Abschnitt 3.5 - 3.5 Abscheider
Abscheider haben die Aufgabe, luftfremde Stoffe vom "Transportmedium Luft" zu trennen. Zu diesen luftfremden Stoffen gehören gasförmige, flüssige und feste Stoffe.
Die Art und Eigenschaft der luftfremden Stoffe entscheidet darüber, welche Arten von Abscheidern grundsätzlich geeignet sind und wie hoch der Abscheidegrad sein muss, um die gereinigte Luft an die Umwelt abgeben oder in den Arbeitsraum zurückführen zu dürfen.
3.5.1 Wirkprinzip von Abscheidern
Vor dem Abscheider spricht man immer von "Rohgas" oder "Rohluft" und hinter dem Abscheider von "Reingas" oder "Reinluft" (siehe Abbildung 3.5.1).
Zur Beurteilung von Abscheidern wurde der Gesamtabscheidegrad Tges (dimensionslos) als Verhältnis der abgeschiedenen Menge der luftfremden Stoffe zur zugeführten Menge der luftfremden Stoffe definiert:

Sofern die Roh- und Reinluft-Staubgehalte CA und CF bekannt sind, kann der Gesamtabscheidegrad auch daraus berechnet werden:

Eine detailliertere Aussage über die Leistungsstärke eines Abscheiders ermöglicht der Fraktionsabscheidegrad T(xP). Hier wird die abgeschiedene Menge einer bestimmten Teilchenfraktion ΔṁG auf die Menge derselben Fraktion im Aufgabegut ΔṁA bezogen:

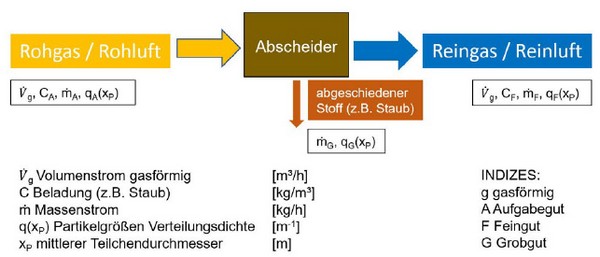
Abb. 3.5.1
Bezeichnung der Massenströme eines Abscheiders (Größen am Beispiel Staubabscheider)
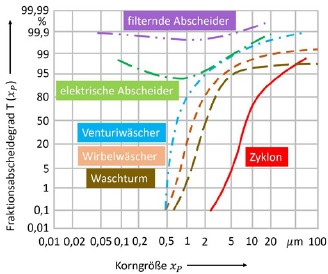
Abb. 3.5.2
Fraktionsabscheidegradkurven verschiedener Staubabscheidesysteme [30]
Der Fraktionsabscheidegrad ermöglicht auch einen direkten Vergleich verschiedener Abscheider-Systeme, die in den folgenden Unterabschnitten weiter erläutert werden (siehe Abb. 3.5.2):
Anstelle des Gesamtabscheidegrads wird gelegentlich auch der Durchlassgrad angegeben. Er gibt an, was durch den Abscheider nicht abgeschieden, sondern durchgelassen wird:

3.5.2 Abscheidung partikelförmiger Stoffe
Zu den partikelförmigen Stoffen zählen nicht nur feste partikelförmige Stoffe, sondern auch flüssige Stoffe in Form von feinen, im Luftstrom getragenen Tropfen. Man spricht von Aerosolen bei einem heterogenen Gemisch aus Luft und feinen Partikeln oder flüssigen Tröpfchen (siehe Abbildung 3.5.3).
Bei partikelförmigen Stoffen richtet sich die Abscheidetechnik im Wesentlichen nach der Partikelgröße und dem Zustand (fest oder flüssig), in dem die Partikel vorliegen.
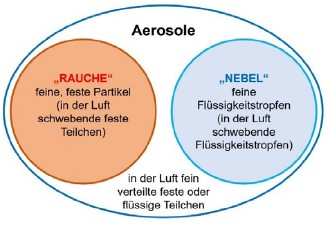
Abb. 3.5.3
Veranschaulichung des Begriffs "Aerosol"
3.5.2.1
Massenkraftabscheider
Massenkraftabscheider nutzen zur Abscheidung von partikelförmigen Stoffen vom Gasstrom/Luftstrom massenproportionale Feldkräfte, wie die Schwerkraft (Gravitation), die (Massen-) Trägheitskraft, die Magnetkraft und Zentrifugalkräfte. Hierzu zählen zum Beispiel:
Schwerkraftabscheider (z. B. Absetzkammern)
Prallabscheider
Magnetabscheider
Zyklone (Zentrifugalabscheider/Fliehkraftabscheider)
Sie dienen häufig nur als Vorabscheider in mehrstufigen Abscheidekonzepten. Die Arten und Einsatzbereiche der verschiedenen Massenkraftabscheider werden in der VDI-Richtlinie 3676 [41] beschrieben.
3.5.2.2
Elektrostatische Abscheider/Elektrofilter
Feste oder flüssige Partikel können aus einem Luftstrom in elektrischen Abscheidern durch die Einwirkung eines elektrischen Felds abgeschieden werden. Hierzu werden die Anziehungskräfte zwischen elektrisch geladenen Partikeln und einer gegenpolig geladenen Abscheidefläche genutzt. Je nach Anwendung können elektrische Abscheider Abscheidegrade von über 99 % erzielen. Der Energiebedarf zum Betreiben elektrischer Abscheider ist relativ zu anderen Abscheidern gering. Sie sind besonders zur Reinigung großer Gasmengen mit hohen Temperaturen geeignet. Der Abscheidevorgang erfolgt in 4 Schritten [30]:
- 1.
Aufladung der Partikel im elektrischen Feld
- 2.
Transport der aufgeladenen Partikel zur Niederschlagselektrode
- 3.
Anhaftung und Schichtbildung an der Niederschlagselektrode
- 4.
Entfernung der Staubschicht von der Niederschlagselektrode
Bei trocken arbeitenden Elektrofiltern bildet sich an der Niederschlagselektrode durch die anhaftenden Staubpartikel eine lockere Staubschicht mit einer Porosität von bis zu 90 % und Schichtdicken zwischen 1 und 10 mm. Durch das Auftreffen weiterer geladener Partikel muss die Ladung durch die Staubschicht zur Elektrode hindurchfließen. Deshalb ist der elektrische Widerstand der Staubschicht entscheidend und die Wirksamkeit hängt maßgeblich von einer regelmäßigen Reinigung ab. Aus diesem Grund gibt es auch Nass-Elektrofilter, bei denen die Reinigung durch einen Wasser-Rieselfilm regelmäßig erfolgt. Bei der Abscheidung flüssiger Tröpfchen aus Aerosolen spricht man auch vom Selbstreinigungsprinzip.
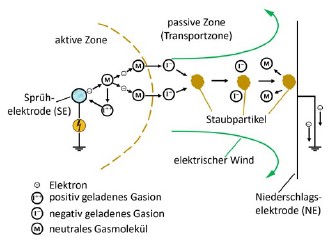
Abb. 3.5.4
Wirkungsprinzip elektrostatischer Abscheider [30]
3.5.2.3
Nassabscheider
Das Wirkungsprinzip von Nassabscheidern besteht darin, die im Rohgasstrom dispergierten Partikel mit einer Waschflüssigkeit in Kontakt zu bringen, um sie darin zu binden und dann das entstehende Partikel-Flüssigkeits-Gemisch vom Luftstrom zu trennen. Besonders geeignet sind Nassabscheider bei klebrigen oder leicht entzündlichen Stäuben und Aerosolen; zusätzlich können mit Nassabscheidern prinzipiell auch gasförmige Gefahrstoffe abgeschieden oder der Luftstrom kann zusätzlich gekühlt werden.
