Abschnitt 4.1 - 4 Schutzmaßnahmen für Industrieroboter und Anlagen
4.1 Rangfolge der Schutzmaßnahmen
Die Gesamtheit der Schutzmaßnahmen an einer Roboteranlage ist wie auch an anderen Anlagen oft eine Kombination von Maßnahmen, die vom Konstrukteur der Anlage in der Konstruktionsphase angewendet werden, z. B. Schutzeinrichtungen, und solchen, die vom Benutzer getroffen werden müssen, z. B. Verhaltensanforderungen, persönliche Schutzausrüstungen. Grundsätzlich haben aber die Maßnahmen, die bereits in der Konstruktion berücksichtigt werden können, Vorrang vor allen Maßnahmen, die vom Verwender zu treffen sind.
Erläuterungen zu einer systematischen Vorgehensweise bei der Festlegung von Schutzmaßnahmen durch den Konstrukteur beschreibt EN ISO 12100. Einer der wesentlichen Inhalte ist die Rangfolge der zu treffenden Maßnahmen (Abbildung 25). Die 3-Stufen-Methode beschreibt, dass die Gefährdungen zunächst konstruktiv zu beseitigen sind (unmittelbare Sicherheitstechnik). Ist dies nicht vollständig möglich, müssen Schutzeinrichtungen vorgesehen werden. Nur wenn sowohl konstruktiv als auch durch Schutzeinrichtungen keine vollständige Beseitigung der Gefährdungen möglich ist, dürfen hinweisende Maßnahmen angewendet werden.
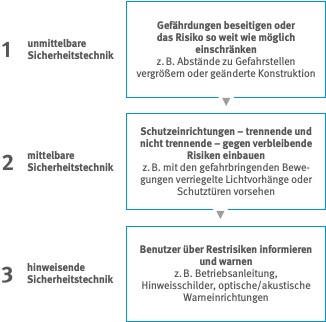
4.1.1 Betriebsarten für Roboter (ohne Peripherie)
Im allgemeinen lässt es sich nicht vermeiden, dass mit den Robotern Einrichtarbeiten nicht nur von außerhalb, sondern auch innerhalb des von Schutzeinrichtungen umgebenen Bereiches durchgeführt werden müssen. Deshalb sind bereits für jeden "nackten" Industrieroboter Betriebsarten zum Einrichten und Programmieren vorzusehen, die dann vom Anlagenbauer eingesetzt werden können.
Nach EN ISO 10218-1 müssen Industrieroboter über die in Tabelle 1 gezeigten Betriebsarten verfügen. Für die Betriebsarten T1 und T2 sowie für Sonderbetriebsarten muss geschultes Personal eingesetzt werden.
Zur Umschaltung der Betriebsarten muss ein abschließbarer Betriebsartenwahlschalter vorgesehen werden, der in jeder Position abziehbar ist (Abbildung 26). Alternative Wahlvorrichtungen, z. B. Zugangscodes, sind ebenfalls zulässig, wenn sie die gleiche Sicherheit bieten. Dabei ist auf die Steuerungssicherheit (Kategorie und PL) und die Möglichkeit des Umgehens von Schutzmaßnahmen (Vorhersehbare Fehlanwendung) zu achten.
In der Betriebsart T2 ist zur Anwahl der hohen Arbeitsgeschwindigkeit neben den in Tabelle 1 aufgeführten Maßnahmen ein zusätzlicher Tastendruck, z. B. auf dem Programmierhandgerät, erforderlich. Die Möglichkeit zur Nutzung der hohen Arbeitsgeschwindigkeit erlischt, sobald der Zustimmungsschalter über eine Zeitdauer von mehr als 5 Minuten unbetätigt bleibt. Will man danach zur hohen Arbeitsgeschwindigkeit zurückkehren, muss diese mittels Drehschalter oder Tastenwahl erneut vorgewählt werden. Die hier geforderte Zeitüberwachung von 5 min ist keine Sicherheitsfunktion.
