Anhang 1 TRG 802
1. Benennungen und Zeichen, die in diesem Anhang verwendet werden
1.1. Streckgrenze
Im Sinne dieser Richtlinie werden bei der Berechnung der drucktragenden Teile folgende Streckgrenzwerte verwendet:
für Aluminiumlegierungen, die konventionelle 0,2-%-Dehngrenze Rp0,2, d.h. diejenige Spannung, bei der eine nichtproportionale Dehnung der Probe von 0,2 % der Meßlänge auftritt;
für unlegiertes Aluminium in weichem Zustand die nichtproportionale 1-%-Dehngrenze.
1.2. Im Sinne dieser Richtlinie ist "Berstüberdruck" der Druck, bei dem plastische Instabilität eintritt, d.h. der höchste Druck, der bei einem Innendruckversuch erreicht wird.
1.3. Die in diesem Anhang verwendeten Zeichen haben folgende Bedeutung:
Ph = | Prüfüberdruck bei der Wasserdruckprüfung in bar; |
---|---|
Pr = | beim Berstversuch gemessener Berstüberdruck der Flasche in bar; |
Prt = | rechnerischer theoretischer Mindestberstüberdruck in bar; |
Re = | Mindestwert der vom Hersteller der Flasche gewährleisteten Streckgrenze in N/mm2; |
Rm = | Mindestwert der vom Hersteller der Flasche garantierten Zugfestigkeit in N/mm2; |
a = | berechnete Mindest-Wanddicke des zylindrischen Teils in mm; |
D = | Nenn-Außendurchmesser der Flasche in mm; |
Rmt = | tatsächliche Zugfestigkeit in N/mm2; |
d = | Durchmesser des Dornes für die Faltversuche in mm |
2. Technische Vorschriften
2.1. Werkstoffe, Wärmebehandlungen und mechanische Behandlungen
2.1.1. Eine Aluminiumlegierung oder unlegiertes Aluminium wird durch die Art der Herstellung, die nominale chemische Zusammensetzung und die Wärmebehandlung der Flasche sowie deren Korrosionsbeständigkeit und mechanische Eigenschaften definiert. Der Hersteller macht die jeweiligen Angaben unter Berücksichtigung der nachstehenden Vorschriften. Jede änderung bezüglich dieser Angaben gilt unter dem Gesichtspunkt der EWG-Bauartzulassung als Wechsel des Werkstoffes.
2.1.2. Zulässig für die Herstellung der Flaschen sind
- a.
unlegiertes Aluminium mit einem Aluminiumgehalt von mindestens 99,5 %;
- b.
Aluminiumlegierungen, deren chemische Zusammensetzung der nachstehenden
Tabelle 1 entspricht und die den in Tabelle 2 aufgeführten Wärmebehandlungen und mechanischen Behandlungen unterzogen worden sind.
Tabelle 1
Chemische Zusammensetzung in % | |||||||||||
---|---|---|---|---|---|---|---|---|---|---|---|
Cu | Mg | Si | Fe | Mn | Zn | Cr | Ti+Zr | Ti | andere insgesamt | Al | |
Legierung B | |||||||||||
min | - | 4,0 | - | - | 0,5 | - | - | - | - | Rest | |
max | 0,10 | 5,1 | 0,5 | 0,5 | 1,0 | 0,2 | 0,25 | 0,20 | 0,10 | 0,15 | |
Legierung C | |||||||||||
min | - | 0,6 | 0,7 | - | 0,4 | - | - | - | - | Rest | |
max | 0,10 | 1,2 | 1,3 | 0,5 | 1,0 | 0,2 | 0,25 | - | 0,10 | 0,15 |
Tabelle 2
Wärmebehandlungen und mechanische Behandlungen | |
---|---|
Legierung B | In folgender Reihenfolge: 1. Korrosionshemmende Behandlung des Rohlings
2. Tiefziehen mit Kaltumformgrad von höchstens 30 % 3. Formung der Flaschenschulter: Die Temperatur des Werkstoffs muß am Ende des Formvorgangs mindestens 300 °C betragen |
Legierung C | 1. Lösungsglühen vor dem Abschrecken:
2. Abschrecken in Wasser 3. Anlassen:
|
c) Für die Herstellung der Flaschen kann jede andere Aluminiumlegierung verwendet werden, vorausgesetzt, daß sie vorher die Korrosionsprüfungen mit Erfolg durchlaufen hat, die in Anhang II aufgeführt sind.
2.1.3. Der Flaschenhersteller hat die Atteste der Schmelzenanalyse der für die Flaschenherstellung verwendeten Werkstoffe zu beschaffen und zu liefern.