Um eine Nassabscheidung effektiv zu gestalten, ist es notwendig, zwischen der Waschflüssigkeit und dem zu reinigenden Gas eine möglichst große Phasengrenzfläche als Kontaktfläche zu schaffen. Hierzu sind technisch folgende Anordnungen möglich (siehe Abbildung 3.5.5):
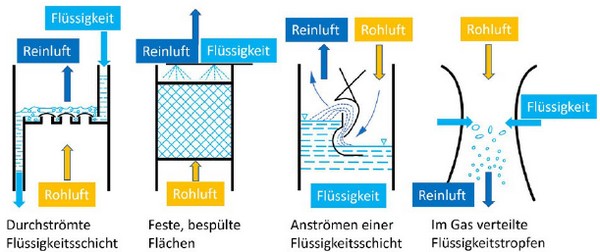
Abb. 3.5.5
4 verschiedene Grundprinzipien von Nassabscheidern zur Erzeugung einer möglichst großen Kontaktoberfläche zwischen Waschflüssigkeit und Partikeln im Rohgas [30]
Abscheidung in durchströmten Flüssigkeitsschichten: In der Flüssigkeitsschicht werden feinste Gasbläschen/Luftbläschen erzeugt. Technisch erfolgt das zum Beispiel durch Sieb- oder Glockenböden. Der Staub lagert sich an der Bläschengrenzfläche ab.
Abscheidung an festen, bespülten Flächen: Der Abscheider ist mit sogenannten Füllkörpern gefüllt, die insgesamt eine große Kontaktoberfläche schaffen, wenn sie von oben mit einem Waschflüssigkeitsnebel berieselt werden und von unten das zu reinigende Gas einströmt (z. B. Spritzwand mit Wasserschleier beim Spritzlackieren).
Abscheidung durch Anströmung einer Flüssigkeitsschicht: Hierbei muss im Abscheider eine feste, gasdichte Abtrennung zwischen Rohgas auf der einen Seite und Reingas auf der anderen Seite oberhalb des Waschflüssigkeitsspiegels vorhanden sein. Dann kann das Rohgas mit Überdruck durch die Waschflüssigkeit hindurchgedrückt werden. Die Strömungsumlenkung und das Mitreißen von Flüssigkeits-Tröpfchen bewirkt die Kontaktfläche und die Abtrennung der im Rohgas enthaltenen Partikel.
Abscheidung an im Gas/in der Luft enthaltenen Flüssigkeits-Tröpfchen: Im Abscheider werden durch Versprühen der Waschflüssigkeit mit Sprühdüsen oder durch rotierende Elemente feinste Flüssigkeits-Tröpfchen mit einer großen Phasenoberfläche als Kontaktfläche erzeugt. Die im Rohgas enthaltenen Partikel haften an der Tröpfchen-Oberfläche an.
Aus diesen Wirkprinzipien entstanden die folgenden Grundbauformen von Nassabscheidern:
Waschtürme, Füllkörperkolonnen: Sie werden meist eingesetzt, wenn neben der Staubabscheidung auch gleichzeitig eine Gaskühlung beabsichtigt ist. Die einfachsten Waschtürme sind große einbaulose Behälter, die mit dem zu reinigenden Gas mit ca. 1 m/s durchströmt werden; dabei wird in mehreren Ebenen Waschflüssigkeit eingespritzt. Die Abscheideleistung dieser Bauform ist sehr gering; aber auch der Druckverlust ist mit ca. 150 Pa sehr gering. Andere Bauformen von Waschtürmen haben Einbauten in Form von berieselten Füllkörpern oder Umlenkblechen. Dadurch wird zwar die Abscheideleistung erhöht, aber auch der Druckverlust kann auf bis zu 2.500 Pa ansteigen.
Strahlwäscher: Strahlwäscher werden überwiegend dann eingesetzt, wenn neben den Partikeln im Gasstrom auch Gase ausgewaschen werden sollen oder wenn die Gasmengen stark schwanken. Die Waschflüssigkeit wird axial durch eine Düse im Gleichstrom mit dem zu reinigenden Gas aufgegeben. Dadurch wird das zu reinigende Gas wie bei einer Wasserstrahlpumpe angesaugt und gereinigt. Die Gasgeschwindigkeit steigt auf bis zu 20 m/s und die Waschflüssigkeit tritt mit einer Geschwindigkeit von bis zu 35 m/s aus der Düse aus. Die spezifische Waschflüssigkeitsmenge liegt bei bis zu 20 l/m3 pro Stufe; allerdings kann die Waschflüssigkeit im Kreislauf gefahren werden. Die Abscheideleistung liegt bei Strahlwäschern etwas höher als bei Waschtürmen. Strahlwäscher erzeugen keinen zusätzlichen Druckverlust. Der Energieeintrag erfolgt über die Waschflüssigkeit.
Wirbelwäscher: Wirbelwäscher sind besonders zur Abscheidung besonders grober Stäube geeignet, wie sie zum Beispiel bei der Oberflächenbehandlung durch mechanische Verfahren (z. B. Schleifen von Metallen) entstehen. Der zu reinigende Gasstrom prallt im Wirbelwäscher auf eine Wasseroberfläche; dadurch erfolgt eine Vorabscheidung. Die Strömung wird dann durch einen gekrümmten Kanal umgelenkt und bewirkt so die Verwirbelung der mitgerissenen Flüssigkeits-Tröpfchen. Durch einen gekrümmten Kanal wird die Strömung umgelenkt, wodurch eine Verwirbelung der mitgerissenen Flüssigkeits-Tröpfchen erfolgt. Dadurch werden auch feinere Partikel abgeschieden. Die Gasgeschwindigkeit in der Wirbelzone beträgt bis zu 15 m/s und der Druckverlust bis zu 3.000 Pa. Dafür ist die Bauweise von Wirbelwäschern vergleichsweise einfach, damit preiswert und wartungsarm.
Rotationswäscher: Bei korrekter Auslegung sind Rotationswäscher leistungsstark. Es handelt sich um zylindrische Behälter, in die das zu reinigende Gas tangential von unten einströmt und dann ein bis zwei Waschstufen durchströmt. Dort befinden sich schnelllaufende Zerstäuber-Scheiben (Umfangsgeschwindigkeit bis zu 70 m/s), die einen dichten Tropfenschleier erzeugen, wodurch Partikel bei Kontakt ausgewaschen werden. Rotationswäscher erreichen gute Abscheidegrade und können Stäube bis unter 0,5 µm vollständig abscheiden. Nachteilig bei Rotationswäschern sind ein relativ hoher Energieverbrauch und eine hohe Wartungsintensität wegen hohem Verschleiß durch die schnell umlaufenden Teile.
Venturiwäscher: Sie erreichen von allen Nasswäschern die höchsten Abscheidegrade und eignen sich besonders zur Abscheidung von Kondensations- und Sublimationsstäuben aus Gasen. Sie zeichnen sich durch eine einfache Konstruktion und einen geringen Platzbedarf aus. Nachteilig ist der hohe Druckverlust von bis zu 20.000 Pa. Das zu reinigende Gas wird durch ein Venturirohr gedrückt und erreicht an der engsten Stelle, der sogenannten Kehle, Geschwindigkeiten von bis zu 150 m/s. Genau dort wird die Waschflüssigkeit axial eingedüst, wodurch feinste Tröpfchen zur Gasreinigung entstehen und die Partikel an sich binden.
Wenn die Partikel sich weitgehend an die Waschflüssigkeits-Tröpfchen angelagert oder in sie eingelagert haben, müssen die beladenen Tröpfchen wieder vom Gasstrom getrennt werden. Das erfolgt meist wieder über Massenkraftabscheider. Tabelle 3.5.1 zeigt die wichtigsten Vor- und Nachteile von Nassabscheidern.