Weiterhin gilt für die Betriebsart T2, dass bei paralleler Nutzung dieser Betriebsart an mehreren Robotern in einer Zelle die Überschneidung der Bewegungsräume ein hohes Risiko darstellt. Es muss für jeden Bediener ein sicherer Stand gewährleistet sein.
Die in Tabelle 1 angegebene reduzierte Geschwindigkeit beim Einrichten und Programmieren von 250 mm/s bezieht sich auf die Bewegung, gemessen an der Werkzeugaufnahme des Roboters. Die Gefahr besteht im Allgemeinen nur durch Anstoßen.
Betriebsart | Schutzmaßnahme | ||
---|---|---|---|
Manuell reduzierte Geschwindigkeit (T1) z. B. zum Einrichten und Programmieren | Schutzeinrichtungen dürfen geöffnet bzw. unwirksam sein | ![]() | |
• | Gesonderte Stellung des Betriebsartenwahlschalters und | ||
• | Reduzierte Geschwindigkeit*) (= 250 mm/s) in Verbindung mit Zustimmungsschalter und Tippschaltung | ||
Manuell hohe Geschwindigkeit (T2) z. B. zum Testen mit Arbeitsgeschwindigkeit | Schutzeinrichtungen dürfen geöffnet bzw. unwirksam sein | ![]() | |
• | Gesonderte Stellung des Betriebsartenwahlschalters oder zusätzlicher Betriebsartenwahlschalter und | ||
• | Verfahrgeschwindigkeit bis zur vollen Arbeitsgeschwindigkeit und | ||
• | Tippschaltung in Verbindung mit Zustimmungsschalter und | ||
• | Geschützter Standort für den Einrichter, d. h. mind. 0,5 m großer Abstand zw. Umzäunung und Roboter, z. B. durch eingeschränkten Bewegungsraum (siehe auch Abschnitt 4.2.1.3) | ||
Automatik | Schutzeinrichtungen müssen geschlossen bzw. wirksam sein | ![]() | |
• | Gesonderte Stellung des Betriebsartenwahlschalters |
Das Vorsehen einer sicher reduzierten Geschwindigkeit in der Betriebsart T1 sollte nach heutigem Stand der Technik wo immer möglich zum Einsatz kommen (Abschnitt 4.1.3).
Tab. 1 Betriebsarten [F]
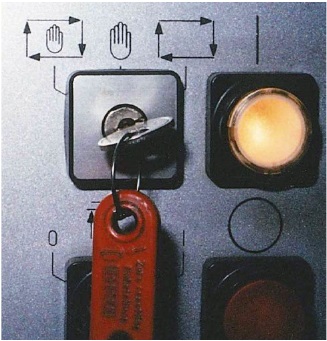
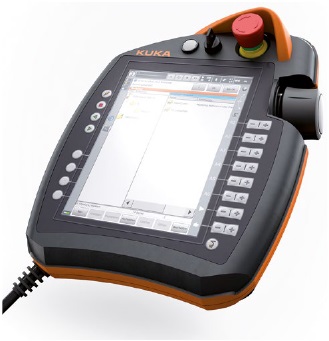
Bei Quetsch- oder Schergefahr, z. B. beim Positionieren einer Vorrichtung, sollte diese Geschwindigkeit entsprechend der Risikobeurteilung weiter reduziert werden.
Der Geschwindigkeitswert der reduzierten Geschwindigkeit (250 mm/s) sollte durch eine sichere Steuerung überwacht werden (siehe Abschnitt 4.1.3). Allerdings lässt EN ISO 10218-1 auch noch die Möglichkeit zu, dass die Geschwindigkeit nicht sicher überwacht wird und dass die Personensicherheit allein mittels des sicheren Zustimmungsschalters hergestellt wird. Ob von dieser Möglichkeit Gebrauch gemacht wird, muss die Risikobeurteilung ergeben, insbesondere im Zusammenhang mit den Anhaltewegen.
