Abschnitt 4.1 - 4 Planung der Gesamtanlage
4.1 Bauarten von Absauganlagen
Absauganlagen werden aus verschiedenen Einzelkomponenten für den jeweiligen Absaugbedarf im konkreten Anwendungsfall zusammengestellt. Die Auswahl der jeweils einzusetzenden Einzelkomponenten richtet sich nach Art, Menge und Eigenschaften der zu erfassenden, zu fördernden und abzuscheidenden Stoffe, den jeweiligen Umgebungsbedingungen und den angestrebten Projektierungszielen. Nähere Einzelheiten zur Auswahl und zum Einsatzspektrum der auszuwählenden Bauteile sind dem Abschnitt 3 "Konzeption und Dimensionierung der Komponenten" dieser Schrift zu entnehmen.
Die nachfolgenden Ausführungen beschreiben praxisrelevante Möglichkeiten zur Zusammenfügung der Bauteile zu komplexen Anlagen und erläutern Vorzüge und Nachteile der angesprochenen Lösungen für bestimmte Anwendungsfälle.
Um ihre Aufgaben zur Erfassung, Förderung und Abscheidung von Schadstoffen aus dem Arbeitsbereich der Beschäftigten erfüllen zu können, bestehen Absauganlagen grundsätzlich aus den folgenden Komponenten:
- 1.
Bauteile zur Erfassung der Schadstoffe am Entstehungsort/Arbeitsplatz (sofern nicht Bestandteil einer stauberzeugenden Maschine)
- 2.
Rohrleitungen zum leitungsgebundenen und gegen Umgebungseinflüsse abgeschirmten Abtransport der erfassten Schadstoff-Luft-Gemische
- 3.
Ventilatoren (in Spezialfällen auch "Verdichter") als Strömungsmaschinen zur Erzeugung der erforderlichen Luftleistung innerhalb der Anlage
- 4.
Abscheider zur Trennung der Schadstoffe von der Transportluft, wenn erforderlich
- 5.
Einrichtungen zur Ableitung der gereinigten Transportluft als Abluft aus dem Abscheider, wenn erforderlich
- 6.
Einrichtungen zum Sammeln oder zur Abführung der abgeschiedenen Schadstoffe aus dem Abscheider zur Weiterbehandlung oder temporären Zwischenlagerung
Neben diesen Basisbestandteilen werden in Abhängigkeit von den Einsatz- und Umgebungsbedingungen noch Einrichtungen zur Steuerung und/oder Regelung der an den Erfassungsstellen und in den Absaugleitungen im Einzelfall bereitzustellenden Luftmengen sowie zu deren Überwachung eingesetzt.
Werden Schadstoffe mit gefährlichen Eigenschaften erfasst und transportiert, sind darüber hinaus spezielle Sicherheitsbauteile vorzusehen. In Abhängigkeit von den Vorschriften für den Umgang mit dem jeweiligen Schadstoff sind außerdem Einrichtungen zur Überwachung der Einsatz- und Betriebsbereitschaft erforderlich.
Für den strukturellen Aufbau von Absauganlagen gibt es grundsätzlich verschiedene Konzeptionen mit jeweils mehreren Untervarianten. Die Kriterien sind die Zusammenfassung von Absaugstellen im Leitungsnetz, die Zahl der Ventilatoren und ihre Anordnung innerhalb der Anlage.
Alle Konzeptionen haben spezifische Vor- und Nachteile, so dass die Planung der Anlage immer auf den konkreten Einzelfall abgestimmt sein muss.
4.1.1
Strukturelle Anlagenvarianten
Im Wesentlichen werden drei Varianten des strukturellen Aufbaus einer stationären Anlage unterschieden.
Bei der Zentralabsaugung werden alle Absaugstellen über einen gemeinsamen Ventilator abgesaugt. Bei der Gruppenabsaugung werden mehrere Absaugstellen zu Gruppen zusammengefasst, die jede mit einem eigenen (Gruppen-) Ventilator abgesaugt werden. Demgegenüber wird bei der Einzelabsaugung jede an die Absaugung angeschlossene Absaugstelle über einen separaten Ventilator abgesaugt.
Die technisch optimale Lösung ist natürlich die Einzelabsaugung, weil hier die Ventilatoren in einem einzigen Betriebspunkt arbeiten, so dass sie optimal auf diesen Punkt und damit auf den Absaugleistungsbedarf der angeschlossenen Verbrauchsstelle ausgelegt werden können. Dadurch sind in vielen Fällen die Betriebskosten für Energie relativ gering; gleichzeitig ergeben sich wegen der größeren Anzahl an Ventilatoren höhere Investitionskosten.
Weitere wirtschaftliche Nachteile entstehen, wenn alle oder mehrere Absaugleitungen Brandwände durchstoßen oder mit Funkendetektions- und -löschanlagen überwacht werden müssen. Außerdem ist bei dieser Lösung der Aufwand im Bereich der zu verlegenden Rohrleitungen von allen Varianten am größten.
