventilator-Kennlinie und damit links vom tatsächlichen Arbeitspunkt AP 2: Die tatsächliche Luftmenge und damit die Luftgeschwindigkeiten sind im konkreten Betrieb höher als erwartet.
- d.
Der errechnete Betriebspunkt AP 4* liegt oberhalb der Ventilator-Kennlinie und damit rechts vom tatsächlichen Arbeitspunkt AP 4: Die tatsächliche Luftmenge und damit die Luftgeschwindigkeiten sind im konkreten Betrieb niedriger als erwartet.
- e.
Der Arbeitspunkt AP 3 liegt dort, wo er nach Errechnen der Leitungs-Kennlinie erwartet wurde (Arbeitspunkt = Betriebspunkt). Die Luftmengen und damit die Luftgeschwindigkeiten sind so wie vorausberechnet. Dieser Arbeitspunkt liegt außerdem im optimalen Wirkungsgradbereich, d. h. in diesem Fall ist das Verhältnis zwischen Absaugleistung und Stromverbrauch am besten.
Das gewählte Antriebssystem hat wesentlichen Einfluss auf folgende Umstände:
- 1.
den Gesamt-Wirkungsgrad des Systems
- 2.
das Anlaufverhalten des Ventilators
- 3.
die Möglichkeiten der Einflussnahme auf das aktuelle Leistungsverhalten des Ventilators
Grundsätzlich liefert der Direktantrieb die geringsten Zusatzverluste aus dem Faktor "Antrieb", sodass der durch den Ventilator gegebene Wirkungsgrad entscheidend bleibt. Kupplungen und Riemenantrieb bedingen zusätzliche Wirkungsradverluste durch den Antrieb von 3 % bis ca. 10 %. Der Antrieb über einen Umrichter führt zu ca. 1 % bis 3 % Wirkungsradverlusten für das Gesamtsystem im laufenden Betrieb.
Im Gegensatz dazu ist das Anlaufverhalten des Ventilators bei Direktanlauf besonders ungünstig, da in diesem Fall der 5-fache Nennstrom wirkt. Bei Anlauf über Stern-Dreieck-Schaltung kann dieser Anlaufstrom auf den Faktor 3,5 reduziert werden. Beim Anlauf über einen Umrichter fällt kein zusätzlicher Anlauf-Faktor an, sodass der Motor hier nur mit dem 1-fachen Nennstrom belastet wird.
Einfluss auf das aktuelle Leistungsverhalten des Ventilators kann nur bei Vorschaltung eines Umrichters genommen werden, über den die Stromzufuhr für den Motor und damit sein Drehmoment beeinflusst werden kann. Damit wird es möglich, den Motor (und damit den Ventilator) in seinem Drehverhalten (und damit die abgegebene Luftleistung des Ventilators) über Regelungs-Mechanismen (i. d. R. durch Auswertung von Unterdruck-Messsignalen) oder programmierbare Steuerungen (i. d. R. über Auswertung von Absperrschieber-Stellungen) zu beeinflussen.
Aus den oben genannten Ausführungen lassen sich folgende Schlussfolgerungen ziehen:
Direktantrieb ist vorteilhaft, wenn
- 1.
die Nennleistung des Ventilators weniger als 15 KW beträgt und
- 2.
aus betrieblichen Gründen keine Beeinflussung der abgegebenen Ventilator-Leistung erfolgen muss und
- 3.
bei den herrschenden Betriebsverhältnissen nur wenige Ventilator-Anläufe je Arbeitsschicht zu erwarten sind.
Riemenantrieb ist vorteilhaft, wenn
- 1.
die Nennleistung des Ventilators mehr als 15 KW beträgt und
- 2.
die weiteren Randbedingungen, wie beim Direktantrieb erwähnt, gegeben sind.
In allen anderen Fällen ist der Antrieb über einen Umrichter vorzuziehen. Er ermöglicht stromsparendes Anlaufverhalten (wichtig vor allem in Handwerksbetrieben, in denen Verbraucher häufig eingeschaltet und nur kurzzeitig betrieben werden) und - als Schnittstelle zur Regelung/Steuerung - die Beeinflussung der aktuellen Luft-Leistung des Ventilators.
Nähere Einzelheiten zu Ventilatoren und Antriebskonzepten sind in Abschnitt 3.4, zu Steuerungen und Regelungen in Abschnitt 3.8 aufgeführt.