Im kollaborierenden Betrieb muss die reduzierte Geschwindigkeit immer sicher überwacht werden (Abschnitt 5).
4.1.2 Zustimmungseinrichtung
Eine Zustimmungseinrichtung (Zustimmungsschalter) ist ein zusätzliches handbetätigtes Befehlsgerät, das in Verbindung mit einer Startsteuerung verwendet wird und, falls es ständig betätigt wird, eine Maschinenfunktion erlaubt. Allein durch Betätigung der Zustimmungseinrichtung darf keine Bewegung gestartet werden. Die Zustimmungseinrichtung muss so ausgelegt sein, dass sie Maschinenbewegungen nur in einer bestimmten Stellung erlaubt. In älteren Anlagen findet man noch zweistufige Ausführungen von Zustimmungseinrichtungen (Tabelle 2).
Für Industrieroboter, die nach Inkrafttreten von EN ISO 10218-1 (Feb. 2007) produziert wurden, dürfen nur noch dreistufige Zustimmungsschalter zum Einsatz kommen. Für den Maschinenaltbestand und für mögliche Nachrüstungen existieren keine europäischen Vorschriften. Möglicherweise existieren aber innerbetriebliche Vorgaben. Sie geben z. B. aufgrund des Unfallgeschehens oder der Durchgängigkeit der Ausrüstung eine bestimmte Ausführungsform vor. Wenn nichts Derartiges vorhanden ist, sollte die Entscheidung aufgrund des vorhandenen Risikos fallen. Dreistufige Zustimmungsschalter schalten auch beim "Verkrampfen" sicher ab. Zweistufige Zustimmungsschalter bieten u. U. ergonomische Vorteile bei lange andauerndem Betätigen, da kein Druckpunkt gehalten werden muss. Bei sehr engen Arbeitsräumen sollte die Wahl zugunsten der dreistufigen Ausführung ausfallen (Reaktionszeit, Verkrampfen).
2-stufig nur für Altbestand zulässig | 3-stufig für Neuanlagen und Altanlagen | |
---|---|---|
Stellung 1 Ruhestellung | Ausfunktion (Stellteil wird nicht betätigt) | Ausfunktion (Stellteil wird nicht betätigt) |
Stellung 2 Freigabestellung | Zustimmungsfunktion (Stellteil wird betätigt) | Zustimmungsfunktion (Stellteil wird in seiner Mittelstellung betätigt) |
Stellung 3 Panikstellung | - | Ausfunktion (Stellteil wird über seine Mittelstellung hinaus betätigt) |
Tab. 2 Ausführungsformen von Zustimmungseinrichtungen
Die in Tabelle 2 angegebenen Funktionen beziehen sich allein auf die Schalteinrichtung. Die Weiterverarbeitung der Signale muss in sicherer Technik erfolgen, z. B. nicht über Standardbussysteme. Wenn bei Betätigung der dreistufigen Ausführung von der dritten in die zweite Stellung zurückgeschaltet wird, darf die Zustimmungsfunktion kein Freigabesignal erzeugen. Mit der Zustimmungseinrichtung allein dürfen keine Bewegungen eingeleitet werden. Zusätzlich ist eine weitere Befehlseinrichtung, z. B. Tippschaltung, notwendig.
Die Signale dieser zusätzlichen Tippschaltung müssen nicht in sicherer Technik verarbeitet werden. Das bedeutet auch, dass bereits beim Drücken des Zustimmungsschalters in Freigabestellung ein Anlaufen der Roboterbewegungen möglich sein kann, auch wenn die eigentliche Verfahrtaste noch nicht betätigt wurde. Dies darf zwar bestimmungsgemäß nicht so vorgesehen werden, kann sich aber aufgrund der geringen Sicherheitsanforderungen für die Tippschaltung zum Beispiel durch einen mit der Zeit eingetretenen Steuerungsfehler ergeben. In den Schulungen der Beschäftigten sollte deshalb darauf hingewiesen werden.