2.1.4. Es muß die Möglichkeit zu unabhängigen Analysen gegeben sein. Die Proben für diese Analysen sind entweder dem Halbfertigerzeugnis, wie es dem Flaschenhersteller angeliefert wird, oder den fertigen Flaschen zu entnehmen. Werden die Proben einer Flasche entnommen, so kann hierfür eine der Flaschen verwendet werden, die zuvor für die unter Nummer 3.1 vorgesehenen mechanischen Prüfungen oder die unter Nummer 3.2 genannte Berstprüfung mit Wasser ausgewählt wurden.
2.1.5. Wärmebehandlung und mechanische Behandlung der unter Nummer 2.1.2 Buchstaben b) und c) genannten Legierungen.
2.1.5.1. Der Fertigungsprozess, mit Ausnahme der Endbearbeitung, wird durch ein Abschrecken mit nachfolgendem Anlassen abgeschlossen.
2.1.5.1.1. Der Hersteller muß die Kennwerte für die von ihm durchgeführte abschließende Behandlung angeben, nämlich:
Nenntemperaturen für Lösungsglühen und Anlassen;
Nenndauer der tatsächlichen Verweilzeit bei der Temperatur des Lösungsglühens und bei Anlaßtemperatur.
Der Hersteller muß bei der Wärmebehandlung diese Kennwerte in folgenden Grenzen einhalten:
Temperatur für Lösungsglühen: auf ± 5 °C genau;
Anlaßtemperatur: auf ± 5 °C genau;
tatsächliche Verweilzeit: auf ± 10 % genau.
2.1.5.1.2. Der Hersteller kann jedoch für das Lösungsglühen und das Anlassen auch einen Temperaturbereich angeben, bei dem der Abstand zwischen Höchst - und Mindesttemperatur höchstens 20 °C beträgt. Für jeden dieser Eckwerte gibt er die Nenndauer der tatsächlichen Verweilzeit an.
Für jeden Temperaturzwischenwert wird die Nenndauer der tatsächlichen Verweilzeit für die Dauer des Lösungsglühens durch lineare Interpolation und für die Dauer des Anlassens durch lineare Interpolation des Logarithmus der Zeit ermittelt.
Der Hersteller muß bei der Wärmebehandlung bei einer im angegebenen Bereich liegenden Temperatur die nach dem obigen Verfahren errechnete Nenndauer der tatsächlichen Verweilzeit auf 10 % genau einhalten.
2.1.5.1.3. Der Hersteller muß in den Unterlagen, die er bei der EWG-Prüfung vorlegt, die Kennwerte der von ihm durchgeführten abschließenden Wärmebehandlung angeben.
2.1.5.1.4. Außer der abschließenden Wärmebehandlung muß der Hersteller auch alle bei Temperaturen über 200 °C durchgeführten Wärmebehandlungen angeben.
2.1.5.2. Der Fertigungsprozess umfaßt kein Abschrecken mit nachfolgendem Anlassen.
2.1.5.2.1. Der Hersteller muß die Kennwerte der letzten bei einer Temperatur über 200 °C durchgeführten Wärmebehandlung angeben, wobei erforderlichenfalls zwischen den verschiedenen Teilen der Flasche zu unterscheiden ist.
Er muß ferner jeden Umformvorgang (z. B. Fließpressen, Tiefziehen, Formen der Flaschenschulter) angeben, bei dem die Temperatur des Werkstoffs nicht über 200 °C angestiegen ist und an den sich keine Wärmebehandlung bei Temperaturen über diesem Wert angeschlossen hat; außerdem muß er die Lage des Teiles der Flasche mit der stärksten Kaltverformung und den entsprechenden Kaltumformgrad angeben. Im Sinne dieser Bestimmung gilt als Kaltumformgrad das Verhältnis (S-s,) /s, wobei S der Ausgangsquerschnitt und s der Endquerschnitt ist.
Der Hersteller muß diese Kennwerte der Wärmebehandlung und des Umformvorgangs in folgenden Grenzen einhalten:
Dauer der Wärmebehandlung auf ± 10 % genau und die Temperatur auf ± 5 °C genau;
Kaltumformgrad des Teils der Flasche mit der stärksten Kaltverformung auf ± 6 % genau bei Flaschendurchmessern bis 100 mm und auf ± 3 % genau bei Flaschendurchmessern über 100 mm.