Nassabscheider werden aufgrund dieser Einschätzung besonders bei nassen, klebrigen, brennbaren und explosionsfähigen Stäuben eingesetzt, aber auch in der chemischen Industrie, in der Abgasreinigung konventioneller Kraftwerke und in der thermischen Abfallverwertung (z. B. Müllverbrennungsanlagen). Tabelle 3.5.2 weist charakteristische Daten von Nasswäschern auf.
Tabelle 3.5.1
Vor- und Nachteile von Nassabscheidern
Vorteile Nassabscheider | Nachteile Nassabscheider |
---|---|
|
|
Tabelle 3.5.2
Charakteristische Daten von Nasswäschern, xP = Grenzkorndurchmesser, bis zu dem gerade 50 % abgeschieden werden, vrel = Relativgeschwindigkeit, Δp = Druckverlust, b = spezifische Waschflüssigkeitsmenge in Bezug auf Gasvolumen, ES = spezifischer Energieaufwand in Bezug auf Gasvolumen nach [30]
Parameter | Wasch-Turm | Strahlwäscher (2-stufig) | Wirbelwäscher | Rotationswäscher (2-stufig) | Venturiwäscher |
---|---|---|---|---|---|
xP [µm] | 0,7 - 1,5 | 0,8 - 0,9 | 0,6 - 0,9 | 0,1 - 0,5 | 0,05 - 0,2 |
vrel [m/s] | 1 | 10 - 25 | 8 - 20 | 25 - 70 | 40 - 150 |
Δp [Pa] | 200 - 2.500 | 0 | 1.500 - 2.800 | 400 - 1.000 | 3.000 - 20.000 |
b [l/m3] | 0,05 - 5 | 5 - 20 (pro Stufe) | auslegungsspezifisch | 1 - 3 (pro Stufe) | 0,5 - 5 |
ES [kWh/1.000 m3] | 0,2 - 1,5 | 1,2 - 3 | 1 - 2 | 2 - 6 | 1,5 - 6 |
Tabelle 3.5.3
Bauarten und typische Kenngrößen von Massenkraftabscheidern, elektrischen und nassarbeitenden Abscheidern [42]
Bezeichnung | Massenkraftabscheider | Elektrische Abscheider | Nassarbeitende Abscheider | |||
---|---|---|---|---|---|---|
Bauformen | Schwerkraft /Umlenk-Abscheider | Fliehkraft-Abscheider (Zyklon) | Trockenelektrofilter | Nasselektrofilter | Dynamische Wäscher Wirbelwäscher | Venturiwäscher |
Systembild (Beispiele) | ![]() | ![]() | ![]() | ![]() | ![]() | ![]() |
Wirkungsweise | Abscheidung Partikel durch | Aufladung von festen oder flüssigen Partikeln in einem elektrischen Feld und Abscheidung auf Niederschlagselektroden. Abscheidegrad stark abhängig von spez. Staubwiderstand, Partikelkonzentration und Geschwindigkeit. Abreinigung der Niederschlagsplatten durch: | Benetzung und Bindung der Partikel an in den Gasstrom eingebrachten Flüssigkeitsschleier | |||
Schwer- und Trägheitskräfte | Fliehkräfte aus einer rotierenden Strömung | Umlenkung der partikelbeladenen Luft und der Flüssigkeit durch feste oder rotierende Einbauten | Wassereindüsung in eine Venturidüse mit Bildung eines homogenen Tropfenschleiers | |||
Klopf- oder Rütteleinrichtungen oder bei kleinen Geräten im ausgebauten Zustand | Abspülen mit Wasserrieselfilm | |||||
Abscheidegrad vor allem abhängig von der Partikelmasse und Geschwindigkeit | ||||||
Tropfenabscheidung durch Massenkraftabscheider | ||||||
Einsatzgebiete Bemerkungen | In allen Industriebereichen für grobe Partikel, bei geringen Anforderungen an den Abscheidegrad als Vorabscheider oder Funkenfänger für nachgeschaltete filternde Abscheider | In nahezu allen Industriebereichen, Zement-, Stahl- und chemische Industrie, Rauchgasentstaubung, Feuerungsanlagen, Ölnebel- und Schweißrauchabscheidung | Vorzugsweise in der Chemie- und Metallindustrie für feuchte Abluftströme, explosive Staub-Luft-Gemische, klebrige und stark hygroskopische Stäube | |||
bei höheren Temperaturen bis ca. 500 °C | Bei feuchtem Abgas, Aerosolen und klebrigen Stäuben | Trenngrenze bis 1 µm | Trenngrenze 0,1 µm | |||
Volumenströme | bis 100.000 m3/h | bis 500.000 m3/h | bis 50.000 m3/h | |||
Druckverluste | 300-600 Pa | 500-1.500 Pa | 200-500 Pa | 400-800 Pa | 1.500-3.000 Pa | 3.000-20.000 Pa |
Rohgaskonzentration | nicht begrenzt | bis ca. 50 g/m3 | bis ca. 50 g/m3 | |||
Reingaskonzentration | 50-500 mg/m3 | Auszulegen auf den zulässigen Emissionsgrenzwert | ||||
Abscheidegrad | 50-90 % | 90-99 % | 90-95 % | 95-99 % | ||
Vorteile | Einfach, robust, kostengünstig; geringer Druckverlust, unempfindlich gegen Druck und hohe Temperatur | Hohe Abscheideleistung für Feinstäube und Aerosole möglich, sehr geringer Druckverlust, niedrige Energiekosten | Unempfindlich gegen Feuchtigkeit, Brand- und Explosionsschutz, gleichzeitige Gaskühlung Schadgasabsorption möglich | |||
Nachteile | Geringe Abscheideleistung, für Feinstäube ungeeignet | Hoher Reinigungsaufwand bei kleinen Baueinheiten | Wasser-/Schlammaufbereitung und Entsorgung erforderlich | Begrenzte Abscheideleistung für Feinstäube | Hohe Abscheideleistung nur bei sehr hohem Druckverlust |
3.5.2.4
Filternde Abscheider
Bei filternden Abscheidern lassen sich unabhängig von der Feinheit des Staubs sehr hohe Abscheidegrade erzielen. Durch immer widerstandsfähigere Filtermaterialien nimmt die Bedeutung der filternden Abscheider stetig zu! Filternde Abscheider lassen sich wie wie in Abb. 3.5.6 dargestellt grob einteilen.
Die häufig anzutreffenden Faserschichtfilter lassen sich weiter einteilen in:
Speicherfilter (Partikelabscheidung im Innern der Faserschicht, Tiefenfiltration)
Abreinigungsfilter (Partikelabscheidung überwiegend an der Filteroberfläche, Abreinigung durch Rütteln, Spülluft oder Druckluftimpulse)
Speicherfilter arbeiten mit Tiefenfiltration und müssen nach einer Sättigung mit Partikeln, die sich im steigenden Differenzdruck und sinkenden Volumenstrom ausdrückt, erneuert werden. Sie sind dann sinnvoll, wenn nur wenig Staub abgeschieden werden muss (z. B. Klimatechnik, Raumlüftung). Abreinigungs-Filter sind dagegen auch für hohe Rohgasbeladungen bis zu 200 g/m3 geeignet. Das Filtervlies ist meist zu Schläuchen oder Taschen vernäht oder wird zu Filterelementen plissiert. Neben Abreinigungsfiltern aus Filtervlies gewinnen bei verschiedenen Anwendungen Patronenfilter oder Filterkerzen aus keramischen und metallischen Materialien (Fasern, Sinterwerkstoffe) immer mehr an Bedeutung. Allgemein steigt auch bei Abreinigungsfiltern der Druckverlust bei der Bildung einer Staubschicht auf dem Filter zunächst an und fällt nach der Abreinigung wieder ab. Bei den Abreinigungsverfahren wird häufig mit Rütteln, Spülluft oder Druckluftimpuls gearbeitet.