Wenn nicht durch die Risikobeurteilung festgelegt, müssen Zustimmungsschalter und Achsverfahrtaste nicht als Zweihandschaltung ausgelegt werden.
Es ist davon auszugehen, dass sich während des Einrichtens/Programmierens nur der Programmierer im Gefahrbereich aufhält. Dementsprechend sind die in Tabelle 1 angegebenen Schutzmaßnahmen als Schutz für den Programmierer zu betrachten. Müssen sich aus technologischen Gründen weitere Personen im Gefahrbereich aufhalten, sind zusätzliche Schutzmaßnahmen vorzusehen, z. B. zusätzliche Zustimmungsschalter.
Eine Schnittstelle zum Anschluss weiterer Zustimmungsschalter sollte vom Maschinenhersteller von vornherein vorgesehen werden, um auch spätere Erweiterungen zu ermöglichen.
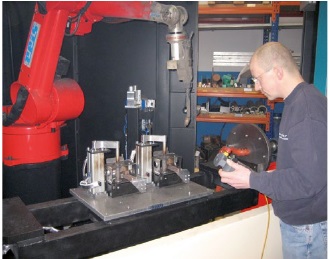
4.1.3 Funktionale Sicherheit der Steuerung
Für sicherheitsbezogene Teile von Steuerungen wird in den Produktnormen für Industrieroboter EN ISO 10218-1 und EN ISO 10218-2 Einfehlersicherheit mit partieller Fehlererkennung gefordert. Gleichzeitig wird auch der Hinweis gegeben, dass diese Anforderungen durch Maßnahmen nach EN ISO 13849-1 oder EN 62061 erfüllt werden. Dabei wird folgende sicherheitsbezogene Leistungsfähigkeit der Steuerung genannt:
PLd (Performance Level d) in Verbindung mit Struktur Kategorie 3 oder
SIL 2 (Safety Integrity Level 2) in Verbindung mit Hardware Fehlertoleranz 1.
Diese Anforderungen bedingen in den meisten Fällen eine zweikanalige Steuerungsstruktur entsprechend Abbildung 29. Somit sind der freien Auswahl der Kategorie bzw. PL oder SIL mittels Risikograph (Abbildung 30) Grenzen gesetzt.
Im begründeten Einzelfall darf aufgrund einer umfassenden Risikobeurteilung für das Robotersystem und dessen Anwendung von diesen Vorgaben abgewichen werden. Bei der Auswahl einer alternativen Steuerungskategorie / PL / SIL können die Risikographen nach EN ISO 13849-1 zu Hilfe genommen werden (Abbildung 30).
Die sicherheitsbezogenen Teile von Steuerungen umfassen z. B.:
Elektrische Verriegelungen von Schutzeinrichtungen
Zustimmungsschalter
Begrenzungen bzw. Überwachung des Bewegungsbereiches von Robotern
Begrenzung bzw. Überwachung der Geschwindigkeit
Begrenzung bzw. Überwachung der Kraft bei kollaborierenden Robotern
Signale von Lichtvorhängen
Not-Halt
Sicherheitshalt
Betriebsartenwahlschalter
Beispiele zur Bestimmung des Performance Levels siehe Abschnitt 4.3
4.1.4 Sicher überwachte Robotersteuerung
Ein sicheres elektronisches Schutzsystem auf der Basis von Mikroprozessoren bietet gegenüber kontaktbehafteter elektromechanischer Technik eine Reihe von Vorteilen, z. B.:
Kein Verschleißen von Endschaltern
Bessere Diagnosemöglichkeiten
Kürzere Reaktionszeiten möglich.