2.1.5.2.2. Der Hersteller kann jedoch für die Wärmebehandlung auch einen Temperaturbereich angeben, bei dem der Abstand zwischen Höchst - und Mindesttemperatur höchstens 20 °C beträgt. Für jeden dieser Eckwerte gibt er die Nenndauer der tatsächlichen Verweilzeit an. Für jeden Temperaturzwischenwert wird die Nenndauer der tatsächlichen Verweilzeit durch lineare Interpolation ermittelt. Der Hersteller muß bei der Wärmebehandlung bei einer im angegebenen Bereich liegenden Temperatur die nach dem obigen Verfahren errechnete Nenndauer der tatsächlichen Verweilzeit auf 10 % genau einhalten.
2.1.5.2.3. Der Hersteller muß in den Unterlagen, die er bei der EWG-Prüfung vorlegt, die Kennwerte der von ihm durchgeführten letzten Wärmebehandlung sowie des Umformvorgangs angeben.
2.1.5.3. Hat sich der Hersteller bei der Wärmebehandlung für die Angabe eines Temperaturbereichs im Sinne der Nummern 2.1.5.1.2 und 2.1.5.2.2 entschieden, so muß er bei der EWG-Bauartzulassung zwei Serien von Flaschen bereitstellen, von denen die eine aus Flaschen, die bei der niedrigsten der vorgesehenen Temperaturen wärmebehandelt worden sind, und die andere aus Flaschen besteht, die bei der höchsten der vorgesehenen Temperaturen wärmebehandelt worden sind, und zwar mit den entsprechenden kürzesten Verweilzeiten.
2.3. Berechnung der drucktragenden Teile
2.3.1. Die Wanddicke des zylindrischen Teils der Gasflaschen darf nicht kleiner sein als der aus der nachstehenden Formel berechnete Wert:
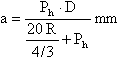
R ist der jeweils kleinere der beiden folgenden Werte:
Re
0,85 · Rm
2.3.2. Die Mindestwanddicke a darf auf keinen Fall kleiner sein als D/100 + 1,5 mm.
2.3.3. Die Wanddicke und die Form des Bodens und der Flaschenschulter müssen derart sein, daß sie die Prüfung nach Nummer 3.2 (Berstprüfung) und Nummer 3.3 (Druckschwellversuch) erfüllen.
2.3.4. Damit eine zufriedenstellende Spannungsverteilung erreicht wird, muß die Wanddicke der Flasche im Bereich der übergangszone zwischen dem zylindrischen Teil und dem Boden stetig erhöht werden, falls der Boden dicker ist als der zylindrische Teil.
2.4. Bau und Ausführung
2.4.1. Der Hersteller muß die Wanddicke sowie innen und außen den Oberflächenzustand jeder Flasche prüfen, um festzustellen, ob
die Wanddicke an keiner Stelle kleiner ist als in der Zeichnung angegeben;
die Innen- und Außenseite der Flasche frei von Fehlern ist, die die Betriebssicherheit der Flasche gefährden können.
2.4.2. Die Unrundheit der zylindrischen Teile muß innerhalb einer Grenze bleiben, die dadurch gegeben ist, daß der Unterschied zwischen dem größten und dem kleinsten Außendurchmesser des gleichen Querschnitts höchstens 1,5 % des mittleren Durchmessers betragen darf. Die Abweichung von den Mantellinien des zylindrischen Teils der Flasche - bezogen auf ihre Länge - darf höchstens 3 mm je Meter betragen.
2.4.3. Vorhandene Flaschenfüße müssen eine ausreichende Festigkeit besitzen und aus einem in bezug auf Korrosion auf den verwendeten Flaschenstahl abgestimmten Werkstoff hergestellt sein. Ihre Form muß der Flasche eine ausreichende Standsicherheit verleihen. Die Flaschenfüße dürfen weder eine Wasseransammlung noch ein Eindringen von Wasser zwischen Fuß und Flasche ermöglichen.
1) ABl. Nr. C 104 vom 13. 9. 1974, S. 75.
2) ABl. Nr. C 5 vom 8. 1. 1975, S. 52.
3) ABl. Nr. C 62 vom 15. 3. 1975, S. 32.
4) Diese Richtlinie ist den Mitgliedstaaten am 26. September 1984 bekanntgegeben worden.
3. Prüfungen
3.1. Mechanische Prüfungen
Die mechanischen Prüfungen werden vorbehaltlich nachstehender Vorschriften gemäß folgenden EURONORMEN durchgeführt:
EURONORM 2-80: Zugversuch bei Stahl;
EURONORM 3-79: Brinell-Härteprüfung;
EURONORM 6-55: Faltversuch bei Stahl;
EURONORM 11-80: Zugversuch an Stahlblechen und -bändern mit einer Dicke unter 3 mm;
EURONORM 12-55: Faltversuch an Stahlblechen und -bändern mit einer Dicke unter 3 mm.