Tabelle 3.5.4 stellt verschiedene Filterklassifikationen dar, die sich aus verschiedenen Filterprüfnormen ergeben. Während die beiden Normen DIN EN ISO 16890 und DIN EN 1822 aufeinander abgestimmt sind, werden bei der DIN EN 60335 die Filterklassifizierungen unter anderen Prüfbedingungen bestimmt, weshalb sie nur bedingt miteinander vergleichbar sind:
Die Filterklassen nach DIN EN ISO 16890 werden als Partikel-Luftfilter der allgemeinen Raumlufttechnik eingesetzt. Die Filter werden im Test nach einem Partikelspektrum von 0,3 bis 10 µm bewertet. Eingeteilt werden die Filter in Feinstaubklassen PM1, PM2,5 und PM10 sowie Grobstaub (ISO coarse, Abscheidegrad ist < 50 % der PM10-Partikelfraktion). Scheidet ein Filter mindestens 50 % der Partikelfraktion PM10 ab, kann er Feinstaubklasse ISO ePM10 zugeordnet werden (e steht für Effizienz). Entsprechendes gilt für die Feinstaubklassen ISO ePM2,5 und ISO ePM1. Zusätzlich wird bei der Filterklassifizierung noch in 5-%-Schritten (immer nach unten abgerundet) zum Beispiel angegeben, wieviel % der PM10-Partikelfraktion abgeschieden wurde. Werden zum Beispiel von einem Filter 62 % der PM10-Partikelfraktion zurückgehalten, heißt die Klassifizierung ISO ePM10 60 %. So ergeben sich 49 unterschiedliche Filterklassen. Als Prüfmedien werden KCl (Kaliumchlorid) für 2,5 und 10 µm sowie DEHS (Di-Ethyl-Hexyl-Sebacat) für 0,3-1,0 µm eingesetzt.
Die Klassifizierung "L", "M" und "H" beruht auf der DIN EN 60335 und gilt für Filter für staubbeseitigende Maschinen mit Reinluftrückführung. Angegeben wird hierzu der Durchlassgrad für einen Prüfstaub, bei dem 61 % der Partikel kleiner sind als 1 µm.
Die Klassifikation von HEPA- und ULPA-Filtern beruht auf der DIN EN 1822 und gilt für Schwebstofffilter. Angegeben wird jeweils der Abscheidegrad für einen Prüfstaub, dessen Partikel am schlechtesten abgeschieden werden können und deren Größe zwischen 0,1 und 0,3 µm liegt.
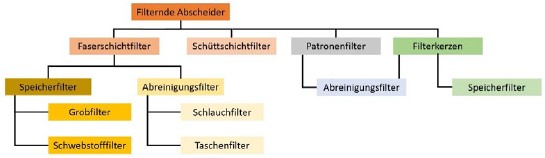
Abb. 3.5.6
Einteilung von filternden Abscheidern nach Bauarten
Tabelle 3.5.4
Übersicht verschiedener Filterklassifizierungen nach verschiedenen Normen
Partikelfilter für die Allgemeine Raumlufttechnik DIN EN ISO 16890-1:2016 | Schwebstofffilter (EPA, HEPA, ULPA) DIN EN 1822:2011 | Filter für staubbeseitigende Maschinen (Staubsauger, Entstauber), Luftrückführung in Arbeitsräume, DIN EN 60335-2 (2010) 2:2010 | ||||||||||||
---|---|---|---|---|---|---|---|---|---|---|---|---|---|---|
Filtergruppe | 49 Filterklassen | Prüfstaub/Aerosol | geforderte Mindestleistung | Filtergruppe | Filterklasse | Prüfaerosol | Integraler Abscheidegrad im MPPS [%] | Lokaler Abscheidegrad im MPPS [%] | Staubklasse | Prüfstaub/Prüfaerosol | max. Durchlassgrad [%] | geeignet für | ||
ePM1, min | ePM2,5, min | ePM10, min | ||||||||||||
ISO Coarse | 20 % | ISO A2-Staub ("Grobstaub" 0,97-176 µm, davon 59,5 % < 11 µm) | < 50 % Abscheidegrad | E (EPA: Efficient Particulate Air filter, Hochleistungspartikelfilter) | E10 | DEHA (Di-Ethyl-Hexyl-Sebacat) 0,1-0,3 µm | ≥ 85 | - | L | 200 mg/m3 Quarzstaub | < 1 | Stäube mit AGW > 1 mg/m3 | ||
25 % | ||||||||||||||
E11 | ≥ 95 | - | M | 90 % 0,2-2 µm (Stokes) | < 0,1 | < 0,1 Stäube mit AGW > 0,1 mg/m3 | ||||||||
... | ||||||||||||||
E12 | ≥ 99,5 | - | H | 10-80 mg/m3 Praffinölnebel 90 % < 1 µm (Stokes) | < 0,005 | Stäube mit AGW, krebserzeugende Aerosole, Stäube mit Krankheitserregern | ||||||||
95 % | ||||||||||||||
ISO ePM10 | 50 % | KCl (Kaliumchlorid) für 2,5 und 10 µm; DEHS (Di-Ethyl-Hexyl-Sebacat) für 0,3-1,0 µm | ≥ 50 % Abscheidegrad im elektrisch entladenen Zustand | H (HEPA: High Efficiency Particulate Air filter, Schwebstofffilter) | E13 | ≥ 99,95 | ≥ 99,75 | |||||||
... | ||||||||||||||
E14 | ≥ 99,995 | ≥ 99,975 | ||||||||||||
> 95 % | ||||||||||||||
ISO ePM2,5 | 50 % | ≥ 50 % Abscheidegrad im elektrisch entladenen Zustand | U (ULPA: Ultra Low Penetrating Air filter, Hochleistungs-Schwebstofffilter) | U15 | ≥ 99,9995 | ≥ 99,9975 | ||||||||
... | U16 | ≥ 99,99995 | ≥ 99,99975 | |||||||||||
> 95 % | U17 | ≥ 99,999995 | ≥ 99,999975 | |||||||||||
ISO ePM1 | 50 % | ≥ 50 % Abscheidegrad im elektrisch entladenen Zustand | ||||||||||||
... | ||||||||||||||
> 95 % |
Anmerkungen: Die beiden Normen DIN EN ISO 16890-1 und DIN EN 1822 sind aufeinander abgestimmt und bauen aufeinander auf. Wegen unterschiedlicher Prüfbedingungen zwischen der DIN EN 60335-2 und diesen beiden Normen ist ein Vergleich der Staubklassen mit den Filterklassen bzw. der Abscheidegrade nur bedingt möglich. Prinzipiell ist der Durchlassgrad = 1 - Abscheidegrad. Bei den Filtergruppen der DIN EN ISO 16890-1 steht ISO Coarse für Abscheidegrad in % bei ISO A2-Staub ("Grobstaub"), aber < 50 % Abscheidegrad im Bereich PM10 (0,3-10 µm Partikelgröße) (Beispiel: ISO Coarse 95 % = Feinstaubabscheidegrad PM10 < 50 %, aber Anfangsabscheidegrad liegt zwischen 95 und 100 % für groben ISO A2-Staub), ISO ePM10 für ≥ 50 % Abscheidegrad im Bereich PM10, ISO ePM2,5 für ≥ 50 % Abscheidegrad im Bereich PM2,5 (0,3-2,5 µm Partikelgröße), ISO ePM1 für ≥ 50 % Abscheidegrad im Bereich PM1 (0,3-1 µm Partikelgröße), Filterklasseneinteilung in 5 %-Schritten von 50 bis 95 %, jeweils Abrundung auf nächsten 5 %-Schritt. Bei den Staubklassen der DIN EN 60335-2 steht L für leichte, M für mittlere und H für hohe Gefährdung.