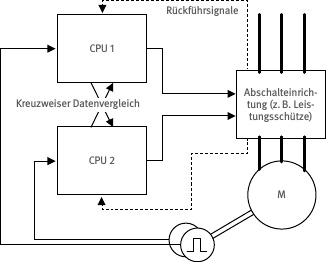
Die für Produktionsaufgaben konzipierte elektronische Programmsteuerung (Anwenderprogramm) erfüllt jedoch in der Regel nicht die Sicherheitsanforderungen (siehe Abschnitt 4.1.3). Dazu ist ein unabhängiges übergeordnetes zweikanaliges Schutzsystem erforderlich. Der technische Aufwand dafür galt lange als nicht vertretbar. Neue leistungsfähige Mikroprozessoren ermöglichten aber auch die sichere Überwachung von Industrierobotern.
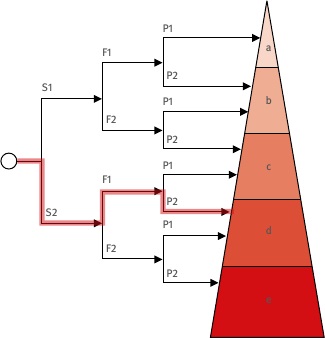
Legende
S | = | Schwere der Verletzung |
---|---|---|
S1 | = | Leichte (üblicherweise reversible Verletzung) |
S2 | = | Ernste (üblicherweise irreversible Verletzung) |
F | = | Häufigkeit und/oder Dauer der Gefährdungsexposition |
F1 | = | Selten bis weniger häufig und/oder die Zeit der Gefährdungsexposition ist kurz |
F2 | = | Häufig bis dauernd und/oder die Zeit der Gefährdungsexposition ist lang |
P | = | Möglichkeit zur Vermeidung der Gefährdung oder Begrenzung des Schadens |
P1 | = | Möglich unter bestimmten Bedingungen |
P2 | = | Kaum möglich |
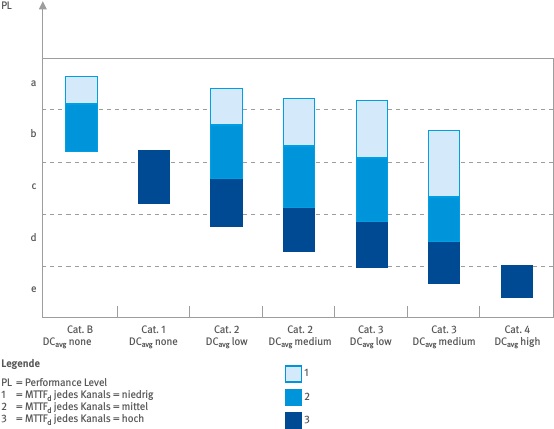
Folgende Sicherheitsfunktionen sind heute bei den meisten Roboterherstellern verfügbar:
Sicher reduzierte Geschwindigkeit, z. B. Überwachung des Werkzeugaufnahmeflansches beim Einrichten mit 250 mm/s oder beim kollaborierenden Betrieb.
Sichere kartesische Begrenzung des Bewegungsraums, z. B. zur sicheren Begrenzung des Bewegungsbereiches bzw. zur Festlegung eines eingeschränkten Raums (siehe Abschnitt 4.2.1.3).
Sichere achsspezifische Begrenzung des Bewegungsraums, z. B. zur sicheren Begrenzung des Bewegungsbereiches bzw. zur Festlegung eines eingeschränkten Raums (siehe Abschnitt 4.2.1.3).
Sicher überwachter Stillstand, z. B. durch Auslösen von Schutzeinrichtungen (siehe Abschnit 4.1.5).
Sichere Bremsrampen, z. B. für Not-Halt, Zustimmungsschalter.
Für kollaborierende Roboter in der Funktion Power and Force Limiting ist zusätzlich eine sicher überwachte Kraftbegrenzung erforderlich.
4.1.5 Sicherheitshalt
Jeder Industrieroboter muss eine Möglichkeit für den Anschluss externer Schutzeinrichtungen haben, z. B. zum Anschluss von Lichtvorhängen und Schutztürschaltern. Dieses Interface wird als Sicherheitshalt-Eingang bezeichnet. Es muss zusätzlich zum Not-Halt-Eingang physikalisch vorhanden sein, z. B. durch zusätzliche Klemmen.