3.1.1. Allgemeine Vorschriften
Alle mechanischen Prüfungen zur Überwachung der Werkstoffeigenschaften der Gasflaschen sind an Werkstoffproben vorzunehmen, die fertigen Flaschen entnommen sind.
3.1.2. Art der Prüfungen und Auswertung der Prüfergebnisse
An jeder Probeflasche werden ein Zugversuch in Längsrichtung und vier Faltversuche in Richtung des Umfangs durchgeführt.
3.1.2.1. Zugversuch
3.1.2.1.1. Die Zugprobe, an der der Zugversuch vorgenommen wird, muß den Bestimmungen
des Kapitels 4 der EURONORM 2-80 entsprechen, wenn ihre Dicke 3 mm oder mehr beträgt;
des Kapitels 4 der EURONORM 11-80 entsprechen, wenn die Dicke weniger als 3 mm beträgt. Unabhängig von der Dicke der Zugprobe betragen die Breite und die Länge der Zugprobe zwischen den Markierungen in diesem Fall 12,5 bzw. 50 mm.
Die beiden Flächen der Zugprobe, die jeweils der Innen - und Außenwandung der Flasche entsprechen, dürfen nicht bearbeitet sein.
3.1.2.1.2.
Bei den unter Nummer 2.1.2 Buchstabe b) genannten C-Legierungen sowie den Legierungen unter Nummer 2.1.2 Buchstabe c) darf die Bruchdehnung nicht geringer als 12 % sein.
Bei den unter Nummer 2.1.2 Buchstabe b) genannten B-Legierungen muß die Bruchdehnung mindestens 12 % betragen, wenn der Zugversuch an einer einzigen, der Flaschenwand entnommenen Probe durchgeführt wird. Der Zugversuch kann auch an vier gleichmäßig über die Flaschenwand verteilten Proben durchgeführt werden. In diesem Fall sind folgende Ergebnisse gefordert:
kein Einzelwert darf unter 11 % liegen;
der Mittelwert der vier Messungen muß mindestens 12 % betragen.
Bei unlegiertem Aluminium darf die Bruchdehnung nicht geringer sein als 12 %.
3.1.2.1.3. Der für die Zugfestigkeit ermittelte Wert muß mindestens Rm sein.
Die im Rahmen der Zugfestigkeitsprüfung zu bestimmende Streckgrenze ist der Wert, der gemäß Nummer 1.1 für die Berechnung der Flaschen verwendet worden ist.
Der für die Streckgrenze ermittelte Wert muß mindestens Re sein.
3.1.2.2. Faltversuch
3.1.2.2.1. Der Faltversuch wird an Faltproben durchgeführt, die man durch Zerschneiden eines Ringes mit einer Breite gleich "3a" in zwei gleiche Teile erhält. Die Breite der Faltprobe darf in keinem Falle kleiner sein als 25 mm. Jeder Streifen darf nur an den Rändern bearbeitet sein. Die Kanten dürfen mit einem Halbwinkel von höchstens 1/10 Probendicke abgerundet oder im Winkel von 45° abgeschrägt sein.
3.1.2.2.2. Der Faltversuch wird mit einem Dorn vom Durchmesser d und zwei Zylindern durchgeführt, die um den Abstand d+3a voneinander entfernt sind. Während des Versuchs muß die Innenfläche des Ringes am Dorn anliegen.
3.1.2.2.3. An der Faltprobe dürfen beim Biegen um einen Dorn keine Risse auftreten, wenn der Abstand der beiden Innenseiten der gefalteten Probe nicht größer ist als der Durchmesser des Dorns (vgl. beschreibendes Schema in Anlage 2).
3.1.2.2.4. Das Verhältnis (n) des Dorndurchmessers zur Wanddicke der Probe darf die Werte der nachstehenden Tabelle nicht überschreiten:
Tatsächliche Zugfestigkeit Rmt in N/mm2 | Wert von n | |
---|---|---|
bis 220 | 5 | |
über 220 | bis 330 | 6 |
über 330 | bis 440 | 7 |
über 440 | 8 |
3.2. Berstprüfung mit Wasser
3.2.1. Versuchsbedingungen
Flaschen, die diesem Versuch unterzogen werden, müssen mit der unter Nummer 6 vorgesehenen Aufschrift versehen sein.