Die im Hinblick auf die Investitionskosten günstigste Variante ist die Zentralabsaugung. Absaugtechnisch ist sie jedoch in Betrieben mit stark wechselnden Luftanforderungen die ungünstigste Lösung, weil zur Aufrechterhaltung eines für die Ablagerungsfreiheit benötigten minimalen Transportluftstroms relativ große, für die Absaugung der Verbrauchsstellen eigentlich nicht benötigte, Luftmengen abgesaugt werden müssen. Das verursacht relativ hohe Betriebskosten (Strom). Zur Gewährleistung der Ablagerungsfreiheit müssen für Betriebszustände mit geringem Volumenfluss daher bei der Anwendung der Zentralabsaugung häufig zusätzliche technische Maßnahmen, zum Beispiel Schieber-Steuerung, Beiluft-Klappen oder Luft-Injektoren, installiert werden. Das erhöht im Regelfall den Steuerungs- und Überwachungsaufwand für die Anlage im Vergleich zur Einzelabsaugung erheblich.
Die Gruppenabsaugung stellt einen Kompromiss zwischen den beiden anderen Varianten dar und vereinigt deren Vor- aber auch Nachteile. Ob es gelingt, überwiegend die Vorteile der Einzelabsaugung bei der Optimierung der Betriebspunkte und dem relativ niedrigeren Energiebedarf zur Wirkung zu bringen und die entsprechenden Nachteile der Zentralabsaugung zu vermeiden, hängt weitgehend davon ab, wie gut die Auslegung im Einzelfall an den tatsächlichen Absaugbedarf und die Umgebungsbedingungen angepasst ist.
4.1.2
Ventilator-Anordnung
Bei der Anordnung der Ventilatoren in der Anlage gibt es folgende Varianten:
a. Rohgasseitige Ventilator-Anordnung
Die Ventilatoren sind in Strömungsrichtung vor dem Abscheider in die Rohgasleitung eingebaut und blasen in ihn ein. Damit steht bei dieser Anordnung der Abscheider unter Überdruck. Besonders bei filternden Abscheidern können Undichtigkeiten zu hohen Schadstoff-Belastungen im Umfeld führen.
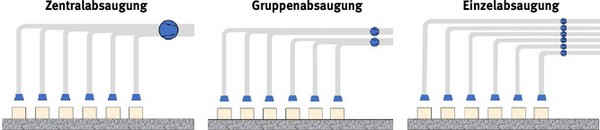
Abb. 4.1.1
Struktur-Varianten von Absauganlagen
Beim pneumatischen Transport von abrasiven, gröberen Stoffbestandteilen werden die Ventilatoren im Rohgasbereich stark belastet. Das Ventilator-Gehäuse kann durch Anprall stückiger Bestandteile deformiert werden und das Laufrad kann durch Materialanbackungen in Unwucht geraten. Die Beschaufelung unterliegt durch Abrasion hohem Verschleiß. Die notwendigerweise zu verwendenden Laufräder in offener Bauweise erzielen zudem einen relativ geringen Wirkungsgrad.
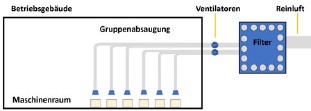
Abb. 4.1.2
Schemaskizze für Rohluftanlagen
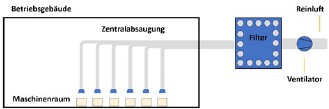
Abb. 4.1.3
Schemaskizze für Reinluftanlagen
Anmerkung:
Bei größeren Luftmengen werden bei Anwendungen mit gleichbleibender Luftmenge rohgasseitig von einzelnen Herstellern Industrieventilatoren mit geschlossenen Laufrädern in massiver Bauweise eingesetzt. Diese Industrieventilatoren haben die oben erwähnten Nachteile nicht.
Die rohgasseitige Anordnung war früher die verbreitetste Anlagenbauform. Anlagen mit rohgasseitiger Ventilator-Anordnung und offenen Laufrädern werden heute - wenn überhaupt - normalerweise nur in der Variante als Gruppenabsaugung in Industriebetrieben mit gleichmäßigem Luftleistungs-Bedarf über den Tag konzipiert. Zentralabsaugungen als Rohluftanlagen sind wegen der oben erwähnten Nachteile heute nicht mehr so üblich. Eine Ausnahme bilden Kleinstanlagen mit sehr wenigen Absaugstellen und jeweils einheitlich geringem Luftleistungs-Bedarf.
b. Reingasseitige Ventilator-Anordnung
Bei dieser Bauweise ist der Ventilator in Strömungsrichtung nach dem Abscheider in die Abluftleitung eingebaut. Der Abscheider steht dabei zwangsläufig unter Unterdruck. Ein Schadstoffaustritt aus dem Abscheider ist somit nur bei möglichen Undichtigkeiten der Filter, Filterelementköpfe oder Abdichtungen zwischen Rohluft- und Reinluftbereich möglich. Allerdings unterliegt das Abscheider-Gehäuse durch den permanenten Unterdruck hohen Belastungen. Eventuell in der Folge auftretende Undichtigkeiten können zu großen Falschluft-Einströmungen in das Gehäuse führen und damit die "Volumenstrom-Nutzleistung" der Anlage deutlich reduzieren.