Die folgenden beiden Bilder verdeutlichen die Abscheidemechanismen an Faserschichtfiltern:
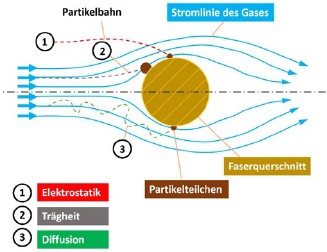
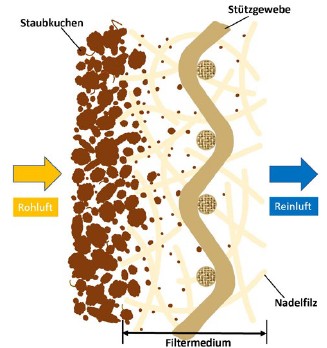
Abb. 3.5.7
Abscheidemechanismen bei Faserschichtfiltern (oben) und Querschnitt eines mit Staub
belegten Filtermediums (unten), Prinzipskizzen [30]
Bei sehr kleinen Partikeln spielt der Diffusionseffekt durch die Brownsche Molekularbewegung die dominierende Rolle. Diese kleinen Partikel folgen nicht den Stromlinien des Gasstroms. Bei unterschiedlicher elektrischer Aufladung von feinsten Partikeln und Filterfaser wirken elektrische Kräfte. Mit zunehmender Partikelgröße nimmt der Massenträgheitseinfluss weiter zu. Am schlechtesten lassen sich Partikelgrößen zwischen 0,1 und 2 µm mit Faserfiltern abscheiden. Filterhersteller geben häufig bei Schwebstofffiltern die Größe MPPS an (most penetrating particle size = Partikelgröße, die sich vom Filtermaterial am schlechtesten abscheiden lässt).
Ein weiterer Abscheidemechanismus ist der Siebeffekt (siehe Abbildung 3.5.7 unten): Wenn die Partikel größer werden als der Faserabstand oder als die Partikelabstände der schon auf dem Filter vorhandenen Staubschicht, stellt sich der Siebeffekt ein.
Der Porenvolumenanteil (Porosität) liegt bei Speicherfiltern noch höher als bei Abreinigungs-Filtern, was sich jedoch während des Abscheideprozesses durch die zunehmende Einlagerung der Partikel in die Speicherfilter verändert - so wird ein Speicherfilter immer undurchlässiger, der Abscheidegrad steigt, der Differenzdruck steigt und der Volumenstrom sinkt, so dass ab einem gewissen Mindestvolumenstrom (Strömungswächter) oder einem maximalen Differenzdruck (Differenzdruckwächter) eine Warnanzeige den Wechsel des Speicherfilters anzeigen muss.
Auch bei neuen Abreinigungs-Filtern lagern sich feinste Partikel in das Filtermaterial ein, verändern die Porosität und steigern den Abscheidegrad. Im Wesentlichen bildet sich aber ein "Staubkuchen" auf der Oberfläche von Abreinigungs-Filtern, der zunehmend die Aufgabe des Filtermaterials übernimmt. Auch hier nimmt der Druckverlust bei wachsendem Staubkuchen zu, bis der Filter abgereinigt wird. Um das Abreinigungs-Verhalten zu verbessern, wird die Oberfläche häufig geglättet oder beschichtet (z. B. mit PTFE). Sehr gute Abscheide-Eigenschaften erhält man zum Beispiel durch eine Beschichtung des Filtermaterials mit Membranen, Feinfaserauflagen oder Nanofaserauflagen [30]. Hierdurch wird besonders das Durchschlagen des Staubs während der Abreinigung verhindert. Den gleichen Effekt hat man bei mit einer PTFE-Membran überzogenen Filtern aus gesintertem Material. Bei abrasiven Medien werden solche Beschichtungen oder Membrane schnell im Betrieb zerstört.
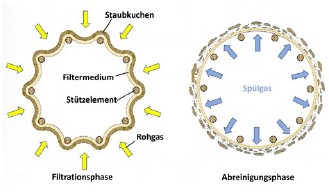
Abb. 3.5.8
Filtrations- und Abreinigungsphase im Druckluftimpuls-Verfahren bei einem Filterschlauch
[30]
Bei Oberflächenfiltern aus Faserfiltermedien wird im Filtrationsbetrieb eventuell eine Stützkonstruktion benötigt, um die konfektionierten Filterelemente in Form zu halten und ein Kollabieren infolge des anstehenden Differenzdrucks zu vermeiden. Starrkörperfilter sind eigenstabil und benötigen diese zusätzliche Stützkonstruktion nicht.
Handelt es sich bei den abgeschiedenen Partikeln um Gefahrstoffe, ist es sinnvoll, in den anfangs leeren Behälter einen Beutel zur gefahrlosen Entsorgung einzubringen, damit nicht der Sammelbehälter noch durch Schütten entleert werden muss. Dadurch würden viele Partikel wieder aufgewirbelt: Das sollte vermieden werden! Statt des hier dargestellten Auffangbehälters für die abgeschiedenen Partikel könnten auch Förderschnecken, Zellenradschleusen oder Ähnliches dafür sorgen, dass die abgeschiedenen Partikel in einem geschlossenen Fördersystem zur weiteren Verarbeitung oder Entsorgung kontinuierlich ausgetragen werden.
Die Filtertaschen bei Taschenfiltern müssen über ebene, plattenförmige Rahmen gespannt werden, die an einer Seite für die gereinigte Luft offen sein müssen. Die Rohluft tritt horizontal oder von oben in das Filtergehäuse ein und durchströmt die Filtertaschen von außen nach innen.
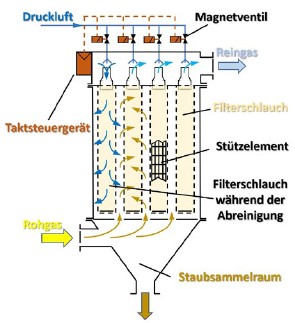
Abb. 3.5.9
Schlauchfilter mit Druckluftimpuls-Verfahren zur Abreinigung [2]
In Schlauchfiltern sind die Filterschläuche zylindrisch und haben Durchmesser zwischen 0,09 und 0,27 m und eine Länge von bis zu 10 m. Sie müssen bei der Durchströmung von außen nach innen über einen zylindrischen Stützkorb gezogen oder mit Stützringen versehen werden, was bei umgekehrter Strömungsrichtung nicht unbedingt erforderlich ist. Die Abreinigung von Schlauch- und Taschenfiltern kann mechanisch (Rütteln, Klopfen, Vibrieren, meist bei gleichzeitigem Einsatz von Spülluft) oder durch das Druckluftimpulsverfahren erfolgen. Dabei wird mit einem Luftdruck von bis zu 7 bar gearbeitet, wobei die Druckluftventile nur 0,1 bis 0,4 s geöffnet werden. Das Zeitintervall zwischen den Druckluftstößen ist unterschiedlich. Durch den Druckluftimpuls innen im Schlauch auf der Reinluftseite blähen sich Schläuche oder Taschen stoßartig auf und werfen dadurch den an der Oberfläche anhaftenden Staub auf der Rohluftseite wieder ab.
Der Hauptgrund, aus dem sich das Druckluftimpuls-Regenerations-Verfahren immer mehr gegen die mechanische Rüttel-Abreinigung durchsetzt, ist die Tatsache, dass es eine bessere Wirkung erzielt und eine Online-Abreinigung (Regeneration bei paralleler Beaufschlagung) zumindest partiell möglich ist. Das ermöglicht eine etwas höhere Filterflächenbelastung, weil sich beim Betrieb niemals ein so dichter Filterkuchen bildet wie bei der seltener getätigten Rüttel-Abreinigung. Ein Nachteil des Druckluftimpuls-Regenerations-Verfahrens ist der mögliche Staubdurchschlag in Form von Emissionsspitzen während des Regenerations-Vorgangs durch im Filtermaterial eingelagerten Staub. Die Abreinigung kann über eine Differenzdrucksteuerung ausgelöst werden. So werden die Abreinigungs-Vorgänge auf ein Minimum reduziert.