3.2.1.1. Die Berstprüfung mit Wasser ist in zwei aufeinanderfolgenden Stufen mittels einer Prüfeinrichtung durchzuführen, die einen stetigen Druckanstieg bis zum Bersten der Flasche und eine Aufzeichnung der Kurve des Druckverlaufs im Verhältnis zur Zeit erlaubt. Die Prüfung ist bei Raumtemperatur durchzuführen.
3.2.1.2. In der ersten Stufe muß der Druck bis zu dem Wert, der dem Beginn der plastischen Verformung entspricht, stetig ansteigen; der Druckanstieg darf nicht mehr als 5 bar pro Sekunde betragen. Nach Erreichen der plastischen Verformung (zweite Stufe) darf die Fördermenge der Pumpe nicht das Zweifache der Fördermenge der ersten Stufe überschreiten; sie muß dann bis zum Bersten der Flasche konstant gehalten werden.
3.2.2. Auswertung der Versuche
3.2.2.1. Die Auswertung des Wasserdruck-Berstversuchs umfaßt folgendes:
Auswertung der Druck-Zeit-Kurve zur Bestimmung des Berstüberdrucks;
Untersuchung des Risses und der Rißoberfläche;
bei Flaschen mit konkavem Boden Prüfung, ob sich der Boden nicht nach außen gewölbt hat.
3.2.2.2. Der gemessene Berstüberdruck (Pr) muß höher sein als der Wert

3.2.2.3. Der Berstversuch darf nicht zur Folge haben, daß sich von der Flasche Bruchstücke ablösen.
3.2.2.4. Der Hauptriß darf nicht sprödbrüchig sein, d.h. die Bruchkanten dürfen nicht radial verlaufen, sondern müssen gegen die Durchmesserebene geneigt sein und eine Brucheinschnürung aufweisen. Ein Bruch ist nur zulässig, wenn er einer der folgenden Beschreibungsbedingungen entspricht:
Flaschen mit einer Dicke a von höchstens 13 mm
der Bruch muß zum größten Teil im wesentlichen in Längsrichtung verlaufen;
der Bruch darf keine Querrisse aufweisen;
der Bruch darf von der Anbruchstelle aus nach beiden Seiten nicht über 90° des Flaschenumfangs hinausreichen;
der Bruch darf sich nicht auf die Teile der Flasche erstrecken, die dicker sind als das 1,5fache der in halber Höhe der Flasche gemessenen maximalen Wanddicke; bei konvexem Flaschenboden darf der Bruch nicht bis zur Mitte des Flaschenbodens reichen.
Flaschen mit einer Dicke a von mehr als 13 mm:
Der Bruch muß zum größten Teil in Längsrichtung verlaufen.
3.2.2.5. Der Riß darf keine charakteristischen Werkstoffehler erkennen lassen.
3.3. Druckschwellversuch
3.3.1. Flaschen, die diesem Versuch unterzogen werden, müssen mit der unter Nummer 6 vorgesehenen Aufschrift versehen sein.
3.3.2. Der Druckschwellversuch wird an 2 Flaschen, für die der Hersteller die Gewähr übernimmt, daß die konstruktiv vorgesehenen Mindestabmessungen praktisch eingehalten sind, mit einer nicht korrosiv wirkenden Flüssigkeit vorgenommen.
3.3.3. Dieser Versuch wird zyklisch durchgeführt. Der obere zyklische Druck ist entweder gleich dem Druck Ph oder gleich 2/3 des Drucks Ph. Der untere zyklische Druck darf 10 % des oberen zyklischen Drucks nicht überschreiten.
Die Zahl der Lastwechsel und die maximale Frequenz sind der nachstehenden Tabelle zu entnehmen:
Oberer zyklischer Druck | Ph | 2/3 Ph |
---|---|---|
Mindestzahl der Lastwechsel | 12000 | 80000 |
Maximale Frequenz (Lastwechsel pro Minute) | 5 | 12 |
Die an der Außenseite der Flaschenwandung gemessene Temperatur darf während des Versuches 50 °C nicht überschreiten.
Der Versuch gilt als bestanden, wenn die Flasche die vorgeschriebene Zahl der Lastwechsel erreicht, ohne undicht zu werden.
3.4. Wasserdruckprüfung
3.4.1. Der Wasserdruck in der Flasche muß stetig ansteigen, bis der Druck Ph erreicht ist.
3.4.2. Die Flasche verbleibt so lange unter Druck Ph, bis sicher erkannt ist, daß keine Neigung zur Drucksenkung und keine Undichtigkeit besteht.
3.4.3. Nach dem Versuch darf die Flasche keine bleibende Verformung aufweisen. 3.4.4. Flaschen, die den Anforderungen des Versuchs nicht genügen, sind zurückzuweisen.