Vorteile der reinluftseitigen Anordnung des Ventilators ergeben sich aus der Tatsache, dass der Ventilator und sein Laufrad keinerlei Belastung und Verschleiß durch Materialeinflüsse ausgesetzt sind. Außerdem können mögliche, vom Ventilator erzeugte, Zündquellen nicht wirksam werden, sofern im Reinluftbereich - wie im Regelfall gegeben - keine explosionsfähige Atmosphäre vorhanden ist oder diese über eine Reststaubgehaltsüberwachung rechtzeitig erkannt wird. Die bei Reinluft-Ventilatoren verwendeten geschlossenen Laufräder führen im Regelfall zu höheren Ventilator-Wirkungsgraden als offene Laufräder, wie sie meistens bei Rohluft-Ventilatoren zum Einsatz kommen.
Der wesentliche Nachteil bei reingasseitiger Ventilatoranordnung besteht darin, dass systembedingt nur ein bestimmter Unterdruck erzeugt werden kann. Eine individuelle Anpassung an die einzelnen Rohrstränge ist damit nur durch Energievernichtung (z. B. Drosseleinrichtungen) möglich. Moderne Bearbeitungsmaschinen - mit den für diese Maschinen typischerweise zur wirksamen Absaugung erforderlichen hohen Unterdrücken von bis zu 3.000 Pa - erzwingen Unterdrücke am Filter von 5.000 Pa und mehr. Diese Drücke sind für Filteranlagen in rechteckiger Paneel-Bauweise zumeist zu hoch. Der Einsatz von Stützventilatoren, wie in Abschnitt 4.1.3.1 beschrieben, wird dadurch notwendig und reduziert die energetischen Vorteile in solchen Fällen erheblich.
Anlagen mit reingasseitiger Ventilator-Anordnung sind vom Prinzip her meistens als Zentralabsaugungen konzipiert, wobei die Maschinen aber durchaus über Einzelleitungen oder gruppenweise zusammengefasste Rohrleitungen an die Filteranlage angeschlossen sein können.
Der Zentralventilator wird häufig mit variabler Drehzahl betrieben. Außerdem muss er nicht unbedingt ein Einzelventilator sein, sondern kann auch als Ventilator-Einheit mit mehreren, parallel geschalteten Ventilatoren ausgeführt sein. Zudem muss der Ventilator nicht unbedingt in einer reinluftseitigen Rohrleitung oder Abluftleitung angeordnet sein. Ebenso möglich ist die Anordnung des Ventilators/der Ventilatoren im Filter-Kopf oberhalb der Regenerations-Einrichtung im Reinluftbereich des (filternden) Abscheiders.
In den nachfolgenden Bildern der Tabelle 4.1 sind die für die Praxis wesentlichen Anlagensysteme skizziert.
4.1.3
Anlagen mit mehreren Ventilatoren
In sehr vielen Fällen ist es unzureichend oder unwirtschaftlich, alle Verbraucher eines Betriebs über nur einen einzigen Ventilator abzusaugen. Randbedingungen, bei denen der Einsatz mehrerer Ventilatoren vorteilhafter ist als der Einsatz nur eines einzigen Ventilators, sind große Unterschiede bei:
Tabelle 4.1
Prinzip-Skizzen häufiger Systeme von Absauganlagen
Rohluftseitige Ventilator-Anordnung | ![]() | ![]() | ![]() |
---|---|---|---|
Reinluftseitige Ventilator-Anordnung | ![]() | ![]() | ![]() |
den Strömungswiderständen der einzelnen Verbraucher,
dem Volumenstrombedarf der einzelnen Verbraucher,
der Auslastung der einzelnen Verbraucher,
der Auslegung der Anlage (Betriebszustände) sowie
sehr weitläufige Maschinenaufstellungen (große Leitungslängen).
In diesen Fällen können angepasste Lösungen gefunden werden, bei denen einzelne Ventilatoren nur genau definierte Aufgaben übernehmen. So kann die Anlage auf konkrete "Problemfälle" besser zugeschnitten werden. Außerdem ergibt sich vielfach auch ein deutlich geringerer Energiebedarf, da die Ventilator-Leistung bedarfsgerechter eingesetzt werden kann.
In den folgenden Abschnitten sollen die für die Praxis relevanten Kombinationen behandelt werden.
