Abschnitt 1.5 - 1.5 Planning the works
Accidents most often occur because of no or insufficient organizational preparation of the maintenance works. Implementing the works when being pressed for time is another reason. Furthermore, often only repair work is performed instead of determining and remedying the reasons for the failure. Moreover, years of routine can lead to overestimation of one’s own capabilities or to misinterpretations, if the practiced way of working is no longer challenged.
A precondition for safe maintenance works is planning the works thoroughly, including the execution of a risk assessment and considering or preparing maintenance instructions.
Planning comprises:
the scope and the course of the maintenance procedure,
required protective measures according to the risk assessment,
the selection of maintenance technicians according to their qualification,
the required number of maintenance technicians according to the extent of the work to be performed, and
the work equipment to be used, such as tools and devices.
When determining the work steps, possible hazards have to be minimized by protective measures. If new hazards occur during the works, they have to be minimized as well by risk assessment and additional protective measures.
The maintenance instructions should include at least the following:
notices on systematic troubleshooting (see section 3),
provision of components that may need to be replaced, special tools, and aids,
securing the circuit breaker of the energy supply, for example electrical, hydraulic, pneumatic,
reduction of residual energies (in connected parts as well),
supporting elevated loads,
method(s) for depressurizing the system,
checking the depressurized condition,
if required, further protective measures to be taken (see Annex 1 letter B).
Safe access to the points of contact and to safe standing surfaces has to be provided for performing the maintenance works, e. g. work platforms, other platforms.
The most important safety measures for maintaining hydraulic systems can be summarized in the five-finger rule of fluid power technology:
![]() | Note |
---|---|
Five-finger rule of fluid power technology
|
If several persons work together during the maintenance work on a hydraulic system, one of them has to be held responsible for determining, monitoring and coordinating the work and the protective measures.
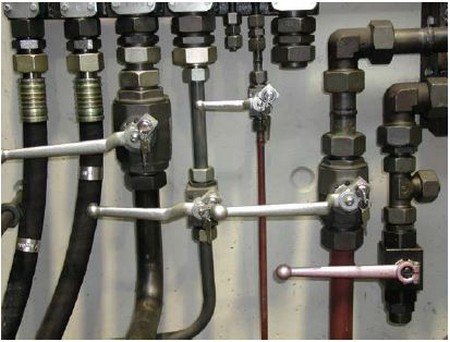
Fig. 3
Securing against unintentional re-closing by lockable ball valves.
Along with the direct hazards caused by the hydraulic system, secondary hazards have to be taken into consideration as well, e. g. risks of falling from heights.
In order to improve occupational safety for maintenance works on a systematic basis
the causes of faults and failures should be documented and evaluated,
the implementation and effectiveness of measures taken should be checked,
work implemented should be documented,
risk assessments and maintenance instructions should be checked and updated, if required, and
any technical modifications implemented should be recorded in the documentation of the machine or system.