4.3.6
Gesamtkonzept überprüfen und justieren
Wenn die optimale Lösung in dem zuvor geschilderten iterativen Prozess herausgearbeitet worden ist, muss das erarbeitete Gesamtkonzept auf alle zugrundeliegenden bekannten oder zu vermutenden Betriebsbedingungen überprüft und an den erkannten Schwachstellen nachjustiert werden. Das betrifft das Verhalten in allen für den späteren Anlagenbetrieb wichtigen Betriebszuständen, die Ermittlung eventuell noch vorhandener Reserven bei der Luftleistung und die Flexibilität des Systems für mögliche spätere Anlagenerweiterungen.
Abschließend sind noch die (Investitions-)Kosten und die zukünftig zu erwartenden Aufwendungen für den Betrieb der Anlage zu ermitteln, vornehmlich also die Kosten für elektrische (und auch pneumatische) Energie.
4.3.6.1
Verhalten in wichtigen Betriebszuständen
Das wesentliche Problem bei der Bestimmung der Anlagengröße ist der anzunehmende gleichzeitige Betrieb der angeschlossenen Absaugstellen. Besonders bei vorwiegend handwerklicher (Einzelstück-)Fertigung kann das von der Anlage abzudeckende Volumenstrom-Spektrum sehr differieren und recht umfangreich werden. Es ist daher zwingend erforderlich, die Leistungsfähigkeit des vorzuschlagenden Absaugkonzepts in allen wesentlichen Betriebszuständen zu überprüfen. Die für diese Überprüfung wichtigsten Zustände ist die
maximal
minimal
durchschnittlich im Betrieb (am häufigsten)
erforderliche Luftmenge, die die Anlage zu erbringen hat.
Der maximale Volumenstrombedarf wird im Regelfall der Betriebszustand sein, der der Dimensionierung zugrunde liegt. Zu beachten ist dabei, dass Zuschläge für den sogenannten hydraulischen Abgleich (siehe rechte Spalte), für eventuell einzuplanende Reserven und für "Falschlufteinträge" aus (montagebedingten) Anlagen-Undichtigkeiten berücksichtigt werden. Letztere müssen besonders dann berücksichtigt werden, wenn das erforderliche Druckniveau in der Anlage hoch ist.
Der minimale Luftbedarf erweist sich in der Praxis häufig als kritisch, wenn aufgrund größerer Leitungsdurchmesser in Sammelleitungen dort die für den ablagerungsfreien Transport erforderlichen Mindestluftgeschwindigkeiten nicht mehr erreicht werden. Dieses Problem kann häufig nur über eine (gezielte) Korrektur der betroffenen Durchmesser oder durch gezielte Aktivierung von Beiluft-Volumenströmen durch steuerungstechnische Maßnahmen (z. B. durch steuerungstechnisch veranlasstes Öffnen von Absperrschiebern an aktuell eigentlich nicht betriebenen Absaugstellen) behoben werden.
Der durchschnittliche Volumenstrombedarf, das heißt, der nach zeitlicher Gewichtung häufigste Betriebsfall, determiniert wesentlich den über längere Zeiträume zu erwartenden Energiebedarf der Anlage sowie die zu erwartende Immissionssituation für die Beschäftigten vor Ort. Deshalb sollte die Anlage für diesen Betriebszustand in Bezug auf ihren Gesamt-Wirkungsgrad optimiert sein.
Hydraulischer Abgleich: Werden mehrere Absaugstellen von einem gemeinsamen Ventilator abgesaugt, stellen sich an den einzelnen Erfassungselementen oder Rohrstutzen unterschiedliche Luftgeschwindigkeiten ein. Die Verteilung der Luftgeschwindigkeiten hängt von den Rohrleitungs-Geometrien und den Strömungswiderständen auf dem Weg zu den einzelnen Erfassungsstellen ab. Durch geschickte Gestaltung der Rohrleitungs-Geometrien an den Anschlussleitungen zu den Erfassungsstellen lässt sich ein einheitliches Widerstands-Niveau in der gesamten Anlage erzeugen und so ein eng an die jeweiligen Mindestanforderungen angepasstes Volumenstrom-Niveau.
Darüber hinaus lässt sich die Verteilung der Luftgeschwindigkeiten nur beeinflussen, wenn man entweder Drosseln als künstliche Zusatzwiderstände (Energievernichtung) oder Stützventilatoren einbaut, die bei Erfassungsstellen mit viel höheren Druckverlusten den Unterschied zwischen erforderlichem Gesamtdruck und Druckniveau der reingasseitigen Absaugventilatoren ausgleichen.