3.5. Kontrolle der Homogenität einer Flasche
Bei dieser Kontrolle wird geprüft, ob zwei beliebige Punkte auf der Außenfläche der Flasche nicht einen Härteunterschied von mehr als 15 HB aufweisen. Die Kontrolle muß in zwei Flaschenquerschnitten in der Nähe der Flaschenschulter und des Bodens an vier regelmäßig verteilten Punkten vorgenommen werden.
3.6. Kontrolle der Homogenität einer Warenpartie
Bei dieser Kontrolle wird vom Hersteller durch eine Härteprüfung oder ein anderes geeignetes Verfahren geprüft, ob nicht bei der Wahl des Ausgangserzeugnisses oder bei der Durchführung der Wärmebehandlung ein Irrtum unterlaufen ist.
3.7. Kontrolle der Flaschenböden
Durch die Mitte des Flaschenbodens wird ein Längsschnitt gelegt; eine Schnittfläche wird poliert und bei 5- bis 10facher Vergrößerung geprüft.
Die Flasche gilt als fehlerhaft, wenn Risse festzustellen sind. Sie gilt ferner als fehlerhaft, wenn Poren oder Einschlüsse so groß sind, daß dadurch die Sicherheit beeinträchtigt ist.
4. EWG-Bauartzulassung
Die in Artikel 4 der Richtlinie genannte EWG-Bauartzulassung kann sowohl für Flaschentypen als auch für Flaschenfamilien erteilt werden. Als Flaschenfamilien gelten Flaschen, die aus ein und derselben Fabrik stammen und sich nur durch ihre Länge unterscheiden, allerdings im Rahmen der folgenden Abmessungen:
Die kleinste Gesamtlänge muß mindestens dem dreifachen Außendurchmesser der Flasche entsprechen;
die größte Gesamtlänge darf nicht mehr als das 1,5fache der Gesamtlänge der geprüften Flasche betragen.
4.1. Derjenige, der die EWG-Zulassung beantragt, hat für jede Flaschenfamilie die notwendigen Unterlagen für die nachstehend vorgesehenen Prüfungen vorzulegen und dem Mitgliedstaat ein Los von 50 Flaschen oder zwei Lose von je 25 Flaschen nach Nummer 2.1.5.3 bereitzustellen, aus dem oder denen die für die nachstehenden Versuche erforderliche Anzahl Flaschen entnommen wird; außerdem hat er alle ergänzenden Auskünfte zu erteilen, die der Mitgliedstaat anfordert. Der Antragsteller hat insbesondere die Art der Wärmebehandlung und mechanischen Behandlung, die Temperaturen und die Behandlungsdauer nach Nummer 2.1.5 anzugeben. Er hat die Atteste der Schmelzanalyse der für die Flaschenherstellung verwendeten Werkstoffe zu liefern.
4.2. Bei der EWG-Bauartzulassung
4.2.1. prüft der Mitgliedstaat, ob
die Berechnungen nach Nummer 2.3 stimmen;
die Wanddicke der Flaschen den Vorschriften unter Nummer 2.3 genügt, und zwar bei zwei der entnommenen Flaschen, wobei die Messung auf der Ebene von drei Querschnitten sowie auf dem gesamten Umfang des Längsschnittes des Flaschenbodens und der Flaschenschulter vorgenommen wird;
die Bedingungen unter den Nummern 2.1 und 2.4.3 erfüllt sind;
die Vorschriften unter Nummer 2.4.2 bei allen vom Mitgliedstaat entnommenen Flaschen eingehalten wurden;
die Innen - und Außenseiten der Flaschen frei von Fehlern sind, die ihre Betriebssicherheit in Frage stellen
4.2.2. führt der Mitgliedstaat an den ausgewählten Flaschen folgende Prüfungen durch:
die Korrosionsprüfungen: interkristalline Korrosion und Korrosion unter Spannung an 12 Proben gemäß Anhang II,
die unter Nummer 3.1 vorgesehenen Prüfungen an 2 Flaschen, bei einer Flaschenlänge von 1500 mm oder mehr werden jedoch die Zugversuche in Längsrichtung und die Faltversuche an Proben durchgeführt, die aus den oberen und unteren Bereichen der Flaschenwand entnommen sind,
die Prüfung nach Nummer 3.2 an zwei Flaschen,
die Prüfung nach Nummer 3.3 an zwei Flaschen,
die Prüfung nach Nummer 3.5 an einer Flasche,
die Kontrolle nach Nummer 3.7 bei allen entnommenen Flaschen.