4.1.3.1
Reihenschaltung von Ventilatoren
Zur Überwindung höherer Druckdifferenzen in einer Absauganlage kann man zwei oder mehrere Ventilatoren hintereinander (in Reihe) schalten (siehe Abb. 4.1.4 auf Seite 98). Dabei addieren sich theoretisch die Gesamtdruckdifferenzen der einzelnen Ventilatoren, während der Volumenstrom konstant bleibt.
Häufig findet man diese Anordnung in Absaugsystemen, bei denen einzelne Verbraucher hohe Druckanforderungen für die Erzielung ausreichender Volumenströme benötigen und nicht die gesamte Anlage auf diese Druckanforderungen ausgelegt werden soll. Die entsprechenden Zusatz-Ventilatoren werden in diesen Fällen häufig in die Zuleitung zu dem fraglichen Verbraucher als "Stützventilatoren" eingebaut, um in dieser Leitung die benötigten Zusatz-Drücke zu erzeugen.
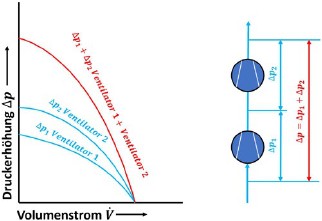
Abb. 4.1.4
Qualitativer Kurvenverlauf der Kennlinie zweier in Reihe geschalteter Ventilatoren
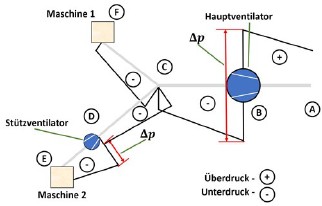
Abb. 4.1.5
Druckverlauf bei Reihenschaltung von zwei Ventilatoren
Die Abbildung 4.1.5 zeigt den Druckverlauf entlang einer Rohrleitung bei der Reihenschaltung von zwei Ventilatoren.
Die Aufgabe von Stützventilatoren besteht darin, das Unterdruckniveau an einzelnen, besonders strömungsungünstig konstruierten, Verbrauchern soweit anzuheben, dass ausreichende Luftgeschwindigkeiten erzielt werden können, ohne den Hauptventilator auf die sonst erforderlichen extremen Pressungen auslegen zu müssen.
Weiterhin kommen Stützventilatoren zum Einsatz, wenn Betriebsteile räumlich weit abgelegen sind und für die abgelegen positionierten Verbraucher kein eigener Abscheider (z. B. Filteranlage) vorhanden ist. Die zusätzliche Pressung der Stützventilatoren wird in diesen Fällen zur Überbrückung der Leitungswiderstände benötigt.
4.1.3.2
Parallelschaltung von mehreren Ventilatoren
Bei der Parallelschaltung von Ventilatoren sind zwei oder mehrere Ventilatoren nebeneinander im Leitungsnetz angeordnet. Bei gleichen Pressungen addieren sich die Volumenströme. Es ergibt sich eine Summenkennlinie, die sich aus den Volumenströmen der Ventilatoren zusammensetzt.
Die Kennlinie von parallel geschalteten Ventilatoren ermittelt man, indem die Volumenströme bei gleichen Gesamtdruckdifferenzen addiert werden (siehe Abbildung 4.1.6).
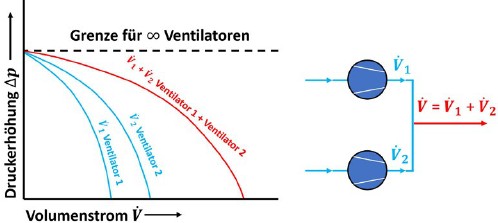
Abb. 4.1.6
Qualitativer Kurvenverlauf der Kennlinie zweier parallel geschalteter Ventilatoren
Häufig wird zur Erhöhung der Anlagensicherheit eine Parallelschaltung von Ventilatoren eingesetzt. Ein größerer Ventilator würde zwar die benötigte Leistung erbringen, stattdessen werden aber mehrere kleinere Ventilatoren zu einer sogenannten Ventilator-Einheit zusammengefasst.
So kann beim Ausfall eines Ventilators eine Grundversorgung sichergestellt werden, ohne dass, wie beim Einsatz nur eines einzigen Ventilators, die komplette Anlage ausfallen würde. Außerdem ist eine Steuerung möglich, denn beim Einsatz mehrerer Ventilatoren können einzelne zu- oder abgeschaltet werden, um so den jeweils benötigten Volumenstrom zu erreichen.
4.1.3.3
Parallelschaltung von Ventilatoren mit variabler Drehzahl
Für die Parallelschaltung variabler Ventilatoren gelten die gleichen Grundüberlegungen wie für die Parallelschaltung von Ventilatoren mit festen Drehzahlen. Die grundsätzliche Funktionsweise von Ventilatoren mit variabler Drehzahl und die Realisierungsmöglichkeiten von variablen Drehzahlen können Abschnitt 3.8. entnommen werden.