Bei der Auslegung von abreinigbaren Filtern ist die schon erwähnte Filterflächenbelastung (= Filtrationsgeschwindigkeit vF) eine entscheidende Größe: Sie ist definiert als der auf die Filterfläche AF bezogene Gas-/Luftvolumenstrom V̇g:

mit
vF | = | Filtrationsgeschwindigkeit/Filterflächenbelastung [m3/(m2 h)] bzw. [m/h] |
---|---|---|
V̇g | = | Gas-/Luftvolumenstrom [m3/h] |
AF | = | Filterfläche [m2] |
Bei bekannter Filtrationsgeschwindigkeit oder Filterflächenbelastung kann so die erforderliche Filterfläche bestimmt werden. Die Filterflächenbelastung oder Filtrationsgeschwindigkeit selbst wird entweder experimentell bestimmt oder kann aus bereits ausgeführten Anlagen abgeleitet werden. Nach [32] kann sie auch mithilfe eines Grundwerts unter Berücksichtigung von Korrekturfaktoren bestimmt werden, die folgenden Einflussgrößen Rechnung tragen:
Filtersystem
Anwendungsart
Staubfeinheit
Rohgasbeladung
Temperatur
chemische und physikalische Staubeigenschaften
Anströmverhältnisse
zulässiger Reststaubgehalt
Filtermedium
Aus der Praxis ergeben sich beispielhaft daraus die in Tabelle 3.5.5 angegebenen Filterflächenbelastungen bei abreinigbaren Filtern mit Druckluftimpuls-Abreinigung für verschiedene Stäube oder Anwendungsfälle.
Tabelle 3.5.5
Typische Filterflächenbelastungen in der Praxis nach Planungshinweisen der Infastaub GmbH [8]
Staubarten/Anwendung | Filterflächenbelastung bei Schlauch- oder Taschenfiltern [m3/(m2*h)] | |
---|---|---|
Eisenoxide (Ofenentstaubung im Stahlwerk) | 60 - 90 | |
Flugasche aus Kohleverbrennung Bereich Handling, Verbrennung abhängig von Vorabscheidung und Verbrennungsart | 60 - 90 30 - 90 | |
Gipsstaub (Gipsbrennen) | 60 - 96 | |
Holzstaub (Schleifstaub mit Leimanteil) | 66 - 150 | |
Sandaufbereitung in Gießereiformsand | 60 - 120 | |
Thermische Spritzverfahren von Aluminium | 30 - 36 | |
Weizenvermahlung | 150 - 246 | |
Zinkoxidstaub (Absaugung über Zinkbad) | 60 - 90 | |
Zementstaub (Förderung, Verladung) | 66 - 120 | |
Zuckersichtung | 66 - 120 | 66 - 120 |
Tabelle 3.5.6 fasst die Bauarten filternder Abscheider mit Wirkungsweisen, wichtigen Kenngrößen, Einsatzgebieten, Vor- und Nachteilen zusammen.
Bei der praktischen Auslegung von Abreinigungsfiltern ist die Kenntnis des zu erwartenden Druckverlusts Δp bei gegebener Filterflächenbelastung vF oft wichtiger als der Abscheidegrad.
So findet sich in der Fachliteratur die sogenannte Fundamentalgleichung für Mehrkammerfilter [2], die aus dem Gesetz von D’Arcy für laminare Durchströmung abgeleitet wurde:

mit
Δp | Druckverlust als Gesamtdruckverlust aus Filtermedium und Filterkuchen [bar] |
---|---|
KF | experimentell ermittelter Widerstand des Filtermediums |
KK | experimentell ermittelter Widerstand des Filterkuchens auf dem Filtermedium |
vF | Filterflächenbelastung/Filtrationsgeschwindigkeit [m3/(m2 h)] |
CA | Rohluftstaubbeladung [g/m3] |
tE | Taktzeit bis zur Filterabreinigung (Dauer der Filtrationsperiode) [h] |
Die experimentell zu ermittelnden Widerstände KF und KK hängen außerdem von den Eigenschaften des Filtermaterials und des Staubs, von der Filterflächenbelastung und der Abreinigungs-Intensität ab. Diese Methode ermöglicht aber Aussagen über den zu erwartenden Druckverlust Δp bei unterschiedlichen Taktzeiten tE und Rohluftstaubbeladungen CA.
Tabelle 3.5.6
Bauarten, Wirkungsweisen, Einsatzgebiete, Kenngrößen und Vor- und Nachteile filternder Abscheider [42]
Bezeichnung | Speicherfilter | Schlauchfilter | Taschenfilter | Taschenfilter | Patronenfilter | Kompaktfilter | Sinterfilter | |
---|---|---|---|---|---|---|---|---|
Abreinigung | ohne Abreinigung | Druckluftimpuls | Druckluftimpuls | Spülluft | Vibration | Druckluftimpuls | Druckluftimpuls | Druckluftimpuls |
Systembild | ![]() | ![]() | ![]() | ![]() | ![]() | ![]() | ![]() | ![]() |
Wirkungsweise | Abscheidung von Partikeln am Filtermedium durch Massenkräfte, Sperreffekt, Diffusion, elektrostatische Kräfte. Abscheidevorgang abhängig von Partikelgröße und -konzentration, Agglomerationsverhalten, Gastemperatur und -feuchte, Anströmgeschwindigkeit und Aufbau des Filtermediums | |||||||
Partikel werden in Wirrfasermatten oder plissierten Papier- oder Kunstfasern gespeichert. In der Regel nicht regenerierbar | Bildung eines die Filterwirkung unterstützenden Filterkuchens - Regeneration durch zyklische Abreinigung mittels Druckluftimpuls, Gegenspülung bzw. Vibration | |||||||
Flexible Filtermedien aus vorwiegend synthetischen Vliesen oder Nadelfilzen als dreidimensionale Tiefenfilter oder als Oberflächenfilter durch Verdichtung, Beschichtung oder Membranen Schläuche auf Stützkörbe aufgezogen nur vertikal oder mit eingenähten Stützringen einbaubar Taschen auf Stützrahmen aufgezogen horizontal oder vertikal einbaubar | Starre, selbsttragende Filterelemente | |||||||
aus sternförmig gefalteten Papier- oder Kunstfasern vertikaler oder schräger Einbau | aus plissierten, thermofixierten Kunstfasern, auch mit Membrane, horizontal oder vertikal | aus gesinterten Kunststoffen, meist mit PTFE-Beschichtung oder aus Keramiksinter, horizontal o. vertikal | ||||||
Einsatzgebiete Bemerkungen | Zu-, Ab- und Umluftfilter in der Raumlufttechnik Farb- und Ölnebelabscheidung Sekundärfilter nach Abreinigungsfiltern | Breites Anwendungsgebiet zur Abscheidung vorzugsweiser trockener Partikel aus industrieller Abluft und Abgasen, Temperaturbereiche bei Filtermedien aus Kunstfasern bis ca. 260 °C, aus Metall und Keramik bis ca. 800 °C. Feuchte Rohgase, zum Anbacken neigende Stäube oder chemischer Angriff nur bei Verwendung für den speziellen Einsatzfall geeigneter Filtermedien möglich | ||||||
Vorwiegend mittlere bis große Anlagen für alle Anwendungsbereiche und kontinuierlichen Betrieb | Vorwiegend dezentrale Entstaubungsgeräte für diskontinuierlichen Betrieb | Kleinere bis mittelgroße Anlagen für kontinuierlichen Betrieb, auch für Feinstäube | ||||||
Volumenströme | 500 bis 100.000 m2/h | 5.000 bis 500.000 m3/h | 1.000 bis 100.000 m3/h | 10.000 bis 150.000 m3/h | 500 bis 10.000 m3/h | 300 bis 10.000 m3/h | 1.000 bis 100.000 m3/h | 1.000 bis 100.000 m3/h |