4.3. Fallen die Ergebnisse der Prüfungen zufriedenstellend aus, so stellt der Mitgliedstaat die EWG-Bauartzulassungsbescheinigung nach dem Muster in Anhang III aus.
5. EWG-Prüfung
5.1. Der Flaschenhersteller muß der Prüfstelle im Hinblick auf die EWG-Prüfung folgendes vorlegen:
5.1.1. die EWG-Zulassungsbescheinigung;
5.1.2. die Werkatteste für die Schmelzanalyse der zur Herstellung der Flaschen verwendeten Werkstoffe;
5.1.3. die Unterlagen über die Herkunft des Werkstoffes, aus dem die Gasflaschen gefertigt sind;
5.1.4. die Unterlagen über die Wärmebehandlung und die mechanische Behandlung, wobei das gemäß Nummer 2.1.5 angewandte Verfahren anzugeben ist;
5.1.5. eine Liste der Gasflaschen mit den unter Nummer 6 vorgesehenen Zahlen und Aufschriften.
5.2. Bei der EWG-Prüfung
5.2.1. muß die Prüfstelle:
feststellen, ob die EWG-Zulassung erteilt worden ist und die Flaschen mit ihr übereinstimmen;
feststellen, ob die Unterlagen mit den Angaben über die Werkstoffe in Ordnung sind;
prüfen, ob die technischen Vorschriften nach Nummer 2 eingehalten sind, und insbesondere mittels einer äußeren und, wenn möglich, inneren Besichtigung der Flasche, die sich auf mindestens 10 % der hergestellten Flaschen erstrecken muß, prüfen, ob die Herstellung sowie die vom Hersteller gemäß Nummer 2.4.1 durchgeführten Kontrollen als zufriedenstellend angesehen werden können;
an 3 Proben, von denen je eine aus der Flaschenschulter, dem Mittelteil und dem Boden der Flasche entnommen ist, die Korrosionsprüfung (interkristalline Korrosion) an den unter Nummer 2.1.2 Buchstabe c) genannten Legierungen gemäß Nummer 1 des Anhangs II durchführen;
die unter den Nummern 3.1 und 3.2 vorgesehenen Prüfungen durchführen;
die Richtigkeit der vom Hersteller in der Liste nach Nummer 5.1.5 gemachten Angaben prüfen. Diese Prüfung wird stichprobenweise vorgenommen;
die Ergebnisse der vom Hersteller nach Nummer 3.6 durchgeführten Kontrollen der Homogenität des Loses beurteilen.
Fallen die Ergebnisse der Prüfungen zufriedenstellend aus, so stellt die Prüfstelle die EWG-Prüfbescheinigung nach dem Muster in Anhang IV aus.
5.2.2. Für die Durchführung der unter den Nummern 3.1 und 3.2 vorgeschriebenen Prüfungen werden aus jedem Los oder Bruchteil eines Loses von 202 aus derselben Schmelze stammenden Flaschen, bei denen folglich auch die vorgesehene Wärmebehandlung unter gleichen Bedingungen erfolgt ist, zwei Flaschen stichprobenweise entnommen.
Eine Flasche wird den unter Nummer 3.1 vorgeschriebenen Prüfungen (mechanische Prüfungen), die zweite den in Nummer 3.2 vorgeschriebenen Prüfungen (Berstprüfung) unterzogen. Stellt sich heraus, daß ein Fehler bei der Durchführung der Prüfung oder ein Irrtum bei den Messungen unterlaufen ist, so muß die Prüfung wiederholt werden. Ergeben sich bei einer oder mehreren Prüfungen auch nur teilweise unbefriedigende Resultate, so ist die Ursache dafür vom Hersteller unter Aufsicht der Prüfstelle zu suchen.
5.2.2.1. Sind die unbefriedigenden Resultate nicht auf die Wärmebehandlung zurückzuführen, so wird das Los zurückgewiesen.
5.2.2.2. Sind die unbefriedigenden Resultate auf die Wärmebehandlung zurückzuführen, so kann der Hersteller sämtliche Flaschen des Loses einer weiteren Wärmebehandlung unterziehen. Diese Behandlung darf nur einmal erfolgen.
In diesem Fall:
führt der Hersteller die unter Nummer 3.6 vorgesehene Kontrolle durch;
führt die Prüfstelle sämtliche unter Nummer 5.2.2 vorgesehenen Prüfungen durch.
Die Ergebnisse der nach dieser neuen Behandlung durchgeführten Prüfungen müssen den Vorschriften der Richtlinie entsprechen.