In der Praxis gibt es Kombinationen aus einem (Grundlast-)Ventilator mit in der Regel variabler Drehzahl und einem bis vier (Teillast-)Ventilatoren mit konstanter Drehzahl, die bei Erreichen des Nennvolumenstroms des geregelten Ventilators sukzessive zugeschaltet werden.
4.1.3.4
Ventilator-Überlagerung bei mehreren rohluftseitig angeordneten Ventilatoren, die in einen gemeinsamen Abscheider einblasen
Ein alltägliches Problem, bei dem sich mehrere, rohluftseitig angeordnete Ventilatoren die gesamte Absaugleistung teilen, ergibt sich bei herkömmlichen Gruppenabsaugungen oder - als Sonderfall - Einzelabsaugungen aller angeschlossenen Erfassungsstellen. Wenn hierbei die Ventilatoren - wie im Regelfall üblich - in eine einzige Filteranlage entsorgen, besteht über diese Filteranlage eine Verbindung zwischen den Ventilatoren, sodass diese nicht mehr unabhängig voneinander betrieben werden. Bei dieser Konstellation ergibt sich mit steigendem Volumenstrom ein höherer Filterwiderstand. Die zur Überwindung dieses Filterwiderstands notwendige Pressung führt zu einer Verschiebung der Arbeitspunkte der einzelnen Ventilatoren hin zu niedrigeren Volumenströmen. Die Ventilatoren hemmen sich also gegenseitig.
Bei einer in der üblichen Weise dimensionierten Filteranlage (100 m3/m2/h Filterflächenbelastung, Filterwiderstand max. 500 Pa bei 100 m3/m2/h) stellt sich normalerweise eine Verminderung der Luftgeschwindigkeit im Stutzen des Ventilators von ca. 10 %, bei einer Ausgangsluftgeschwindigkeit von 20 m/s, also etwa 2 m/s, ein.
Probleme mit der Leistung solcher Anlagen gibt es vor allem dann, wenn
die Filteranlage zu klein ist, da dann die Filterflächenbelastung und damit die Filterwiderstände stark anwachsen und/oder
einzelne Ventilatoren sich deutlich im Pressungsverhalten von den anderen Ventilatoren unterscheiden und diese quasi überdrücken, weil sie mit ihrer Presskraft den Überdruck in der Filteranlage hochtreiben.
4.1.4
Kompakte Absauggräte für Stäube (Entstauber)
Entstauber sind als Alternative zu stationären Absauganlagen, gerade für Kleinbetriebe, zu sehen und dienen zum Absaugen einzelner oder weniger Verbraucher. Es gibt diese kompakten Absauggeräte üblicherweise mit Anschluss-Durchmessern von 100 mm bis 355 mm und Nennvolumenströmen bis 8.000 m3/h.
Hinweis:
Geräte mit einem höheren Nennvolumenstrom (Anschluss-Durchmesser größer ca. 355 mm) sind eventuell lieferbar, liegen aber außerhalb des Anwendungsbereichs von EN 16770. Ob zusätzliche Gefährdungen bei einer Innenaufstellung von größeren Geräten entstehen, ist unklar. Somit werden vorerst auch keine geprüften Geräte dieser Größe auf den Markt kommen.
Als kompakte Absauggeräte beinhalten sie alle wesentlichen Funktionen einer stationären Zentral-Absauganlage, nur in meist deutlich kleinerem Maßstab:
einen reinluftseitig angeordneten Ventilator
eine Filtereinheit (Patrone, Taschenfilter oder Schlauch)
Einrichtungen zur Regeneration des Filters
einen Vorabscheider
eine Sammel- oder Austrageinrichtung
einen Abluftauslass
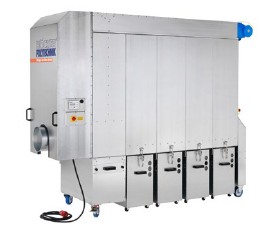
Abb. 4.1.7
Entstauber als vollständiges Kompakt-Gerät
Gehen von den abzusaugenden Schadstoff-Luft-Gemischen Gesundheits- und/oder Brand- und Explosionsgefahren aus, werden zusätzliche Anforderungen an die Abscheidequalität und/oder den Brand- und Explosionsschutz gestellt. In diesem Fall dürfen nur Entstauber im Arbeitsraum aufgestellt werden, die diese zusätzlichen Anforderungen erfüllen.
Kompaktgeräte können bei einer zertifizierten Prüfstelle einer speziellen Prüfung auf EG-Konformität unterzogen und entsprechend zertifiziert werden. Sie sind häufig ortsbeweglich (fahrbar) ausgeführt und können als Betriebsmitteleinheit gehandelt werden.