Der Einsatz von Drosseln ist, auch wegen der Probleme beim Materialtransport, häufig nicht ratsam. Wenn man sie trotzdem einsetzen möchte, ist besonders bei partikelförmigen Stoffen darauf zu achten, dass die Übergänge vom und zum Ausgangsdurchmesser innerhalb der Drossel sanft gestaltet werden, damit sich kein Material hinter Blenden oder festgestellten Klappen verfängt und die Rohrleitung verstopft. Auch sollte der verbleibende Rohrquerschnitt ausreichend groß sein, damit sich große Materialstücke oder Fasern nicht verfangen.
Stützventilatoren sind wegen ihres zusätzlichen Energiebedarfs und der mit ihrem Betrieb verbundenen Lärmentwicklung unbeliebt.
Würde der hydraulische Abgleich vollständig gelingen, wäre der vom Ventilator zu fördernde Volumenstrom gleich der Summe der Mindestvolumenströme der angeschlossenen Absaugstellen. In der betrieblichen Praxis ist das aber nur äußerst selten der Fall.
Je schlechter der hydraulische Abgleich gelingt, desto größer ist der notwendige Zuschlag Z(h) als Faktor mit

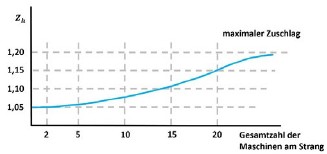
Abb. 4.3.12
Zuschlagsfaktor für hydraulischen Abgleich in Abhängigkeit von den angeschlossenen Maschinen
Abbildung 4.3.12 stammt aus einer Untersuchung von Absauganlagen für Holzstaub und -späne, bei der zur vergleichenden Bewertung unterschiedlicher Anlagenkonzeptionen der hydraulische Abgleich über eine Volumenstrombilanz an mehreren Anlagen bestimmt wurde. Sie zeigt, dass die Größe dieses Zuschlags von der Größe des zu untersuchenden Strangs - also der Anzahl der angeschlossenen Maschinen - abhängt. Die Anzahl der gleichzeitig betriebenen Maschinen ist oft deutlich geringer.
Der notwendige Zuschlagsfaktor beträgt:
für kleine Stränge (2 bis 5 angeschlossene Maschinen) in der Regel Z(h) = 1,05 und im Einzelfall bis Z(h) = 1,20
für größere Stränge bis zu Z(h) = 1,20 im Normalfall, bei schlechtem Abgleich kann er bis zu Z(h) = 1,50 anwachsen.
Daraus lässt sich schließen, dass der hydraulische Abgleich bei Zentralabsaugungen (auch mit reingasseitiger Anordnung des Ventilators) im Allgemeinen in der Praxis schlechter gelingt als bei anderen Konstellationen.
Für Planungsaufgaben muss der Zuschlag entweder wie oben beschrieben per Faktor erfolgen oder durch konkrete Ermittlung der Anlagen-Kennlinien für die relevanten Betriebszustände verifiziert werden.
4.3.6.2
Ermittlung von vorhandenen Leistungs-Reserven und System-Flexibilität
Viele Betreiber möchten möglichst hohe Leistungsreserven (= Volumenstromreserven) in eine neue Absauganlage packen, weil sie über die zukünftige Entwicklung in ihrem Betrieb unsicher sind und teure Nachrüstungen an der Absauganlage umgehen wollen. Häufig planen sie auch den Neukauf oder Austausch von Maschinen oder anderen Arbeitsmitteln mit Absaugstellen, ohne konkretere Vorstellungen über die benötigte Absaugleistung zu haben.
Der Betreiber möchte, dass bei der Anlagenplanung entsprechende Zuschläge berücksichtigt werden. Das ist aber nur in begrenztem Umfang vernünftig.
Kritisch ist der nachträgliche Anschluss von Absaugstellen immer dann, wenn
entweder durch diesen Anschluss der gleichzeitig erforderliche Volumenstrombedarf erhöht würde
oder das Pressungsniveau des Ventilators für die Absaugung der nachträglich anzuschließenden Absaugstellen unzureichend ist.
Die Berücksichtigung großer oder unbestimmter Reserven bei der Dimensionierung der Hauptleitungen und Ventilatoren ist in jedem Fall fragwürdig, da bis zur Realisierung der infrage stehenden Anschlüsse von zusätzlichen Absaugstellen erhebliche strömungstechnische und energetische Nachteile in Kauf zu nehmen wären. Solche Nachteile ergeben sich, weil
erhebliche Beiluft-Mengen für den reibungslosen Transport in den überdimensionierten Leitungen anfallen würden,
der überdimensionierte Ventilator überwiegend in Bereichen schlechter Wirkungsgrade arbeiten würde und damit eine überhöhte Stromaufnahme hätte.