Die Stoppreaktion des Roboters bei einem Sicherheitshalt muss entsprechend EN 60204-1 in Stoppkategorie 0 oder 1 erfolgen [9]. Stoppkategorie 2 darf zusätzlich verwendet werden, wenn der Stillstand sicher überwacht wird.
4.1.6 Not-Halt
Industrieroboter müssen mit einer oder mehreren Not-Halt-Einrichtung(en) ausgerüstet sein. Gleichzeitig muss eine Möglichkeit für den Anschluss der externen Not-Halt-Einrichtungen vorgesehen sein, z. B. Klemme.
Die Bezeichnung "Not-Aus" wie z. B. in der früheren EN 775 darf für Neuanlagen nicht mehr verwendet werden. Not-Aus ist reserviert für elektrische (galvanische) Trennung von der Energieversorgung.
Die Ausführung der Not-Halt-Kreise muss in sicherer Technik entsprechend EN 60204-1 erfolgen. Die funktionale Sicherheit des Not-Halt-Kreises ist nach EN ISO 10218-1 in Einfehlersicherheit auszulegen (siehe Abschnitt 4.1.3). Not-Halt-Einrichtungen müssen gut sichtbar und leicht erreichbar sein. Sie müssen mindestens an jedem Bedienplatz vorgesehen werden.
Nach Entriegelung des Not-Halt-Befehlsgerätes darf die Anlage nicht unmittelbar wieder anlaufen. Erst nach Betätigung einer weiteren Starteinrichtung darf der Wiederanlauf erfolgen.
4.1.7 Anlagen-Not-Halt
Im Normalfall ist die Not-Halt-Schaltung so auszuführen, dass bei Betätigung des Not-Halts die gefährlichen Bewegungen und die gefährlichen Prozessfunktionen der gesamten Anlage stillgesetzt werden. Bei sehr weiträumigen Roboteranlagen ist es zulässig, die Not-Halt-Einrichtungen in bestimmte Teilbereiche aufzuteilen (siehe auch EN ISO 11161). Voraussetzung ist, dass diese aufgrund der konstruktiven Anordnung der Anlage als Teilbereiche erkennbar sind. Zusätzlich sind Hinweisschilder an den Not-Halt-Befehlsgeräten anzubringen. Das Personal muss durch entsprechende Schulungen mit der Wirkungsweise dieser Not-Halt-Einrichtungen vertraut sein.
Besonderes Augenmerk ist auf die Schnittstellen zu benachbarten Anlagenteilen zu richten. Gegebenenfalls müssen die Not-Halt-Kreise an den Schnittstellen auch auf benachbarte Anlagenteile wirken, wenn z. B. deren Weiterbetrieb eine Gefahr darstellt (z. B. Fördertechnik). Hierzu siehe auch Abschnitt 2.3.
4.1.8 Programmierhandgerät
Jedes Programmierhandgerät (PHG) muss mit einer Not-Halt-Einrichtung versehen sein. Die in der beweglichen Zuleitung des PHG untergebrachten sicherheitsrelevanten Leitungen, z. B. Not-Halt und Zustimmungseinrichtung, müssen gegen Kurz- und Querschluss geschützt sein, z. B. durch Redundanz und Überwachung.
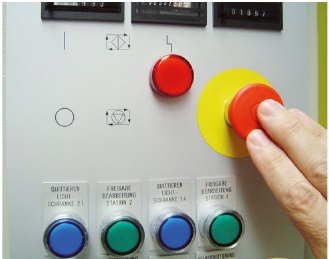

In der Praxis sieht man gelegentlich Programmierhandgeräte mit grauen Not-Halt-Stellteilen. Diese sind nach EN ISO 10218-1 nicht zulässig. Not-Halt-Einrichtungen müssen auf gelbem Hintergrund rot gekennzeichnet sein. Auch über Funk betriebene Programmierhandgeräte müssen eine vollwertig wirksame Not-Halt-Einrichtung haben, die ebenfalls rot/gelb gekennzeichnet sein muss.