Ist der Entstauber ausreichend leistungsfähig, können an ihn kleinere Rohrnetze angeschlossen werden, sodass für den Handwerksbetrieb kompakte Absauganlagen realisiert werden können. Da die maximal vertretbare Gleichzeitigkeit meist sehr gering ist (1 - 3 Absaugstellen) müssen in aller Regel Automatikschieber zur Sicherstellung ausreichender Absaugleistungen installiert werden.
Die Entsorgung des abgeschiedenen Materials kann wahlweise über einen Sammelbehälter, eine Brikettier-Presse oder eine Zellenradschleuse mit vor- und/oder nachgeschalteter Schnecke erfolgen. Abbildung 4.1.8. zeigt eine Schemaskizze für einen fahrbaren Entstauber zum Absaugen einer kleineren Einzelmaschine. In Abbildung 4.1.9. ist der Aufbau eines größeren Kompakt-Geräts schematisch dargestellt.
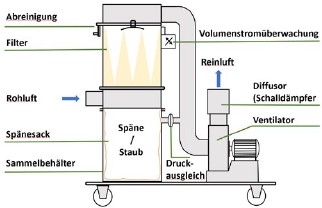
Abb. 4.1.8
Schema-Skizze eines Entstaubers zum Absaugen von Einzelmaschinen
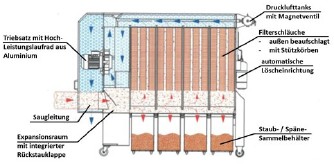
Abb. 4.1.9
Schematischer Aufbau eines größeren Kompakt-Geräts
Ein Nachteil ist, dass die Vorabscheidung bei kompakten Absauggeräten aufgrund der beengten Platzverhältnisse nur schwer umgesetzt werden kann.
Für einen einwandfreien Betrieb solcher Geräte sind zwei Punkte von besonderer Bedeutung.
- 1.
Um beim Betrieb ein Einsaugen der in den Sammelbereichen eingelegten Abfüllsäcke in die Filterschläuche zu vermeiden, oder das Füllvolumen maximal zu halten, wird mit einer Verbindung zwischen der Saugseite kurz vor dem Ventilator (Reingasseite) und der Sammeltonne gleiches Druckniveau geschaffen. So erreicht man in dem Zwischenraum zwischen Tonne und Abfüllsack einen Unterdruck gegenüber dem Sackinneren. Der Sack wird also förmlich an die Tonnenwandung angesaugt.
- 2.
Die in den Geräten eingesetzten Filterschläuche oder Filterpatronen haben oft einen kleinen Durchmesser und/oder nur sehr geringe Abstände voneinander. Das kann bei einem höheren Anteil von gröberen oder faserförmigen Stoff-Bestandteilen zu Problemen führen. Die Bestandteile können aufgrund der sich ergebenden hohen Steiggeschwindigkeiten (Kaminwirkung) in die Schläuche (bei Innenbeaufschlagung) oder in die Zwischenräume (bei Außenbeaufschlagung) gezogen werden, sich untereinander vernetzen und bei der anschließenden Regeneration nicht ausfallen. Es kommt zu Verstopfungen und das Gerät wird unbrauchbar.
4.1.5
Absauganlagen für Kleinverbraucher
Neben den stationären Bearbeitungsmaschinen und anderen größeren Luftverbrauchern gibt es in vielen Betrieben eine Reihe von kleineren, meistens handgeführten Maschinen oder Elektrowerkzeugen, sogenannte Kleinverbraucher, die nachweislich mindestens ebenso viel zur Schadstoffbelastung am Arbeitsplatz beitragen wie die genannten größeren Stationär-Emittenten.
Die Verwendung solcher Maschinen konzentriert sich häufig auf gesonderte Arbeitsbereiche oder -räume, in denen keine stationären Absauganlagen installiert sind. Deshalb werden solche Maschinen heute häufig über ortsbewegliche Kleinentstauber abgesaugt. Die Zahl der im Betrieb benötigten Kleinentstauber ergibt sich dabei aus der Zahl der gleichzeitig zu bedienenden Arbeitsplätze, da über solche Geräte immer nur eine Maschine gleichzeitig abgesaugt werden kann.
Die Betriebe müssen dann aber eine große Zahl von Kleinentstaubern beschaffen und empfinden auch den Umgang mit ihnen als schwierig, weil die Länge des Anschlussschlauchs begrenzt ist, die Schläuche schwer sind, die im Entstauber integrierten Sammelbehälter durch ihr Gewicht das Handling erschweren und sich ein höherer Wartungsaufwand ergibt. Außerdem können über solche Kleinentstauber meistens ausschließlich handgeführte Maschinen, nicht aber kleinere stationäre Bearbeitungsmaschinen abgesaugt werden, die sich häufig ebenfalls in größerer Zahl in diesen Arbeitsbereichen befinden.