Bei als "Gruppenabsaugungen" konzipierten Systemen stellt sich zudem die Frage, welche der vorhandenen Gruppen auf die zusätzlichen Luftmengen auszulegen wäre. In der Regel ist selbst über den zukünftigen Standort dieser zusätzlichen Verbraucher in der Werkstatt noch nichts bekannt.
Unschädlich ist die Berücksichtigung von Reserven nur im Bereich der Abscheider. Da diese in der Regel auch das teuerste Einzelbauteil der Anlage darstellen, ist eine auf gewisse Volumenstromreserven vorgenommene Auslegung des Abscheiders auch im Hinblick auf die Abscheidegeschwindigkeit und die (eventuell) notwendigen Regenerations-Intervalle am sinnvollsten.
Eine höhere Flexibilität ergibt sich bei Systemen, die nach dem Baukastenprinzip erweitert werden können (z. B. durch Drehzahlregelung oder Parallelschaltung von Ventilatoren) und bei denen das Transportproblem in Sammelleitungen durch alternative technische Lösungen gemindert werden kann. Aber selbst in diesen Fällen müssen die Druckverluste immer noch kompensiert werden können, das heißt, das Pressungsniveau der vorhandenen Ventilatoren muss auch für die neuen Anforderungen ausreichend sein.
4.3.6.3
Bewertung von Kosten- und Energieeffizienz
Neben den Investitionskosten für den Erwerb und die Errichtung der Absauganlage spielen die Kosten für den Betrieb der Anlage eine Rolle.
Da die Wartungskosten im Allgemeinen relativ gering sind, sind vor allem die Kosten für den Energieverbrauch, speziell die Kosten für die elektrische Antriebsenergie relevant.
Der Energieverbrauch von Absauganlagen ist erheblich und macht zum Beispiel im handwerklichen Schreinerei-Betrieb ca. 30 %, in Extremfällen bis zu 50 % des Gesamtbedarfs an elektrischer Energie aus.
Da die Anforderungen an die Leistungsfähigkeit von Absauganlagen, bedingt durch höhere gesetzliche Anforderungen, aber auch größeres Qualitäts- und Kosten-Bewusstsein auf der Betreiberseite ständig gewachsen sind und zugleich in näherer Zukunft mit steigenden Energiekosten gerechnet werden muss, wird die Bedeutung des Energiebedarfs einer Anlage wachsen.
Die wesentlichen Faktoren zur Bestimmung des Energiebedarfs und dessen Kosten sind:
die Anforderungen an die Absauganlage,
die Randbedingungen beim Betrieb der Anlage,
die strömungstechnische Konstruktion und Auslegung der Absauganlage.
Der Energiebedarf einer Anlage bestimmt sich aus zwei wesentlichen Leistungskomponenten:
- 1.
der Luftleistung, die sich als "Output" des Ventilators ergibt und
- 2.
der Netzleistung, quasi dem "Input" des den Ventilator antreibenden Elektromotors (bzw. Umrichters).
Beide Leistungen sind durch die diversen Verluste direkt miteinander verbunden. Sie sind außerdem vom tatsächlichen Betrieb der Anlage, das heißt, der Zusammensetzung und der Häufigkeit einzelner Betriebszustände, abhängig. Zu diesen rein auf die eigentliche Absaugung konzentrierten Komponenten sind im Allgemeinen auch noch der Strombedarf von diversen "Hilfseinrichtungen", zum Beispiel Schnecken und Zellenradschleusen für die Austragung, Überwachungs- und Sicherheitseinrichtungen sowie von Kompressoren, zur Erzeugung benötigter "Fremdenergien" wie Druckluft zu berücksichtigen.
Die Luftleistung ergibt sich physikalisch nach der Beziehung:

PLuft = Luftleistung [Watt]
V̇ = Volumenstrom [m3/s]
Δpges = Totaldruckerhöhung [Pa]
Die Netzleistung ergibt sich aus dem aufgenommenen Motorstrom nach der Beziehung:

PNetz = Netzleistung [Watt]
cosφ = Phasenverschiebungswinkel
U = Netzspannung [V]
I = Stromstärke [A]
Der Vereinfachungsfaktor √3 · cosφ · U = 0,58 gilt für eine Netzspannung von 400 Volt.
Die von beiden Leistungen "eingerahmten" Verluste determinieren den Gesamt-Wirkungsgrad.