Steckbare PHGs müssen, wenn sie nicht angeschlossen sind, so aufbewahrt werden, dass eine irrtümliche Betätigung des darauf befindlichen, dann unwirksamen Not-Halt-Befehlsgerätes vermieden wird. Der Anlagenlieferant muss darauf in der Betriebsanleitung hinweisen. Entsprechend muss der Betreiber der Anlage die Beschäftigten unterweisen.
Bei verketteten Anlagen mit mehreren Robotern ist es u. U. erforderlich, das Programmierhandgerät während des laufenden Betriebes abzuziehen, weil es an einer anderen Station oder für einen anderen Roboter benötigt wird. Ohne zusätzliche schaltungstechnische Maßnahmen würde das Abziehen des Steckers zum sofortigen Stillstand der gesamten Anlage führen. Grund ist die als Ruhestromkreis ausgeführte Not-Halt-Einrichtung auf dem PHG. Eine Schaltung zum kurzzeitigen Überbrücken des betreffenden Not-Halt-Stromkreises ist dann erforderlich. In den einschlägigen Normen existieren keine Vorgaben darüber, wie eine solche Schaltung auszuführen ist. Jedoch sollte im Rahmen der Risikobeurteilung auch das Klemmen von Tastern, die zur Überbrückung verwendet werden, bedacht werden, ebenso wie das bewusste Festsetzen aus Bequemlichkeitsgründen.
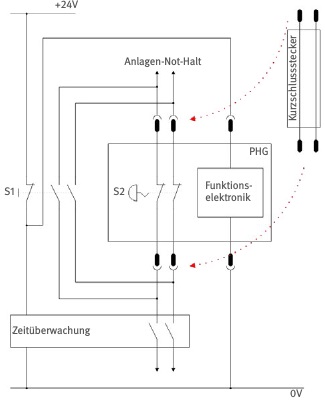
Eine Überwachung des Zeitablaufs ist daher in jedem Fall sinnvoll. Abbildung 34 zeigt ein Schaltungsbeispiel mit Blindstecker (Kurzschlussstecker). Da die Zeitüberwachung keinen direkten Einfluss auf die Sicherheitsfunktion hat, kann ein rückfallverzögertes Relais oder ein elektronisches Betriebsmittel (z. B. SPS) verwendet werden. Potenzialtrennung ist zu beachten. Die Zeiteinstellung sollte dem Umsteckvorgang genügend Zeit einräumen (z. B. einige Minuten), so dass es nicht zu Fehlabschaltungen kommt.
4.1.9 Schnellstmögliches Stillsetzen
Die Maschinenrichtlinie und EN 60204-1 verlangen übereinstimmend für die Anwendung der Stoppfunktionen für Not-Halt ein schnellstmögliches Stillsetzen. Der Begriff "schnellstmöglich" ist jedoch dehnbar und verlangt zusätzliche Überlegungen.
Die Verknüpfung der Not-Halt- oder Schutztürsignale mit der sofortigen Energietrennung (Stoppkategorie 0) und dem gleichzeitigen Einfallen der mechanischen Haltebremsen kann einen schnellen Bremsvorgang bewirken, führt aber zum Verschleißen der Bremsen. Dies beeinträchtigt die Sicherheit der Anlage. Ein gesteuertes Stillsetzen, bei dem die Energie zu den Maschinenantriebselementen beibehalten wird, um das Stillsetzen zu erzielen, schont die Maschine. Die Energie wird erst dann unterbrochen, wenn der Stillstand erreicht ist (Stoppkategorie 1). Jedoch ist die für das Bremsen erforderliche Antriebselektronik normalerweise sicherheitstechnisch nicht ertüchtigt. Der Fehlerfall, bei dem diese Elektronik im Moment des Not-Halts oder Öffnens der Schutztür versagt, ist zwar unwahrscheinlich, aber nicht auszuschließen. In der Folge könnte es zum unkontrollierten Austrudeln oder Weiterbeschleunigen der Antriebe kommen.