Leistungsfähigere Geräte sind im Hinblick auf die im Betrieb benötigte Anzahl zu teuer. In vielen Betrieben wird deshalb versucht, die Kleinmaschinen ebenfalls über eine gesonderte Leitung an die vorhandene Absaugung für stationäre Bearbeitung anzuschließen, in der Regel mit völlig unbefriedigendem Ergebnis.
Warum die Absaugung von Elektrowerkzeugen über die Absauganlage, mit der auch die stationären Bearbeitungsmaschinen abgesaugt werden, gar nicht oder unzureichend funktioniert, wird klar, wenn man sich die Anschluss-Querschnitte selbst und die Unterdrücke, die zur Erzielung einer Luftgeschwindigkeit von 20 m/s im Anschluss-Querschnitt der abzusaugenden Elektrowerkzeuge erforderlich sind, ansieht.
Während für die Absaugung einer typischen stationären Bearbeitungsmaschine durchschnittlich 1.500 m3/h Volumenstrom bei ca. 1.000 Pa Unterdruck erforderlich sind, werden für die Absaugung von Elektrowerkzeugen oder Ähnlichem durchschnittlich nur ca. 70 m3/h Volumenstrom bei allerdings ca. 3.000 Pa Unterdruck benötigt. Einige Maschinen verlangen sogar noch weitaus höhere Unterdrücke.
Zur Lösung des Problems bieten einige Hersteller von Entstaubern/Staubsaugern Absauganlagen an, die speziell auf die geschilderten Randbedingungen abgestimmt sind. Dabei handelt es sich um Zentralabsaugungen auf der Basis größerer Industriestaubsauger oder kleinerer fahrbarer Entstauber.
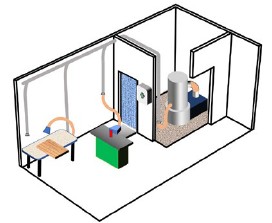
Abb. 4.1.10
Kleine Absauganlage auf der Basis eines Kleinentstaubers
Kernstück der Anlagen sind größere Staubsauger oder kleinere Entstauber, die mehrere Aufgaben erfüllen, die bei stationären Absauganlagen von separaten Anlagenbauteilen übernommen werden. In diese, meist fahrbaren Einheiten sind integriert:
Gebläse (z. T. mehrere Gebläse in einem Gerät)
Filtereinheit/Abscheider mit Regeneration
Staub-/Späne- Sammelbehälter
Reinluftrückführung
Die folgende Abbildung 4.1.11 zeigt ein Beispiel für eine zentrale Kleinabsaugung auf Entstauber-Basis für mehrere Absaugstellen in einen metallverarbeitenden Betrieb.
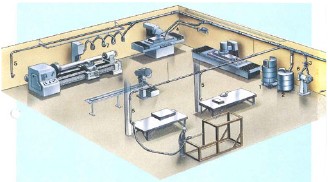
Abb. 4.1.11
Kleinabsaugung für einen typischen kleineren Metallverarbeitungsbetrieb
4.1.6
Absauganlagen zum Materialtransport über kurze Strecken
Größere Mengen an Staub und/oder Grobteilen, die bei der Zerspanung, zum Beispiel bei der Holzbe- und -verarbeitung oder bei der Kunststoffbearbeitung anfallen, können häufig nicht über längere Zeiträume im Bereich der Absauganlage bleiben. Sie müssen in diesen Fällen dann über kürzere oder längere Strecken zu einem größeren Sammelbehälter (Silo) transportiert werden.
Über längere Strecken eignen sich dazu mechanische oder pneumatische Förderanlagen (Hochdruck-Förderung). Beide sind nicht Gegenstand dieser Schrift. Bei Fragen muss an dieser Stelle auf die einschlägige Fachliteratur verwiesen werden.
Besonders in Handwerksbetrieben können jedoch - wegen des dort geringeren Materialanfalls - diese Transportaufgaben auch von Niederdruck-Förderanlagen, also speziellen Absauganlagen, übernommen werden. Zu unterscheiden sind dabei sogenannte "offene Systeme" und "Ringleitungssysteme". Nachfolgend werden die wesentlichen Gesichtspunkte zu Auslegung und Betrieb der beiden Bauarten erläutert.
Bei offenen Systemen wird die Transportluft aus dem Umgebungsbereich im Freien entnommen und über die Förderleitung in den Lagerbehälter transportiert. Das Transportgut wird dabei über eine Austragschleuse in die Leitung eingetragen, sodass es von der strömenden Luft aufgenommen und weitertransportiert werden kann. Damit die (gereinigte) Luft wieder aus dem Lagerbehälter entweichen kann, müssen Vorkehrungen getroffen werden. In der Regel wird eine meist kleine (nur auf die Transportluftmenge ausgelegte) Filteranlage verwendet. Sie kann als Einbaufilter innerhalb des Lagerbehälters oder Aufsatzfilter oberhalb des Lagerbehälters konstruiert sein. Zyklone kommen wegen ihrer, auch für die meist weniger strengen Bedingungen der TA-Luft, unzureichenden Abscheidewirkung in offenen Systemen heute nicht mehr zum Einsatz.