Schon bei der Anlagen-Konstruktion können sich durch konsequentes Anwenden physikalischer Zusammenhänge (z. B. Trassierung und Dimensionierung des Leitungsnetzes) und Beschränkung der Volumenströme erhebliche Leistungseinsparungen und damit Reduktionen beim Energiebedarf ergeben.
Weitere Einsparungen können sich aus der Wahl des richtigen Ventilator-Konzepts ergeben. Grundlegende Frage ist dabei, ob der Ventilator auf der Rohluft- oder der Reinluftseite der Anlage angeordnet werden soll.
Verluste, die die erforderliche Ventilator-Leistung und damit deren elektrische Leistungsaufnahme beeinflussen, sind gegeben durch:
Ventilator-Wirkungsgrad (Anordnung und Form des Laufrads)
Antrieb zwischen Ventilator und Motor (Direktantrieb, Riemenantrieb)
Motorwirkungsgrad
Antrieb des Motors (z. B. Umrichter)
Der Gesamt-Wirkungsgrad beträgt:

Darüber hinaus spielt für die Gesamtleistungsaufnahme auch das Anlaufverhalten des Ventilators eine wesentliche Rolle, vor allem beim Anlagenbetrieb mit häufigen Einschalt-/Ausschaltvorgängen.
Als Fazit kann gezogen werden: Wesentliche Energieeinsparungen sind durch die richtige Anlagenkonzeption (Konstruktion) zu erzielen. Der Einfluss des Ventilator-Konzepts auf den Energieverbrauch hängt vom Betrieb der Anlage (abzudeckendes Luftmengenspektrum, Häufigkeit und Variationsbreite der einzelnen Betriebszustände) in der Praxis ab. Häufig hat ein Konzept mit reinluftseitiger Ventilator-Anordnung und Drehzahlregelung energetische Vorteile, das ist aber nicht grundsätzlich so! Es ist daher immer eine Untersuchung im Einzelfall erforderlich.
4.3.7
Dokumentation der Betriebszustände
Nachdem die auf iterativem Wege (möglichst) optimale Lösung gefunden wurde, müssen die Ergebnisse dieser Lösung für jeden der zugrunde gelegten Betriebszustände nachvollziehbar dokumentiert werden. Die bestmögliche Umsetzung ist eine Tabelle, es sind aber auch andere Formen möglich. In jedem Fall muss die Dokumentation folgende Informationen enthalten:
Einhaltung der Anforderungen an den Absaugstellen:
Eine Liste (Gleichzeitigkeitstabelle) aller Absaugstellen, die im jeweiligen Betriebszustand erfasst werden, mit Angaben zu
den Durchmessern der Erfassungselemente in mm,
der Luftgeschwindigkeit in m/s,
dem Volumenstrom in m3/h,
dem zur Erzielung dieses Volumenstroms zugrunde gelegten Unterdruck in Pa,
der Kennzeichnung von Absaugstellen, deren Absaugung im aktuellen Betriebszustand nicht gefordert wird, die aber aus Gründen des hydraulischen Abgleichs oder zur Aufrechterhaltung der Mindestluftgeschwindigkeiten in Sammelleitungen Volumenströme zuführen.
Einhaltung der Anforderungen innerhalb des Leitungsnetzes und der Abscheider
Angaben zu den vorhandenen Luftgeschwindigkeiten in den betroffenen Sammelleitungen,
Angaben zur Belastung des Abscheiders (Filtrationsgeschwindigkeit, Filterflächenbelastung, zu erwartende Druckverluste, etc.),
Angaben zu den vorhandenen Luftgeschwindigkeiten in den Abluftleitungen und zu den Ausblasgeschwindigkeiten.
Erzeugung der Luftströmung:
Angaben zum Verhalten des/r Ventilators/en,
Darstellung des aktuellen Arbeitspunkts auf der Ventilator-Kennlinie oder im Kennlinien-Feld (im Fall drehzahlgeregelter Ventilatoren),
Angabe der aktuellen Ventilator-Drehzahl, der aktuellen Leistungsaufnahme und des aktuellen Ventilator- und Gesamt-Wirkungsgrads (inkl. Antriebs- und Motorverlusten),
Angaben zum/zur aktuellen Energieverbrauch/Stromaufnahme,
Angaben zu im aktuellen Betriebszustand noch vorhandenen Leistungsreserven gegenüber den Mindestanforderungen,
Angaben zu Maßnahmen des hydraulischen Abgleichs (Einsatz von Drosseln, Beiluftklappen, Stützventilatoren, programmgesteuertes Öffnen von Schiebern aktuell nicht zu bedienender Absaugstellen).