Stoppfunktion | Beschreibung | Eignung für Sicherheitsfunktionen |
---|---|---|
Stoppkategorie 0 | Stillsetzen durch sofortiges Abschalten der Energie zu den Maschinen-Antriebselementen | ja |
Stoppkategorie 1 | Gesteuertes Stillsetzen, wobei die Energie zu den Maschinen-Antriebselementen beibehalten wird, um das Stillsetzen zu erzielen. Die Energie wird erst dann unterbrochen, wenn der Stillstand erreicht ist. | ja |
Stoppkategorie 2 | Gesteuertes Stillsetzen, wobei die Energie zu den Maschinen-Antriebselementen beibehalten wird | ja, jedoch mit zusätzlichen Maßnahmen |
Tab. 3 Stoppfunktionen nach EN 60204-1
Da die Antriebsregelelektronik auch während des normalen Betriebes zum Einsatz kommt, geht man davon aus, dass sich derartige Fehler schon während der Produktion durch Störungen bemerkbar machen. Derzeit sind sichere Zeitüberwachungen der Bremsrampen noch ausreichend. Neuere Steuerungen verfügen jedoch schon über sogenannte Bremsrampenüberwachungen, welche auch den Verlauf der Bremsrampe überwachen können.
Welche zeitliche Funktion für das elektronisch geregelte Stillsetzen gewählt wird, ist nach den geltenden Normen nicht vorgegeben. Ein Stillsetzen auf einer geometrischen Bahn ist ebenso zulässig wie ein Stillsetzen an der Stromgrenze. Die Entscheidung bleibt der Risikobetrachtung des Herstellers überlassen. Die Energietrennung nach der vorgesehenen Zeit muss sichergestellt sein. Dies verlangt sichere Zeitglieder.
Beim Zustimmungsschalter sollte Stoppkategorie 0 oder Stoppkategorie 1 mit überwachter Bremsrampe gewählt werden.
4.1.10 Achsbegrenzungen
Nach EN ISO 10218-1 muss mindestens die Grundachse, d. h. die Achse mit der größten Auslenkung, mit der Möglichkeit zur Anbringung mechanischer Festanschläge ausgestattet sein. Für die Achsen zwei und drei (die Achsen mit der zweit- und drittgrößten Auslenkung) muss die Möglichkeit vorgesehen werden, mechanische, elektromechanische oder elektronische Achsbegrenzungen vorzusehen.
Wo und mit welchem Radius personensichere Achsbegrenzungen vorzusehen sind, hängt von der Risikoanalyse der Anlage ab. Dabei ist der nach EN ISO 10218-1 definierte sogenannte eingeschränkte Raum festzulegen:
Maximaler Raum: Raum, der von beweglichen Teilen des Roboters erreicht werden kann, wie vom Hersteller definiert, und zusätzlich der Raum, der vom Endeffektor und dem Werkstück erreicht werden kann.
Eingeschränkter Raum: Anteil des maximalen Raumes, der durch Begrenzungseinrichtungen eingeschränkt ist, die die unüberschreitbaren Grenzen darstellen.
Begrenzungseinrichtungen mittels Steuerungstechnik müssen in sicherer Technik ausgeführt sein (siehe Abschnitt 4.1.3).
Bei Neuanlagen kommen Achsbegrenzungen wie in Abbildung 35 gezeigt heute nur noch vereinzelt zum Einsatz. Meistens werden sicher überwachte Robotersteuerungen genutzt (siehe Abschnitt 4.2.1.3).
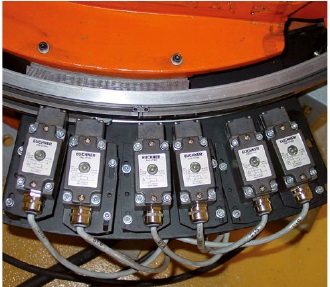