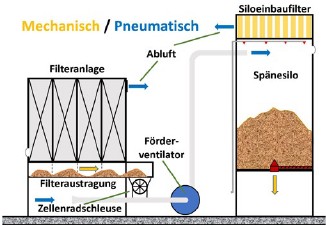
Abb. 4.1.12
Schema einer offenen Förderanlage
Um den Überdruck im Behälter möglichst gering zu halten, muss die Filteranlage mit einer Regenerations-Automatik ausgestattet sein. Durch die Regeneration (Abreinigung) werden die Filterschläuche vom anhaftenden Staubkuchen befreit und die Luftdurchlässigkeit wird so wieder erhöht.
Vor allem in holzverarbeitenden Handwerksbetrieben sind Ringleitungssysteme weit verbreitet. Auch bei diesen Systemen wird das Transportgut über eine Austragschleuse in die Leitung eingetragen und meist mit in einem gutbeladenen Rohluftstrom installierten Transportventilator über eine Steigleitung in das Silo eingeblasen. Der Transportventilator kann aber auch im Reinluftstrom angeordnet sein.
Über eine Rückluftleitung wird die gereinigte "Abluft" wieder vom Ventilator angesaugt, sodass ein Luft-Kreislauf entsteht und der Behälter (Silo) - zumindest theoretisch - druckfrei bleibt. Die Zwischenschaltung von Abscheidern ist zweckmäßig, muss aber für die Funktion des Systems nicht unbedingt sein.
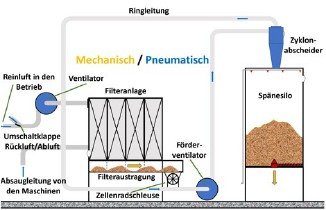
Abb. 4.1.13
Schema eines geschlossenen Ringleitungs-Systems
Dort, wo Abscheider eingesetzt werden, kommen alle bekannten Varianten, wie
Zyklone,
Einbau- und Aufsatzfilter mit oder ohne gesonderte Austragung (Anmerkung: Evtl. brand- und explosionstechnische Anforderungen sind zu berücksichtigen, z. B. die Gehäusefestigkeit bei Aufsatzfiltern.),
Kleinabscheider
in Betracht.
In der Praxis sind Ringleitungssysteme ohne gesonderten Abscheider relativ störanfällig, weil
- 1.
der theoretisch sich einstellende Ausgleich bei den Luftmengen und Drücken im praktischen Betrieb durch Leck-Luftströme und teilweise stark differierende Gutbeladung im Rohluftbereich nicht selten gestört wird, sodass sich im Lagerbehälter unerwünschte Über- oder Unterdrücke einstellen (Anmerkung: Die Transportanlage auf der Basis einer Ringleitung funktioniert dann optimal, wenn sich der Druck-Nullpunkt der Anlage innerhalb des Behälters einstellt.);
- 2.
der Expansionsraum im Behälter durch die Guteintragung stetig verkleinert wird und dadurch die Abscheidewirkung verschlechtert wird; das führt zu einer erhöhten Gutbeladung in der Saugleitung, wodurch bei konstanter Zu-Dosierung die Gutbeladung auch im Bereich der Druckleitung ansteigt. Wenn dann die Pressungsleistung des Ventilators überschritten wird, geht der Volumenstrom zurück, die Förderleitung geht von Flug- in Strähnen-Förderung über, bis schließlich die Förderung komplett zusammenbricht und die Leitung verstopft;
- 3.
in Verbindung mit im Unterdruck stehenden Hauptfilteranlagen und undichten Austragschleusen über das Transportsystem - bei Betrieb der Absauganlage und Stillstand der Transportanlage - Leck-Luftströme aus dem Behälter in die Filteranlage gezogen werden können. Diese Strömung führt zur Unterdruckbildung im Behälter. In vereinzelten Fällen hat sich dieser Unterdruck in der Vergangenheit bis in die Zuführung von den Behältern nachgeschalteten Heizungsanlagen übertragen. Dies führte dann zu einer Umkehr der Rauchgasströmung in den Behälter hinein, mit der Folge von Rückbränden aus der angeschlossenen Feuerung.
Wegen der genannten Probleme und der daraus resultierenden Störanfälligkeit in der Praxis sollten bei der Neuerrichtung solcher Niederdruck-Förderanlagen offene Systeme bevorzugt werden. Bei Verwendung von Ringleitungssystemen ist eine technische Vorrichtung am Silo vorzusehen, die entstehende Über- bzw. Unterdrücke im Silo zwangsläufig (z. B. über ein Ventil)) ausgleicht.