Anströmgeschwindigkeit | bis ca. 2,5 m/s | 1,0 bis 3,5 m/min | 1,0 bis 3,5 m/min | 0,5 bis 1,5 m/min | 0,5 bis 2,0 m/min | 0,5 bis 1,5 m/min | ||
Druckverluste | 100 bis 600 Pa | 600-2.000 Pa | 600-2.000 Pa | 1.000-2.500 Pa | 800-2.000 Pa | 1.500-3.000 Pa | ||
Rohgaskonzentration | maximal 20 mg/m3 | bis ca. 100 g/m3 | bis ca. 50 g/m3 | bis ca. 10 g/m3 | bis ca. 5 g/m3 | bis ca. 20 g/m3 | ||
Reingaskonzentration | 0,01-1 mg/m3 | 1-10 mg/m3 | 0,5-10 mg/m3 | 5-10 mg/m3 | 0,5-10 mg/m3 | 0,1-1 mg/m3 | ||
Vorteile | Hohe Abscheideleistung für feinste Stäube möglich | Anpassung an unterschiedlichste Betriebsbedingungen durch große Auswahl verschiedener Filtermedien und sehr effektive Abreinigung, niedrige Reststaubgehalte durch Trend zur Oberflächenfiltration | Preiswerte Komplettgeräte mit Ventilator und Staubsammelbehälter, mobile Ausführung möglich | Etwa doppelte Filterfläche gegenüber Taschenfiltern auf gleichem Raum, geringer Verschleiß und lange Standzeiten der Filterelemente, kaum Partikeldurchtritt beim Druckluftimpuls, hohe Abscheidegrade auch bei Feinststäuben, z. B. metallurgische Rauche | ||||
Großanlagen durch große Schlauchlängen kostengünstig, Vorabscheidung im Bunker bei hohen Staubkonzentrationen | Rohgasführung von oben nach unten kann Staubaustrag unterstützen, wartungsfreundlich durch horizontalen Taschenauszug | Geringe Wieder- und Gegenbeaufschlagung, schonende Off-line-Abreinigung, geringer Verschleiß des Filtermediums, sehr wartungsfreundlich | Bis zu 10-fache Filterfläche gegenüber Schlauchfilter auf gleichem Raum | Hohe chemische bzw. Temperaturbeständigkeit | ||||
Nachteile | Nur sehr geringe Rohgaskonzentrationen Während des Betriebs ansteigender Druckverlust, Standzeit maximal 6 Monate | Wegen großer Bauhöhen i. allg. nicht für Innenaufstellung | Taschengröße für Großanlagen begrenzt | Für kleinere Anlagen hoher Investitionsaufwand, verfügbare Filterfläche durch Spülwagen reduziert | Abreinigung nur diskontinuierlich, hoher Verschleiß und Staubdurchtritt beim Abrütteln | Hohe Strömungsgeschwindigkeiten, mögliches Zusetzen bei enger Sternfaltung | Geringere Flächenbelastung gegenüber Taschen | Vergleichsweise hohe Druckverluste, geringer flächenbelastbar |
Erhöhter Verschleiß und Partikeldurchtritt beim Druckluftimpuls möglich | Nur für trockene und freifließende Stäube bei geringer Filterfächenbelastung |
Schüttschichtfilter werden nur bei klebrigen oder abrasiven Stoffen oder bei sehr hohen Gastemperaturen angewendet, sofern es für diese Bedingungen noch kein geeignetes Faserschichtfiltermaterial gibt. Je nach Wahl des Schüttguts kann neben der Staubabscheidung in Schüttschichtfiltern auch eine Schadgasadsorption erfolgen. Das Schüttgut kann aus Kies, Sand, Kalkstein oder Koks im Korngrößenbereich von 0,3 mm bis ca. 5 cm bestehen. Die Schichthöhe kann mehrere Meter betragen. Die zu reinigende Luft sollte mit 0,5 bis zu 2 m/s (Leerrohrgeschwindigkeit) durch die Schüttung strömen. Auch bei Schüttschichtfiltern ist eine Reinigung des Filtermediums durch Gegenstromspülung, durch mechanisches Rütteln in Verbindung mit Spülluft oder durch verschiebbare Düsen möglich. Die zu reinigende Filtereinheit muss jedoch während des Abreinigungs-Vorgangs vom Luftstrom getrennt werden. Eine kontinuierliche Luftreinigung und eine gleichzeitige Filter-Abreinigung ist in einer einfachen Schüttschichtfiltereinheit nicht möglich.
Anders sieht es bei einem sogenannten Gegenstrom-Schüttelfilter aus, bei dem die zu reinigende Luft in der Regel von unten einströmt und das Schüttgut von unten nach oben durchströmt, während das Schüttgut als Filtermaterial ständig im Gegenstrom von oben her erneuert und das beladene Schüttgut unten abgezogen wird. Es kann dann gereinigt und dem Filter anschließend oben wieder zugeführt werden. Schüttschichtfilter haben eine schlechtere Abscheideleistung als Faserschichtfilter.
Deshalb werden sie nur bei schwierigen Einsatzbedingungen verwendet:
bei harten und verschleißenden Stäuben
bei hohen Temperaturen (bis zu 1.000 °C)
bei Gefahr von Funkenflug
bei zündfähigen Stäuben
bei zusätzlicher Entfernung gasförmiger Gefahrstoffe (z. B. SO2, HCL, HF) durch Zusatz von gebrochenem Kalkstein
3.5.3 Abscheidung von dampf- und gasförmigen Stoffen
3.5.3.1
Kondensationsverfahren
Enthält die abgesaugte Luft Zusatzstoffe, die als flüchtige Bestandteile aus der Abluft abgeschieden werden sollen, weil sie nicht mit der Abluft ins Freie gelangen dürfen oder weil sie als Wertstoff zurückgewonnen werden sollen (z. B. Lösemittel), können Kondensat-Abscheider eingesetzt werden. Kondensat-Abscheider sind verfahrenstechnisch "Kühlfallen" zur Auskondensierung von Stoffen aus dem Luftstrom durch Unterschreitung des Taupunkts. Dazu kann eine Abkühlung auf sehr tiefe Temperaturen notwendig sein. Für die Anwendung dieses Verfahrens ist die Kenntnis der Dampfdruckkurven beziehungsweise der Lösemittelkonzentrationen bei Sättigung (Sättigungskonzentration) unerlässlich.
Tabelle 3.5.7
Charakteristische Daten typischer Adsorbenzien [2]
Adsorbens | Schüttdichte [kg/m3] | Spezifische Oberfläche [m2/g] | Desorptions-Temperaturbereich (°C) |
---|---|---|---|
Aktivkohle | 300 bis 500 | 1.000 bis 1.500 | 100 bis 150 |
Aktivkohle engporig | 400 bis 500 | 600 bis 1.000 | 100 bis 150 |
Aktivkoks | 600 | 100 | 300 bis 500 |
Kohlenstoff-Molekularsieb (CMS) | 600 bis 890 | ||
Zeolithisches Molekularsieb (ZMS) | 650 bis 750 | 800 bis 1.100 | 200 bis 300 |
3.5.3.2
Adsorptionsverfahren
Unter Adsorption versteht man die Bindung von Gasen und Dämpfen an die Oberfläche eines festen, porösen Stoffes (Adsorbens). Adsorptionsfilter sind mit Pufferspeichern vergleichbar, die die Gase und Dämpfe bis zur vollständigen Beladung der spezifischen Oberfläche zurückhalten, aber nicht komplett beseitigen. Wenn die Oberfläche komplett beladen ist ("Pufferspeicher ist voll"), kommt es zum sogenannten Durchbruch. Dennoch ist die Adsorption das am häufigsten eingesetzte Verfahren zur Gasabscheidung. Als Adsorbenzien werden zum Beispiel Aktivkohle (bei Bedarf imprägniert und in mehreren Schichten), Silicagel, Zeolithe oder makroporöse Polymere eingesetzt, die sehr große spezifische Oberflächen aufweisen.