5.2.3. Die Auswahl der Stichproben sowie die Durchführung aller Prüfungen erfolgt im Beisein und unter Aufsicht eines Vertreters der Prüfstelle. Bezüglich der im vierten Gedankenstrich der Nummer 5.2.1 vorgesehenen Prüfung kann sich die zugelassene Stelle jedoch darauf beschränken, nur bei der Auswahl der Proben und bei der Prüfung der Ergebnisse anwesend zu sein.
5.2.4. Sind alle vorgeschriebenen Versuche durchgeführt worden, so werden alle Flaschen des Loses im Beisein und unter Aufsicht eines Vertreters der Prüfstelle einer Wasserdruckprüfung gemäß Nummer 3.4 unterzogen.
5.3. Befreiung von der EWG-Prüfung
Bei den unter Artikel 4 dieser Richtlinie fallenden Flaschen werden gemäß Artikel 15 Buchstabe a) der Richtlinie 76/767/EWG alle unter Nummer 5.2 vorgesehenen Prüfungen und Kontrollen vom Hersteller unter seiner Verantwortung durchgeführt.
Der Hersteller hält alle in der EWG-Bauartzulassung aufgeführten Unterlagen sowie die Prüf - und Kontrollprotokolle zur Verfügung der Prüfstelle.
6. Zeichen und Aufschriften
Die unter dieser Nummer vorgesehenen Zeichen und Aufschriften werden auf der Flaschenschulter angebracht.
Bei Flaschen mit einem Rauminhalt von höchstens 15 Litern können die Zeichen und Aufschriften entweder auf der Flaschenschulter oder auf einem ausreichend verstärkten anderen Teil der Flasche angebracht werden. Bei Flaschen mit einem Durchmesser von weniger als 75 mm müssen die Zeichen 3 mm hoch sein.
Abweichend von Nummer 3 des Anhangs I der Richtlinie 76/767/EWG bringt der Hersteller das EWG-Bauartzulassungszeichen in folgender Reihenfolge an:
bei den unter Artikel 4 fallenden Flaschen
stilisierter Buchstabe e;
Kennzahl 2 dieser Richtlinie;
Kennbuchstaben (ein oder mehrere Großbuchstaben) des Mitgliedstaats, der die EWG-Zulassung erteilt hat, und die beiden letzten Zahlen der Jahreszahl der Zulassung;
Kennummer der EWG-Zulassung
(Beispiel: e 2 D 79 45);
bei den nur der EWG-Zulassung unterliegenden Flaschen;
stilisierter Buchstabe e, umrahmt von einem Sechseck;
Kennzahl 2 dieser Richtlinie;
Kennbuchstaben (ein oder mehrere Großbuchstaben) des Mitgliedstaats,
der die EWG-Zulassung erteilt hat, und die beiden letzten Zahlen der Jahreszahl der Zulassung;Kennummer der EWG-Zulassung
(Beispiel:2 D 79 54).
Abweichend von Nummer 3 des Anhangs II der Richtlinie 76/767/EWG bringt die Prüfstelle das EWG-Prüfzeichen in folgender Reihenfolge an:
Kleinbuchstaben " e ";
Kennbuchstaben (ein oder mehrere Großbuchstaben) des Mitgliedstaats, in dem die Prüfung erfolgt ist, erforderlichenfalls zusammen mit einer oder zwei Zahlen zur Angabe einer gebietsmäßigen Untergliederung;
Zeichen der Prüfstelle, das vom Kontrollbediensteten angebracht wird und gegebenenfalls durch dessen Zeichen zu ergänzen ist;
Sechseck;
Prüfungsdatum: Jahr, Monat,
(Beispiel: e D 12 4880/01).
6.1. Aufschriften betreffend die Herstellung
6.1.1. Werkstoff
Zahl zur Angabe des der Berechnung zugrunde gelegten Wertes von R in N/mm2.
6.1.2. Wasserdruckprüfung
Wert des Prüfüberdrucks in bar, gefolgt von dem Symbol "bar".
6.1.3. Flaschentyp
Leergewicht der Flasche, einschließlich der mit der Flasche fest verbundenen Teile, ohne Absperrventil, in Kilogramm und vom Hersteller garantierter Mindestrauminhalt der Flasche in Litern.
Leergewicht und Rauminhalt sind auf eine Dezimalstelle genau anzugeben. Der betreffende Wert ist beim Rauminhalt abzurunden, beim Gewicht aufzurunden.
6.1.4. Herkunft der Flasche
Großbuchstabe(n) zur Kennzeichnung des Herkunftslandes, gefolgt vom Herstellerzeichen und der Fabrikationsnummer.
6.2. Ein als Beispiel dienendes Schema der Zeichen und Aufschriften ist in Anlage 1 enthalten.(2)