Die Adsorption kann dabei in einem Festbett-, Fließbett- oder Wirbelbett-Adsorber durchgeführt werden. Verbreitet sind Festbett-Adsorber, zum Beispiel in Form von Filterplatten oder Filterpatronen, die mit dem Adsorbens befüllt werden. Das Adsorbens muss regelmäßig vor Erreichen des Sättigungszustands ausgetauscht oder durch Desorption regeneriert werden. Die begrenzte Standzeit und das Erkennen des richtigen Wechselzeitpunkts stellt beim Betrieb von Adsorptionsabscheidern ein grundsätzliches Problem dar.
3.5.3.3
Absorptionsverfahren
Bei der Absorption werden gasförmige oder dampfförmige Luftverunreinigungen (Absorptiv) in einer Waschflüssigkeit als Lösemittel aufgenommen und entweder nur gelöst (physikalische Absorption) oder gelöst und zusätzlich chemisch in lockere chemische Verbindungen umgesetzt (chemische Absorption). Die in der Waschflüssigkeit aufgenommene Komponente heißt dann Absorpt. Durch physikalische Absorption lassen sich zum Beispiel Ammoniak, Schwefeloxide oder Stickoxide in einem Wäscher auswaschen. Für Schadstoffe wie Phosgen, Brom-, Chlor-Fluor- oder Schwefelwasserstoff verwendet man wässrige Waschmedien (Absorbenzien), die mit alkalischen Zusätzen wie Natrium- oder Calcium-Hydroxid, Natriumcarbonat oder Ammoniak versehen sind. Ein verbreitetes Beispiel für die chemische Absorption ist auch die Abscheidung von Aminen aus der Kern-Formherstellung in Gießereien, bei der die aminbeladene Abluft mit verdünnter Schwefelsäure neutralisiert wird.
Die Apparate, die man für eine Absorption benötigt, wurden bereits unter Abschnitt 3.5.2.1.3 "Nasswäscher" vorgestellt. Auch für die Absorption muss eine möglichst große Kontaktfläche zwischen zu reinigender Luft und Waschflüssigkeit hergestellt werden. Das kann zum Beispiel durch Sprühwäscher, Glockenbodenkolonnen oder Füllkörperkolonnen geschehen.
3.5.3.4
Oxidationsverfahren (thermisch und katalytisch)
Bei der thermischen (Temperaturbereich ϑFO = 750 °C ... 1.200 °C) und der katalytischen (Gegenwart von Katalysatoren, Temperaturbereich ϑFO = 200 °C ... 400 °C) Oxidation werden unerwünschte Abluftbestandteile (z. B. Anteile mit C, H und O in organischen Verbindungen) durch Umsetzung mit Sauerstoff in unbedenkliche Stoffe (idealerweise in CO2 und H2O) überführt.
Im Idealfall setzt ein Katalysator die notwendige Aktivierungsenergie (Reaktionstemperatur) herab und nimmt letztlich nicht an der Verbrennungs-Reaktion teil. Ein Zusatzbrennstoff (z. B. Erdgas) dient dazu, die Brennkammer auf die notwendige Reaktionstemperatur aufzuheizen. Folglich ist bei der katalytischen Verbrennung weniger Zusatzbrennstoff notwendig. Zu beachten ist dabei, dass stickstoff-, schwefel- oder halogenhaltige organische Abluftbestandteile zu unerwünschten Nebenreaktionsprodukten führen können. Bei unvollständiger Verbrennung (z. B. bei zu wenig O2 oder zu hoher Strömungsgeschwindigkeit) können ebenso unerwünschte Nebenprodukte wie CO oder Formaldehyd entstehen.
Eine typische Anwendung ist die Reinigung kohlenwasserstoffhaltiger oder lösemittelhaltiger Abluftströme in der chemischen Industrie oder aus Lackieranlagen in der Automobilindustrie.
Die Tabelle 3.5.8 zeigt einige Beispiele von Oxidationsverfahren in der Abluftreinigung mit der zu erwartenden Temperaturerhöhung:
Tabelle 3.5.8
Beispiele von eingesetzten Oxidationsverfahren in der Abluftreinigung [2]
Einsatzgebiet | Emittierte Schadstoffe | Temperaturerhöhung durch Verbrennung in °C | |
---|---|---|---|
Art | Konzentration in g/m3N | ||
Lacktrocknung, PVC-Verarbeitung | Lösemittel | 0,5 bis 15 | 20 bis 400 |
Papierbeschichtung | Lösemittel, Styrol | bis 10 | bis 350 |
Folienbeschichtung, Tiefdruck, Druckmaschinen | Xylol, Toluol | 5 bis 20 | 150 bis 600 |
Drahtlackierung | Phenol, Kresol, Formaldehyd | 0,5 bis 1,0 | 15 bis 30 |
3.5.3.5
Biologische Abluftreinigung
Die biologische Abluftreinigung erfolgt mit Biowäschern oder Biofiltern und beruht auf dem Abbau von organischen Stoffen durch Mikroorganismen, wobei im Idealfall CO2 und H2O als Endprodukte verbleiben. Dieser Vorgang wird auch als biologisches Sorptionsverfahren bezeichnet.
Biowäscher werden in Apparate mit Belebtschlamm (Belebtschlamm-Verfahren) und Apparate mit Tropfkörper (Tropfkörper-Verfahren) eingeteilt.
Beim Belebtschlamm-Verfahren sind die Mikroorganismen in einer Waschflüssigkeit (überwiegend Wasser) frei beweglich und nehmen dort die Schadstoffe als Nahrung auf. So bilden die Mikroorganismen mit der Waschflüssigkeit den Belebtschlamm. In sogenannten Belebungsbecken wird die Waschflüssigkeit regeneriert.
Bei den Tropfkörper-Verfahren befinden sich lose Schüttungen oder feste Packungen (Füllkörper) als Einbauten in Waschapparaten. Auf diesen Einbauten sind die Mikroorganismen als "biologischer Rasen" fest angesiedelt. Sie werden ständig mit einer umlaufenden Waschflüssigkeit benetzt.
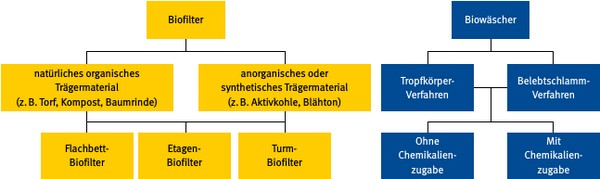
Abb. 3.5.10
Einteilung der biologischen Sorptionsverfahren in Biofilter und Biowäscher [2]
Biofilter bestehen aus einer Schüttung aus organischem Trägermaterial (z. B. Torf-Heidekraut) als offene Flächenfilterbeete oder sind als gekapselte Fallstrom-Filter mit anorganischem oder synthetischem Trägermaterial (z. B. Aktivkohle, Blähton) ausgeführt.
Der Einsatzbereich von Biowäschern hat sich inzwischen auf geringkonzentrierte Abluftströme mit biologisch abbaubaren Inhaltsstoffen erweitert (z. B. bei organischen Lösemitteln in Lackieranlagen oder Gießereien, siehe folgendes Anlagenbeispiel).
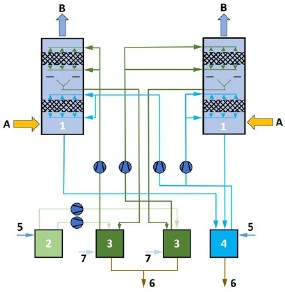
In der Darstellung bedeuten:
A Rohgas
B Reingas
1 Gaswäscher
2 Nährlösungsbehälter
3 Belebungsbecken
4 Wasserbehälter für die Vorwäsche
5 Frischwasser
6 Schlamm
7 Belüftung
Abb. 3.5.11
Biologische Gaswäsche in einer Metallgießerei als schematische Darstellung